Fabricant de substrats à ondes millimétriques
Fabricant de substrats à ondes millimétriques,Millimeter Wave substrates are specialized materials designed to support high-frequency signal transmission in the millimeter-wave range, typically from 30 GHz to 300 GHz. These substrates are crafted from materials with low dielectric loss and high thermal conductivity to handle the demands of millimeter-wave applications, such as advanced communication systems, radar, and satellite technologies. Their precise construction minimizes signal degradation and interference, ensuring high signal integrity and performance. Millimeter Wave substrates facilitate the integration of complex, high-speed circuitry in compact and efficient designs, enabling cutting-edge technologies to operate effectively in demanding environments.
What is a Millimeter Wave Substrate?
A Millimeter Wave Substrate is a specialized material used in the design and fabrication of electronic circuits and systems operating at millimeter wave frequencies, typically defined as frequencies between 30 GHz and 300 GHz. These substrates are crucial in applications such as radar systems, satellite communications, and high-speed data transmission, where high-frequency signals require precise handling and minimal loss.
Millimeter wave frequencies demand substrates with unique electrical and mechanical properties to ensure optimal performance. Key characteristics of these substrates include low dielectric loss, stable dielectric constant, and minimal signal degradation. Materials commonly used for millimeter wave substrates include high-frequency laminates, céramique, and advanced composites.
In practice, the choice of substrate material affects the performance of the final circuit or system. For instance, a low-loss substrate helps in maintaining signal integrity and minimizing attenuation, which is critical for maintaining high data rates and signal clarity at millimeter wave frequencies. De plus, the substrate’s thermal and mechanical properties are also important, as they impact the reliability and durability of the components.
Advanced millimeter wave substrates are often engineered with precision to support high-frequency operations and are tailored to meet specific performance requirements in cutting-edge technologies. Their development and application are essential for the advancement of modern high-frequency communication systems and other high-tech electronic applications.
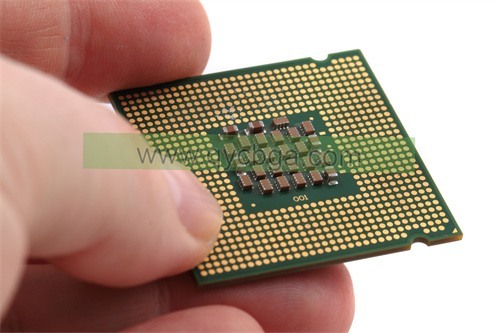
Fabricant de substrats à ondes millimétriques
What is the Millimeter Wave Substrate Design Guidelines?
Designing millimeter wave substrates requires careful attention to several key guidelines to ensure optimal performance and reliability. Here are some essential design guidelines:
- Sélection des matériaux: Choose substrates with low dielectric loss (low loss tangent) and stable dielectric constant (relative permittivity) to minimize signal attenuation and maintain signal integrity. Common materials include high-frequency laminates, céramique, and advanced composites designed specifically for millimeter wave applications.
- Impedance Matching:Ensure that the substrate supports accurate impedance matching to prevent reflections and signal loss. This involves precise control of the substrate’s thickness, dielectric constant, and trace width. Use simulation tools to verify impedance characteristics across the operating frequency range.
- Surface Roughness: Minimize surface roughness to reduce signal scattering and losses. The substrate surface should be smooth to ensure consistent electrical performance and high-frequency signal propagation.
- Gestion thermique: Consider the thermal properties of the substrate, as millimeter wave circuits can generate significant heat. Choose materials with good thermal conductivity and incorporate appropriate heat dissipation techniques to prevent overheating and maintain stable operation.
- Mechanical Stability: Ensure the substrate provides mechanical stability to support the high-frequency components and circuits. This includes checking for dimensional stability and resistance to warping or deformation during manufacturing and operation.
- Fabrication Tolerances: Adhere to tight fabrication tolerances to ensure precision in the manufacturing process. Small deviations in dimensions or material properties can significantly impact performance at millimeter wave frequencies.
- Design for Manufacturing: Incorporate design practices that facilitate ease of manufacturing and assembly. This includes considering factors such as substrate size, handling, and processing methods to avoid defects and ensure high-quality production.
- Intégrité du signal: Pay close attention to signal integrity by minimizing crosstalk, signal degradation, et interférences électromagnétiques. Implement proper grounding and shielding techniques to protect signal paths.
- Testing and Validation: Conduct thorough testing and validation of the substrate and the overall circuit design. This includes measurements of signal loss, impedance, and thermal performance to ensure the substrate meets the required specifications.
By following these guidelines, designers can optimize millimeter wave substrate performance, ensuring that high-frequency circuits and systems operate effectively and reliably in advanced communication and radar applications.
What is the Millimeter Wave Substrate Fabrication Process?
