Ceramics PCB Manufacturer
Ceramics PCB Manufacturer,Ceramics PCBs, crafted from robust ceramic substrates like aluminum oxide or aluminum nitride, are engineered for high-performance electronic applications. Renowned for superior thermal conductivity, impeccable electrical insulation, and durability, they excel in demanding environments where traditional PCBs falter. Their innate ability to manage heat efficiently ensures stability even under extreme conditions, making them ideal for aerospace, automotor, and medical industries. With precise manufacturing processes and attention to design intricacies, Ceramics PCBs epitomize reliability and innovation, empowering cutting-edge technologies to thrive in the modern world.
What is a Ceramics PCB?
A Ceramic PCB, or Ceramic Printed Circuit Board, refers to a type of printed circuit board (PCB) that utilizes ceramic materials for its base, instead of traditional materials such as fiberglass or plastics. Ceramics offer several superior properties compared to standard PCB materials, including high thermal conductivity, Excelente aislamiento eléctrico, and robust mechanical strength. These characteristics make ceramic PCBs highly suitable for high-frequency and high-power electronic applications.
The most common types of ceramics used in these PCBs are aluminum oxide (Al2O3) y nitruro de aluminio (Aln). Aln, in particular, offers higher thermal conductivity compared to Al2O3, making it more effective for heat dissipation. This is crucial in applications where heat management is critical, such as in LED technology, power converters, and high-frequency amplifiers.
Ceramic PCBs can be manufactured through various techniques including thick film and thin film technologies. In thick film technology, conductive, resistive, and insulating pastes are screen printed onto the ceramic base. Thin film technology, however, involves the deposition of thin layers of metal onto the ceramic substrate through processes like sputtering. This allows for finer resolution and more detailed circuit patterns, beneficial for high-density applications.
Their superior thermal management, reliability under high temperatures, and electrical performance make ceramic PCBs ideal for demanding applications across aerospace, automotor, and medical fields, where conventional PCBs might fail under stress.
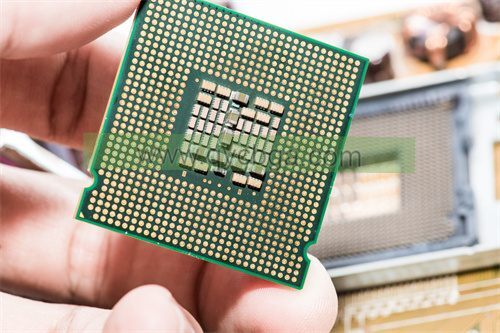
Ceramics PCB Manufacturer
What are the Ceramics PCB Design Guidelines?
Designing a ceramic PCB requires attention to several key guidelines to ensure optimal performance and reliability. Here are some common guidelines:
- Gestión térmica: Since ceramics offer excellent thermal conductivity, consider designing the layout to efficiently dissipate heat from high-power components. Proper heat sinking and thermal vias can help in heat dissipation.
- Dielectric Constant: Ceramics have a relatively high dielectric constant compared to traditional PCB materials. Design the circuit layout considering the dielectric properties to maintain signal integrity, especially in high-frequency applications.
- Colocación de componentes: Place components strategically to minimize signal distortion and ensure efficient heat dissipation. High-power components should be placed near heat-sinking areas, and sensitive components should be shielded from interference.
- Via Placement: Use thermal vias to improve heat dissipation from components to the ceramic substrate. Strategic placement of vias can enhance thermal conductivity and reduce thermal resistance.
- Selección de materiales: Choose the appropriate ceramic material based on the specific requirements of the application, considering factors such as thermal conductivity, Constante dieléctrica, y resistencia mecánica.
- Routing and Trace Width: Optimize trace widths and routing to minimize impedance mismatches, signal loss, e interferencias electromagnéticas (EMI). Follow recommended guidelines for trace width, espaciamiento, y control de impedancia.
- Tierra: Implement a solid ground plane to minimize ground loops and reduce EMI. Proper grounding techniques can also improve signal integrity and reduce noise.
- Solder Mask and Surface Finish: Choose solder mask materials compatible with ceramic substrates and select surface finishes suitable for the specific application requirements, considering factors such as solderability and corrosion resistance.
- Pruebas y validación: Conduct thorough testing and validation of the ceramic PCB design to ensure compliance with performance specifications and reliability under operating conditions.
