Showa Denko Package Substrate Manufacturer
Showa Denko Package Substrate Manufacturer,Showa Denko Package Substrates (SDPS) represent the pinnacle of innovation and reliability in semiconductor packaging materials. Engineered with precision and expertise, SDPS offers unparalleled thermal conductivity, electrical insulation, et stabilité mécanique, making it the substrate of choice for a wide range of electronic devices.
SDPS is meticulously crafted using advanced manufacturing processes, ensuring consistent quality and performance. Whether it’s ceramic substrates for high-power applications, organic laminates for cost-effective solutions, or metal-based substrates for superior thermal management, SDPS delivers exceptional reliability and functionality.
With fine-pitch wiring capabilities and compatibility with advanced packaging technologies like flip-chip and wire bonding, SDPS empowers designers to push the boundaries of electronics innovation. From smartphones and tablets to automotive electronics and industrial equipment, SDPS plays a crucial role in enabling the next generation of electronic devices to meet the demands of today’s connected world.
Backed by Showa Denko’s commitment to excellence and customer satisfaction, SDPS continues to set the standard for performance, quality, and versatility in semiconductor packaging substrates.
What is a Showa Denko Package Substrate?
A Showa Denko Package Substrate is a type of substrate used in semiconductor packaging. Showa Denko (SDK) is a Japanese company known for its production of advanced materials, including those used in electronic components.
In semiconductor packaging, the substrate serves as a foundation or base for mounting and connecting various electronic components, such as integrated circuits (Ics) or chips. The substrate provides mechanical support, electrical connections, and thermal management for these components.
Showa Denko Package Substrates are designed to meet the demanding requirements of modern semiconductor devices, particularly in terms of electrical performance, conductivité thermique, et fiabilité. They are typically made from materials like ceramic, organic laminate, or metal, depending on the specific application and performance requirements.
These substrates are manufactured using advanced production techniques and quality control measures to ensure consistency and reliability. They may incorporate features such as fine-pitch wiring, multiple layers, and specialized coatings to optimize performance and enable integration with other components in the semiconductor package.
Total, Showa Denko Package Substrates play a critical role in the performance and reliability of semiconductor devices, helping to enable the continued advancement of electronics technology in various applications, from consumer electronics to automotive and industrial systems.
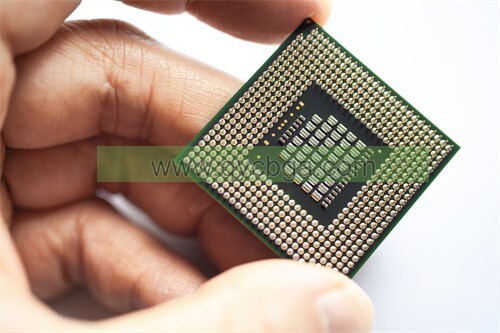
Showa Denko Package Substrate Manufacturer
What are the SDPS Design Guidelines?
Specific design guidelines for Showa Denko Package Substrates (SDPS) may vary depending on the specific product line and application requirements. Toutefois, some general design principles and guidelines typically apply when designing with SDPS. Here are some common design considerations:
- Electrical Performance: Ensure that the substrate design meets the electrical performance requirements of the application, including impedance control, signal integrity, and power distribution.
- Gestion thermique: Incorporate features to facilitate efficient heat dissipation from the semiconductor devices mounted on the substrate. This may include thermal vias, Coussinets thermiques, or heat spreaders.
- Mechanical Integrity: Design the substrate to provide sufficient mechanical support for the components mounted on it, considering factors such as package size, weight, and mounting method.
- Intégrité du signal: Minimize signal distortion and interference by optimizing the routing of high-speed signal traces, Réduire la diaphonie, and adhering to impedance matching guidelines.
- Fabricabilité: Ensure that the substrate design is manufacturable within the capabilities of the chosen fabrication process. Consider factors such as layer count, feature sizes, and material properties.
- Reliability: Design the substrate with reliability in mind, considering factors such as thermal cycling, mechanical stress, and environmental conditions. Incorporate features to enhance the reliability of solder joints and interconnects.
- Compatibility:Ensure compatibility with other components in the semiconductor package, such as ICs, connectors, and housing materials. Verify that the substrate design meets the interface requirements of these components.
- Cost Optimization: Balance performance requirements with cost considerations to achieve an optimal balance between functionality and affordability. Consider factors such as material selection, manufacturing complexity, and yield rates.