Le fabrication process for millimeter wave substrates involves several key steps tailored to produce high-precision and high-performance materials suitable for high-frequency applications. Here’s a detailed overview of the typical process:
- Sélection des matériaux:Choose an appropriate substrate material based on the required electrical, thermique, et les propriétés mécaniques. Common materials include high-frequency laminates, céramique, and advanced composites.
- Préparation du matériel: Process the selected material into sheets or panels of the desired thickness. This may involve cutting, polishing, and conditioning the substrate to meet specific design requirements.
- Photoresist Coating: Apply a photoresist layer to the substrate. This is a light-sensitive material used to create patterns on the substrate. The photoresist is typically applied using spin coating or roller coating techniques to achieve a uniform layer.
- Pattern Transfer: Expose the photoresist to ultraviolet (UV) light through a photomask that contains the desired circuit pattern. This step transfers the circuit design onto the photoresist layer. The areas of the photoresist exposed to UV light undergo a chemical change, making them either soluble or insoluble in the developer solution.
- Development: Develop the exposed photoresist to reveal the pattern. This involves immersing the substrate in a developer solution that removes the soluble photoresist, leaving behind the desired pattern on the substrate.
- Etching: Use etching techniques to remove material from the substrate where the photoresist was removed. This step creates the actual circuit pattern on the substrate. Etching can be done using wet etching (chemical solutions) or dry etching (plasma-based methods), depending on the substrate material and required precision.
- Photoresist Removal: Strip away the remaining photoresist to reveal the final circuit pattern on the substrate. This is usually done with a photoresist stripper or solvent.
- Via and Plating: If the design includes vias (holes that connect different layers of the substrate), drill or laser them and then plate them with metal to establish electrical connections. This may involve processes such as electroless plating or electroplating.
- Laminage: For multilayer substrates, laminate additional layers onto the base substrate. This involves applying adhesive and heat to bond multiple layers together, forming a multi-layered circuit board.
- Essais et inspections: Conduct thorough testing and inspection of the fabricated substrate. This includes checking for defects, measuring electrical properties, and verifying that the substrate meets design specifications.
- Final Processing:Perform any additional processes required to finalize the substrate, such as cutting to size, applying surface finishes, or adding solder masks and other protective layers.
- Packaging: Package the finished substrates for shipment and integration into electronic systems. This may involve protective packaging to prevent damage during transport and handling.
Each of these steps is critical in ensuring that the millimeter wave substrate performs effectively at high frequencies, meeting the stringent requirements of advanced communication systems, radar applications, and other high-tech electronic devices.
How do you Manufacture a Millimeter Wave Substrate?
Manufacturing a millimeter wave substrate involves several critical steps to ensure that the material meets the high-frequency performance requirements. Voici un aperçu du processus de fabrication:
- Sélection des matériaux: Begin by choosing a suitable substrate material with low dielectric loss, a stable dielectric constant, and appropriate thermal and mechanical properties. Materials often used include high-frequency laminates, céramique, and advanced composites specifically designed for millimeter wave applications.
- Préparation du matériel: Process the selected material to achieve the desired thickness and surface characteristics. For laminates, this involves stacking layers of prepreg and then curing them. For ceramics or composites, the material may be pressed and sintered to form the desired substrate shape and properties.
- Circuit Design and Layout: Develop the circuit design and layout using specialized software. This includes defining trace patterns, impedance levels, and component placements to ensure the substrate can handle millimeter wave frequencies effectively.
- Photolithography: Apply a photoresist layer to the substrate material and use photolithography techniques to create the circuit pattern. This involves exposing the photoresist to UV light through a mask, then developing the resist to reveal the underlying substrate.
- Etching: Remove the unwanted material from the substrate to form the circuit patterns. This is typically done using chemical etching processes that selectively dissolve the exposed material, leaving behind the desired circuitry.
- Metal Deposition: Deposit thin layers of metal, comme le cuivre, onto the substrate to form the conductive traces and pads. Techniques like sputtering, electroplating, or vacuum deposition are commonly used to achieve the required metal thickness and coverage.
- Drilling and Via Formation:Create holes and vias (electrical connections between different layers) in the substrate as required by the circuit design. This can be done using laser drilling or mechanical drilling methods, followed by plating to ensure electrical conductivity through the vias.
- Laminage (for multi-layer substrates): If the design involves multiple layers, stack and bond them together using a lamination process. Apply heat and pressure to fuse the layers and ensure proper alignment and adhesion.
- Finishing and Inspection: Perform finishing processes such as surface cleaning, coating, and solder mask application to protect and prepare the substrate for final assembly. Inspect the substrate for defects, dimensional accuracy, and adherence to design specifications.