By adhering to these guidelines, designers can create ceramic PCB layouts that optimize performance, fiabilidad, and manufacturability for a wide range of applications.
What is the Ceramics PCB Fabrication Process?
The fabrication process for ceramic PCBs involves several steps, each crucial for ensuring the final product meets performance and reliability requirements. Here’s an overview of the typical fabrication process:
- Preparación del sustrato: The process starts with preparing the ceramic substrate, which is usually made of materials like aluminum oxide (Al2O3) or aluminum nitride (Aln). The substrate is cut into the desired size and shape, and surface preparation techniques such as cleaning and roughening may be employed to promote adhesion of subsequent layers.
- Layer Deposition: Depending on the specific design requirements, various layers may be deposited onto the ceramic substrate. These layers typically include conductive, resistive, and insulating materials. Techniques like screen printing or thin-film deposition (p. ej.., sputtering) are commonly used for this purpose.
- Patrón de circuitos: The conductive and resistive materials are patterned to create the desired circuit layout using photolithography or screen printing techniques. Photolithography involves applying a photoresist layer, exposing it to UV light through a mask with the circuit pattern, and then developing it to remove the unwanted areas.
- Vía Formación: Vias are holes drilled or etched through the substrate to provide electrical connections between different layers. Laser drilling or chemical etching processes are typically used to create vias in ceramic substrates.
- Metalización: Después de la formación de la vía, metal is deposited onto the substrate to form conductive traces and vias. This can be done using techniques like sputtering or electroplating.
- Deposición de capa dieléctrica: Insulating layers are deposited over the conductive traces and vias to electrically isolate them and provide protection. This step may involve screen printing or thin-film deposition of dielectric materials.
- Surface Finish and Coating: Surface finish materials like solder mask are applied to protect the circuitry and provide solderable surfaces for component attachment. Adicionalmente, protective coatings may be applied to enhance durability and reliability.
- Curing and Annealing: The fabricated PCB undergoes curing and annealing processes to ensure proper adhesion of layers, as well as to relieve internal stresses and improve mechanical strength.
- Testing and Inspection: Una vez que se complete la fabricación, the ceramic PCB undergoes rigorous testing and inspection to verify electrical connectivity, adherence to specifications, and reliability under operating conditions.
- Montaje final: After passing quality control checks, the ceramic PCB may be assembled with electronic components using soldering or other attachment methods, Dependiendo de los requisitos de la aplicación.
By following these steps with precision and attention to detail, manufacturers can produce ceramic PCBs that meet the stringent performance and reliability standards demanded by various industries and applications.
How do you manufacture a Ceramics PCB?
Manufacturing a ceramic PCB involves several intricate steps to ensure the final product meets the desired specifications and performance requirements. Here’s a detailed overview of the typical manufacturing process:
- Preparación del diseño: The process starts with the design of the ceramic PCB using specialized PCB design software. Design engineers create the circuit layout, considering factors such as component placement, Enrutamiento de rastreo, y gestión térmica.
- Selección de materiales: Choose the appropriate ceramic material based on the specific requirements of the application. Common ceramic materials used for PCBs include aluminum oxide (Al2O3) y nitruro de aluminio (Aln), each offering unique properties such as thermal conductivity and dielectric constant.
- Preparación del sustrato: Prepare the ceramic substrate by cutting it to the desired size and shape. Surface preparation techniques such as cleaning and roughening may be employed to promote adhesion of subsequent layers.
- Layer Deposition: Deposit various layers onto the ceramic substrate to create the circuitry. This typically involves depositing conductive, resistive, and insulating materials using techniques like screen printing or thin-film deposition (p. ej.., sputtering).
- Patrón de circuitos: Pattern the conductive and resistive layers to create the desired circuit layout. This step may involve photolithography or screen printing techniques to define the circuit traces and components.
- Vía Formación: Create vias, which are holes drilled or etched through the substrate to provide electrical connections between different layers. Laser drilling or chemical etching processes are commonly used to create vias in ceramic substrates.
- Metalización: Deposit metal onto the substrate to form conductive traces and vias. This can be achieved through techniques like sputtering or electroplating, ensuring good adhesion and conductivity.
- Deposición de capa dieléctrica: Deposit insulating layers over the conductive traces and vias to electrically isolate them and provide protection. This step may involve screen printing or thin-film deposition of dielectric materials.