- Compliance: Ensure that the substrate design complies with relevant industry standards and regulations, such as IPC (Association Connecting Electronics Industries) standards for PCB design.
- Future Scalability: Anticipate future scalability and evolution of the design by leaving room for additional features, upgrades, or modifications as needed.
These guidelines serve as a starting point for designing with Showa Denko Package Substrates and should be adapted to meet the specific requirements of each application and product. Consulting with Showa Denko or experienced substrate designers can provide additional insights and recommendations tailored to your specific needs.
What is the SDPS Fabrication Process?
The fabrication process for Showa Denko Package Substrates (SDPS) involves several steps to manufacture substrates that meet the required specifications and performance standards. While the exact details may vary depending on the specific substrate type and application, here is a generalized overview of the typical fabrication process:
- Substrate Material Selection: The process begins with the selection of suitable substrate materials based on the desired electrical, thermique, mécanique, and chemical properties. Common substrate materials include ceramics, organic laminates, and metal-based substrates.
- Substrate Preparation: The chosen substrate material undergoes preparation steps such as cleaning, surface treatment, and shaping to ensure it meets the required specifications for size, flatness, and surface finish.
- Layer Formation: For multilayer substrates, the fabrication process involves the formation of individual layers using techniques such as thin-film deposition, printing, or lamination. Each layer may contain conductive traces, dielectric materials, and vias for interconnection.
- Pattern Generation: The conductive traces and circuit patterns are generated on the substrate layers using photolithography, gravure, or other patterning techniques. This step defines the electrical connections and routing on the substrate.
- Via Formation: Vias, which are small holes drilled or etched through the substrate layers, are formed to provide vertical interconnections between different layers. Via formation may involve processes such as laser drilling, mechanical drilling, or chemical etching.
- Finition de surface: The substrate surfaces are finished to enhance solderability, electrical conductivity, and corrosion resistance. Common surface finishes include solder mask application, metal plating, and surface coating.
- Quality Control: Throughout the fabrication process, quality control measures are implemented to ensure the substrates meet the required specifications and performance standards. This may involve inspection, testing, and validation of critical parameters such as dimensional accuracy, electrical continuity, et fiabilité.
- Final Inspection and Packaging: Once fabrication is complete, the finished substrates undergo final inspection to verify their quality and performance. Substrates that pass inspection are packaged and prepared for shipment to customers.
- Additional Processing (Optionnel): Depending on the specific application requirements, additional processing steps such as laser marking, surface texturing, or component attachment may be performed before the substrates are ready for use.
Total, the SDPS fabrication process involves a combination of material preparation, Structuration, interconnection, and finishing steps to produce substrates that meet the demanding requirements of modern semiconductor packaging applications. Continuous improvement and innovation in fabrication techniques are essential to meet the evolving needs of the electronics industry.
How do you manufacture SDPS?
Manufacturing Showa Denko Package Substrates (SDPS) involves a series of intricate processes aimed at producing substrates with precise electrical, mécanique, and thermal properties. Here’s an overview of the general steps involved in manufacturing SDPS:
- Substrate Material Selection: The manufacturing process begins with selecting the appropriate substrate material based on the desired characteristics such as thermal conductivity, electrical insulation, et résistance mécanique. Common materials include ceramics (such as alumina or aluminum nitride), organic laminates, and metal substrates.
- Substrate Preparation: The chosen substrate material undergoes preparation steps to ensure it meets the required specifications. This may include cutting, grinding, and polishing to achieve the desired dimensions, flatness, and surface finish.
- Layer Formation (for Multilayer Substrates): If the SDPS requires multiple layers, each layer is formed using techniques such as screen printing, thin-film deposition, or lamination. These layers may include conductive traces, dielectric materials, and vias for interconnection.
- Patterning: The conductive traces and circuit patterns are defined on the substrate surface using photolithography or other patterning techniques. This step involves applying a photoresist material, l’exposer à la lumière UV à travers un masque, and developing it to create the desired pattern.
- Etching: After patterning, the substrate undergoes etching to remove unwanted material and define the conductive traces and circuit features. Wet or dry etching techniques may be employed depending on the substrate material and pattern complexity.
- Via Formation: Vias are created to establish vertical interconnections between different layers of the substrate. This can be achieved through processes such as laser drilling, mechanical drilling, or chemical etching, depending on the substrate material and via size requirements.
- Finition de surface: The substrate surfaces are finished to improve solderability, electrical conductivity, and corrosion resistance. Common surface finishes include solder mask application, metal plating (e.g., gold or tin), and surface coating (e.g., protective polymer coatings).