- Testing: Conduct thorough testing of the substrate to verify its performance at millimeter wave frequencies. This includes measuring signal integrity, impedance, and dielectric properties to ensure the substrate meets the required specifications.
- Assembly: Integrate the substrate into the final electronic assembly or package, ensuring that it aligns with other components and functions correctly within the high-frequency system.
By following these steps, manufacturers can produce millimeter wave substrates that meet the demanding performance requirements of high-frequency applications, ensuring reliability and efficiency in advanced communication and radar systems.
How Much Should a Millimeter Wave Substrate Cost?
The cost of a millimeter wave substrate can vary widely depending on several factors:
- Material Type: The choice of substrate material—whether it’s a high-frequency laminate, céramique, or advanced composite—can significantly impact cost. High-quality, low-loss materials specifically designed for millimeter wave applications are typically more expensive.
- Frequency Range and Performance Specifications: Substrates designed for higher frequencies or with stricter performance requirements (e.g., low dielectric loss, tight tolerances) generally cost more due to the advanced materials and precision manufacturing needed.
- Taille et épaisseur: Larger or thicker substrates will generally cost more. The cost also scales with the complexity of the circuit design and the number of layers if it’s a multi-layer substrate.
- Volume et échelle de production: Costs can be reduced with higher production volumes due to economies of scale. Custom or low-volume orders often have higher per-unit costs.
- Complexité de la fabrication: The complexity of the manufacturing process, including steps like photolithography, gravure, and metal deposition, affects the cost. Advanced processes and additional quality control measures can increase costs.
- Supplier and Region: Prices can vary depending on the supplier and the region. Factors such as local manufacturing capabilities, labor costs, and supply chain considerations can influence the overall cost.
As a rough estimate, millimeter wave substrates can range from a few hundred to several thousand dollars per square meter, depending on these factors. For example, simple substrates for lower frequencies might be on the lower end of this range, while high-performance substrates for extreme millimeter wave frequencies or specialized applications could be significantly more expensive.
For precise cost estimates, it’s best to consult with manufacturers or suppliers, who can provide quotes based on the specific requirements of your project.
What is Millimeter Wave Substrate Base Material?
Millimeter wave substrate base material refers to the foundational material used in the construction of substrates for high-frequency applications, specifically those operating in the millimeter wave frequency range (30 GHz to 300 GHz). This base material is crucial because it influences the electrical, mécanique, and thermal performance of the substrate.
Here are some common types of base materials used for millimeter wave substrates:
- High-Frequency Laminates: These are composite materials made of a dielectric core (such as a resin-impregnated glass fabric) with properties tailored for high-frequency applications. They offer low dielectric loss and stable dielectric constant, which are essential for maintaining signal integrity at millimeter wave frequencies. Examples include materials like Rogers RT/duroid® or Taconic’s RF/microwave laminates.
- Ceramic Materials: Ceramics are often used for their excellent dielectric properties and thermal stability. Materials such as alumina (Al2O3), barium titanate (BaTiO3), and other high-permittivity ceramics are used in applications where low loss and high stability are critical. Ceramics can be engineered to meet specific performance needs and are often used in high-reliability applications.
- Advanced Composites: These materials are engineered to combine the benefits of various components, such as low-loss dielectric materials and high-strength fibers. They can offer customized properties to meet specific performance requirements for millimeter wave frequencies.
- Polyimide Films: Polyimide materials, like Kapton®, are used for their flexibility and high thermal stability. While typically not the primary material for rigid substrates, they are used in flexible or hybrid millimeter wave circuits and applications.
- High-Performance Epoxy Resins: Epoxy resins formulated for high-frequency applications can be used in conjunction with reinforcing materials to create substrates that perform well at millimeter wave frequencies. These resins are engineered to provide low dielectric loss and thermal stability.
Each type of base material has its own set of advantages and trade-offs. The choice of material depends on factors such as the required performance characteristics, Besoins en matière de gestion thermique, mechanical stability, and cost considerations. High-frequency laminates are popular due to their balance of performance and manufacturability, while ceramics are chosen for applications requiring high precision and stability.
Which Company Makes Millimeter Wave Substrates?
In the field of high-frequency electronics and millimeter wave communications, many companies specialize in the production of millimeter wave substrates, which support frequencies ranging from 30 GHz to 300 GHz. Here are some well-known manufacturers with extensive experience and technical expertise in millimeter wave substrates:
- Rogers Corporation: As a leader in high-frequency materials, Rogers offers a range of high-performance millimeter wave substrate materials, such as the RT/duroid® series. These materials are widely used in radar, satellite communications, and high-speed data transmission systems due to their excellent dielectric properties and low loss characteristics.
- Arlon Materials for Electronics: Arlon provides a variety of substrate materials suitable for millimeter wave frequencies, particularly high-frequency composites and ceramics. Their products are known for high stability and low loss.