- Surface Finish and Coating: Apply surface finish materials such as solder mask to protect the circuitry and provide solderable surfaces for component attachment. Adicionalmente, protective coatings may be applied to enhance durability and reliability.
- Curing and Annealing: Cure the fabricated PCB to ensure proper adhesion of layers and relieve internal stresses. Annealing processes may also be employed to improve mechanical strength and stability.
- Pruebas e inspección: Perform thorough testing and inspection of the ceramic PCB to verify electrical connectivity, adherence to specifications, and reliability under operating conditions. Esto puede incluir pruebas eléctricas, Inspección visual, y pruebas de fiabilidad (p. ej.., Ciclo térmico, humidity testing).
- Montaje final: After passing quality control checks, the ceramic PCB may be assembled with electronic components using soldering or other attachment methods, Dependiendo de los requisitos de la aplicación.
By following these steps meticulously and employing advanced manufacturing techniques, manufacturers can produce high-quality ceramic PCBs that meet the stringent performance and reliability standards required for various industries and applications.
How much should a Ceramics PCB cost?
The cost of a ceramic PCB can vary significantly depending on various factors such as size, complejidad, material choice, cantidad, y los procesos de fabricación involucrados. Here are some key factors that influence the cost:
- Material Cost: Materiales cerámicos, such as aluminum oxide (Al2O3) or aluminum nitride (Aln), can be more expensive compared to traditional PCB materials like FR4. The cost will depend on the specific type and quality of the ceramic material chosen.
- Procesos de fabricación: The manufacturing processes involved in producing ceramic PCBs, such as layer deposition, Vía de formación, metalización, and curing, can contribute to the overall cost. Processes like laser drilling for vias or thin-film deposition for high-precision circuits may incur higher costs.
- Complexity of Design: The complexity of the PCB design, incluyendo el número de capas, density of components, and intricacy of the circuit layout, can affect manufacturing costs. More complex designs may require additional processing steps and specialized equipment, increasing the overall cost.
- Cantidad:Economies of scale apply to PCB manufacturing, meaning that higher quantities generally lead to lower unit costs. Ordering larger quantities of ceramic PCBs can often result in discounted pricing per unit.
- Additional Services: Additional services such as testing, inspection, Acabado superficial, and assembly can add to the overall cost. These services are often necessary to ensure quality and reliability but may increase the final price.
- Proveedor y ubicación: The choice of PCB supplier and their location can impact costs due to differences in labor costs, overhead expenses, and shipping fees.
As a rough estimate, the cost of a ceramic PCB can range from a few dollars to several hundred dollars per square inch, depending on the factors mentioned above. For a more accurate cost estimate, it’s best to consult with PCB manufacturers or suppliers who can provide quotes based on specific design requirements and quantities.
What is Ceramics PCB base material?
The base material for ceramic PCBs is typically a ceramic substrate, which provides the foundation for building the electronic circuitry. The most commonly used ceramic materials for PCB substrates are:
- Aluminum Oxide (Al2O3): Also known as alumina, aluminum oxide is a widely used ceramic material for PCB substrates. It offers excellent thermal conductivity, good mechanical strength, y propiedades de aislamiento eléctrico. Alumina substrates are suitable for various high-temperature and high-power applications.
- Aluminum Nitride (Aln): Aluminum nitride is another popular choice for ceramic PCB substrates, particularly in applications requiring superior thermal management. AlN has exceptionally high thermal conductivity, even higher than alumina, making it ideal for dissipating heat from electronic components.
These ceramic materials provide several advantages over traditional PCB substrates such as FR4 (fiberglass-reinforced epoxy). They offer better thermal performance, improved electrical insulation, and enhanced reliability, making them well-suited for demanding applications in industries such as aerospace, automotor, telecomunicaciones, and power electronics. Adicionalmente, ceramic substrates can be manufactured with tight tolerances and fine features, allowing for high-density circuit designs and advanced packaging solutions.
Which company makes Ceramics PCB?
Many companies specialize in the manufacturing of Ceramics PCB, including large PCB manufacturers and specialized ceramic PCB factories internationally. Por ejemplo, there are Japanese companies such as Murata, Kyocera, and NGK Insulators, which possess deep expertise and technical capabilities in ceramic materials and electronic manufacturing. Adicionalmente, companies like Rogers Corporation in the United States, TDK in China, and BOE Technology Group in Shenzhen have significant business operations in the Ceramics PCB field.