- Quality Control: Throughout the manufacturing process, rigorous quality control measures are implemented to ensure that the substrates meet the required specifications and performance standards. This may involve dimensional inspection, electrical testing, and reliability testing to assess factors such as thermal cycling and mechanical stress.
- Final Inspection and Packaging: Once manufacturing is complete, the finished substrates undergo final inspection to verify their quality and performance. Substrates that pass inspection are packaged and prepared for shipment to customers.
- Additional Processing (Optionnel): Depending on specific customer requirements, additional processing steps such as laser marking, surface texturing, or component attachment may be performed before the substrates are ready for use.
Total, the manufacturing of SDPS involves a combination of material preparation, Structuration, interconnection, and finishing processes to produce substrates that meet the demanding requirements of modern semiconductor packaging applications. Continuous improvement and innovation in manufacturing techniques are essential to meet the evolving needs of the electronics industry.
How much should SDPS cost?
The cost of Showa Denko Package Substrates (SDPS) can vary significantly depending on several factors including the substrate material, taille, complexité, quantity ordered, and any additional features or customization required.
- Matériau du substrat: Different substrate materials have different costs associated with them. For example, ceramic substrates tend to be more expensive than organic laminates due to their superior thermal properties and performance.
- Taille et complexité: Larger and more complex substrates typically require more materials and manufacturing processes, which can increase the overall cost.
- Quantity Ordered: Economies of scale often apply in manufacturing, meaning that larger quantities may result in lower unit costs due to bulk discounts and optimized production processes.
- Additional Features or Customization: Any additional features or customization, such as specialized surface finishes, unique patterning, or specific testing requirements, can add to the cost of the substrates.
- Supplier Relationship: Long-term relationships with suppliers, volume commitments, and negotiated contracts can also influence the cost of SDPS.
To get an accurate cost estimate for SDPS, it’s best to contact Showa Denko directly or consult with a supplier who specializes in semiconductor packaging substrates. Ils peuvent fournir des devis en fonction de vos besoins spécifiques et de vos besoins en matière de volume. De plus, considering the total cost of ownership, which includes factors like reliability, performance, and support, is crucial when evaluating the cost-effectiveness of SDPS for your application.
What is SDPS base material?
The base material used in Showa Denko Package Substrates (SDPS) can vary depending on the specific requirements of the application and the desired performance characteristics. Showa Denko offers a range of substrate materials tailored to different semiconductor packaging needs. Here are some common base materials used in SDPS:
- Ceramics: Ceramic materials such as alumina (Al2O3) and aluminum nitride (Aln) are widely used in high-performance SDPS due to their excellent thermal conductivity, electrical insulation properties, et résistance mécanique. Alumina-based substrates are often chosen for their cost-effectiveness and compatibility with a wide range of applications, while aluminum nitride offers superior thermal conductivity for applications requiring enhanced heat dissipation.
- Organic Laminates: Organic laminates, typically made of epoxy resin and reinforced with glass fiber, are commonly used in cost-sensitive SDPS applications. These substrates offer good electrical insulation properties, ease of fabrication, and are suitable for applications where high thermal conductivity is not a primary concern.
- Metal-Based Substrates: Metal-based substrates, such as copper-clad laminates or metal core printed circuit boards (MCPCBs), are used in SDPS applications where high thermal conductivity and excellent heat dissipation are critical requirements. These substrates typically consist of a metal core (e.g., aluminum or copper) with dielectric layers for electrical insulation and circuit routing.
- Composite Materials: Some SDPS may utilize composite materials that combine the benefits of ceramics, organics, and metals to achieve specific performance objectives, such as improved thermal management, Performance électrique, et stabilité mécanique.
The choice of base material for SDPS depends on factors such as thermal management requirements, Performance électrique, Considérations relatives aux coûts, and application-specific needs. Showa Denko offers expertise in material selection and can provide guidance on choosing the most suitable base material for a particular semiconductor packaging application.
Which company manufactures SDPS?
SDPS (Showa Denko Package Substrates) are manufactured by the Japanese company Showa Denko. Showa Denko is a leading chemical and electronics materials company with extensive experience and technical expertise in the semiconductor industry. They offer a variety of high-performance substrate boards for manufacturing and assembly of electronic devices.
Showa Denko employs advanced processes and technologies in the manufacturing of SDPS to ensure product quality and performance. They have advanced material development laboratories and manufacturing facilities capable of customizing various types of substrate boards according to customer requirements, including ceramic substrates, organic laminates, and metal substrates.