- Taconic Advanced Dielectric: Taconic offers various substrates for high-frequency and millimeter wave applications, including the Taconic RF/microwave laminates series. Their products excel in high-frequency performance and manufacturing processes.
- Nihon Superior Co., Ltd.: This company provides high-performance ceramic substrates for various high-frequency applications. Nihon Superior has extensive experience in the design and production of millimeter wave substrates.
- Thintronics: Specializing in high-frequency millimeter wave substrates, Thintronics offers customized solutions to meet different application requirements.
Our company also manufactures millimeter wave substrates and has the following advantages:
- High Precision Manufacturing:We use advanced manufacturing technologies and equipment to ensure that millimeter wave substrates have high-precision electrical performance and stable dimensional tolerances.
- Low Loss Materials: We use specially designed high-frequency materials with low dielectric loss and stable dielectric constants to ensure signal integrity and transmission efficiency at millimeter wave frequencies.
- Custom Solutions: We provide customized millimeter wave substrate solutions based on specific customer requirements, meeting the needs of different frequency bands and performance criteria.
- Reliability and Durability: Our substrate materials offer excellent thermal stability and mechanical strength, ensuring reliability and long-term stability under high-frequency operation.
- Professional Support: We have a team of experienced engineers who provide comprehensive support from design to production, including performance optimization and problem-solving.
With our advanced manufacturing capabilities and professional technical support, we can offer high-quality millimeter wave substrate solutions to meet the needs of various high-frequency applications.
What Are the 7 Qualités d’un bon service client?
Good customer service is essential for building strong relationships with customers and ensuring their satisfaction. Here are seven key qualities of excellent customer service:
- Réactivité: Effective customer service is prompt and timely. Responding quickly to customer inquiries, complaints, or issues demonstrates that you value their time and are committed to addressing their needs. This includes providing timely updates and resolving issues efficiently.
- Empathie: Understanding and acknowledging the customer’s feelings and perspectives is crucial. Showing empathy involves listening actively, recognizing their concerns, and validating their emotions. This helps build rapport and trust between the customer and the service provider.
- Knowledgeability: A well-informed customer service representative can provide accurate and helpful information. This includes understanding the products or services offered, being familiar with company policies, and having the ability to troubleshoot problems effectively.
- Compétences en communication: Clear and effective communication is vital for good customer service. This means using simple, straightforward language, being polite and respectful, and ensuring that customers fully understand the information being provided. Good communication also involves active listening and addressing the customer’s questions or concerns comprehensively.
- Patience: Handling customers with patience is important, especially when dealing with complex issues or frustrated individuals. Being patient helps ensure that the customer feels heard and valued, and allows for a thorough and thoughtful resolution to their concerns.
- Reliability: Customers need to trust that the service provider will deliver on promises and commitments. Reliability involves following through on what has been promised, meeting deadlines, and consistently providing high-quality service. It also means being dependable in handling customer issues or requests.
- Personalization: Tailoring the service experience to the individual needs of each customer enhances satisfaction. This includes recognizing repeat customers, remembering their preferences, and offering customized solutions or recommendations. Personalization helps create a more positive and memorable experience for the customer.
Ces qualités contribuent à une expérience client positive, favoriser la fidélité et encourager la fidélisation des clients. By focusing on these aspects, companies can build strong relationships with their customers and enhance their overall service reputation.
Foire aux questions
What is a millimeter wave substrate?
A millimeter wave substrate is a specialized material used in electronic circuits and systems that operate at millimeter wave frequencies (30 GHz to 300 GHz). These substrates support high-frequency signal transmission with minimal loss and interference.
What materials are used for millimeter wave substrates?
Common materials include high-frequency laminates (e.g., Rogers RT/duroid®), céramique (e.g., alumina), and advanced composites. These materials are chosen for their low dielectric loss and stable dielectric constant.
What are the key properties of millimeter wave substrates?
Important properties include low dielectric loss (to minimize signal attenuation), stable dielectric constant, high thermal stability, and good mechanical strength.
How do millimeter wave substrates differ from other substrates?
Millimeter wave substrates are specifically designed to handle higher frequencies and provide lower signal loss compared to standard substrates. They often require more precise material properties and manufacturing processes.
What applications use millimeter wave substrates?
They are used in high-frequency applications such as radar systems, satellite communications, 5G networks, and advanced data transmission systems.
What factors affect the cost of millimeter wave substrates?
Cost factors include the choice of material, substrate size and thickness, production volume, manufacturing complexity, and specific performance requirements.
How are millimeter wave substrates manufactured?
The manufacturing process involves material preparation, circuit design, photolithography, gravure, metal deposition, and finishing. Each step ensures that the substrate meets high-frequency performance criteria.