En nuestra empresa, we also have the capability to manufacture Ceramics PCBs. Equipped with advanced production equipment and a skilled technical team, we can provide high-quality ceramic PCB products. Our manufacturing process is meticulously designed, involving ceramic substrate processing, material deposition, circuit pattern definition, Vía de formación, metalización, and final assembly. We employ advanced technologies and stringent quality control measures to ensure that each Ceramics PCB manufactured meets our customers’ requirements and standards.
Moreover, we prioritize communication and collaboration with our customers, offering customized PCB design solutions tailored to their specific needs and providing professional technical support and after-sales service. We are committed to delivering the best solutions to our customers, meeting the demands of various application areas, incluida la industria aeroespacial, Electrónica automotriz, communication equipment, Dispositivos médicos, and more.
En resumen, although Ceramics PCB manufacturing involves advanced technology and specialized knowledge, our company has the capabilities and experience to provide customers with high-quality and reliable products and services.
¿Cuáles son los 7 Cualidades de un buen servicio al cliente?
Good customer service is characterized by several key qualities that help businesses build strong relationships with their customers and ensure satisfaction. Here are seven important qualities of good customer service:
- Respuesta: Un buen servicio al cliente implica atender con prontitud las consultas de los clientes, Preocupaciones, and requests. Responding to customers in a timely manner demonstrates attentiveness and a commitment to meeting their needs.
- Empatía: La empatía implica comprender y reconocer la perspectiva del cliente, Sentimientos, y preocupaciones. Customer service representatives who demonstrate empathy can build rapport with customers and provide personalized assistance that resonates with their individual situations.
- Clear Communication: La comunicación efectiva es esencial para brindar un buen servicio al cliente. Customer service representatives should communicate clearly and concisely, ensuring that customers understand the information provided and any actions taken to resolve their issues.
- Conocimiento: Customer service representatives should have a thorough understanding of the products or services offered by the business. They should be knowledgeable enough to answer customer questions, provide guidance, and offer solutions to problems.
- Profesionalismo: Good customer service requires professionalism in all interactions with customers. This includes maintaining a positive attitude, remaining calm and composed, and treating customers with respect and courtesy, incluso en situaciones difíciles.
- Habilidades de resolución de problemas: Customer service representatives should be equipped with strong problem-solving skills to effectively address customer issues and resolve conflicts. They should be proactive in identifying solutions and taking appropriate action to ensure customer satisfaction.
- Seguimiento: Following up with customers after resolving their issues or completing a transaction is an important aspect of good customer service. This demonstrates care and concern for the customer’s experience and provides an opportunity to gather feedback and address any lingering concerns.
Al encarnar estas cualidades, businesses can deliver exceptional customer service that fosters loyalty, enhances reputation, and drives long-term success.
Preguntas frecuentes
What is a Ceramics PCB?
A Ceramics PCB, or Ceramic Printed Circuit Board, is a type of PCB that utilizes ceramic materials such as aluminum oxide (Al2O3) or aluminum nitride (Aln) as the base substrate. Ceramics PCBs offer advantages such as high thermal conductivity, Excelente aislamiento eléctrico, y resistencia mecánica.
How are Ceramics PCBs manufactured?
The manufacturing process for Ceramics PCBs involves several steps, incluida la preparación del sustrato, layer deposition, Patrón de circuitos, Vía de formación, metalización, Acabado superficial, and testing. These steps may vary depending on the specific requirements of the PCB design and the chosen ceramic materials.
What factors affect the cost of Ceramics PCBs?
The cost of Ceramics PCBs can vary depending on factors such as material choice, Procesos de fabricación, complexity of design, cantidad, additional services (p. ej.., ensayo, ensamblaje), y proveedor. Generalmente, Ceramics PCBs tend to be more expensive than traditional PCBs due to the cost of ceramic materials and specialized manufacturing techniques.
Where can I find a reliable supplier for Ceramics PCBs?
Reliable suppliers for Ceramics PCBs can be found through online searches, industry directories, trade shows, and referrals from other professionals in the electronics industry. It’s essential to research potential suppliers, evaluate their capabilities, Estándares de calidad, and customer reviews before making a decision.
What are the design considerations for Ceramics PCBs?
Designing Ceramics PCBs requires attention to factors such as thermal management, Propiedades dieléctricas, Colocación de componentes, routing, via design, Tierra, and material selection. These considerations ensure optimal performance, fiabilidad, and manufacturability of the final PCB design.