As a company manufacturing SDPS, we also have the capability to produce these high-performance substrates. We have advanced manufacturing equipment and a skilled technical team capable of customizing SDPS products to various specifications and requirements as per customer needs. We are committed to providing high-quality, reliable, and high-performance substrate boards to meet customer demands in the semiconductor packaging field.
Our company has extensive experience and expertise to provide comprehensive services from design to production for our customers. Our products comply with international standards and industry requirements, undergoing rigorous quality control and testing to ensure stability and reliability in various application environments.
Whatever the customer’s needs, we can provide customized solutions to meet their specific application requirements. We are committed to establishing long-term partnerships with our customers, fostering mutual development and sharing success.
Quels sont les 7 Qualités d’un bon service à la clientèle?
Good customer service is essential for building and maintaining positive relationships with customers. Here are seven qualities that characterize excellent customer service:
- Réactivité:Un bon service à la clientèle implique de répondre rapidement aux demandes des clients, Préoccupations, et demandes. Being responsive demonstrates that you value the customer’s time and are committed to providing timely assistance.
- Empathie: L’empathie est la capacité de comprendre et de partager les sentiments des autres. Effective customer service representatives empathize with customers’ frustrations or challenges and strive to provide support and solutions that address their needs and concerns.
- Communication claire: Clear communication is vital for ensuring that customers understand the information provided and the actions being taken to assist them. Customer service representatives should communicate clearly, using language that is easy to understand and avoiding jargon or technical terms when possible.
- Professionnalisme: Professionalism encompasses various attributes such as politeness, courtesy, and professionalism. Customer service representatives should conduct themselves in a professional manner, treating customers with respect and maintaining a positive attitude, even in challenging situations.
- Knowledgeability: Good customer service requires a thorough understanding of the products or services being offered, as well as relevant policies and procedures. Knowledgeable representatives can provide accurate information, answer questions effectively, and offer valuable insights or recommendations to customers.
- Compétences en résolution de problèmes: Effective problem-solving skills are essential for resolving customer issues and addressing their concerns efficiently. Customer service representatives should be proactive in identifying solutions, taking ownership of problems, and following through to ensure that issues are resolved to the customer’s satisfaction.
- Follow-Up and Follow-Through: Good customer service doesn’t end with the initial interaction. It involves following up with customers to ensure that their needs have been met and their issues resolved satisfactorily. Following through on commitments and keeping customers informed throughout the resolution process helps build trust and loyalty.
En incarnant ces qualités, businesses can deliver exceptional customer service experiences that foster customer satisfaction, loyalty, and advocacy.
Foire aux questions
What are SDPS and their applications?
SDPS stands for Showa Denko Package Substrates, which are advanced substrate materials used in semiconductor packaging. They are used in various electronic devices, including smartphones, Comprimés, computers, Électronique automobile, and industrial equipment.
What are the advantages of SDPS compared to other substrate materials?
SDPS offer several advantages, including high thermal conductivity, excellent electrical insulation properties, résistance mécanique, et fiabilité. They are also customizable to meet specific application requirements.
What types of SDPS are available?
Showa Denko offers a range of SDPS materials, including ceramic substrates (such as alumina and aluminum nitride), organic laminates, and metal-based substrates. Each type has unique properties and is suitable for different applications.
What are the key features of SDPS?
Key features of SDPS include high thermal conductivity, low thermal expansion coefficient, excellent dielectric properties, fine-pitch wiring capabilities, and compatibility with advanced packaging technologies such as flip-chip and wire bonding.
How are SDPS manufactured?
SDPS are manufactured using advanced processes such as thin-film deposition, photolithography, gravure, and metallization. The exact manufacturing process may vary depending on the substrate material and desired specifications.
What are the reliability and quality assurance measures for SDPS?
SDPS undergo rigorous quality control and testing to ensure reliability and performance consistency. This includes dimensional inspection, electrical testing, thermal cycling testing, and reliability testing under various environmental conditions.
Can SDPS be customized for specific applications?
Yes, SDPS can be customized to meet specific application requirements, y compris le matériau du substrat, taille, épaisseur, surface finish, and circuit layout. Showa Denko offers customization services to tailor SDPS to customer needs.
Where can I purchase SDPS?
SDPS are available through authorized distributors and directly from Showa Denko. Customers can contact Showa Denko for inquiries, quotes, and technical support related to SDPS products.