Cavity Step PCB Manufacturer
Cavity Step PCB Manufacturer,Cavity Step PCBs revolutionize electronic design by embedding components directly within the circuit board, offering compactness and efficiency unparalleled in traditional PCB layouts. These boards feature recessed areas, or cavities, meticulously crafted to house various components, ranging from integrated circuits to sensors. By integrating components within the PCB, Cavity Step technology optimizes space utilization, reduces signal path lengths, and minimizes electromagnetic interference. This innovative approach enhances the overall performance and reliability of electronic devices, making them ideal for applications where size constraints are critical, such as portable electronics, wearables, and aerospace systems. With their advanced design and manufacturing techniques, Cavity Step PCBs represent the pinnacle of modern electronic engineering, pushing the boundaries of what’s possible in miniaturization and functionality.
What is a Cavity Step PCB?
A Cavity Step PCB, also known as an Embedded Step PCB, is a type of printed circuit board (PCB) design that incorporates cavities or recessed areas within the board itself. These cavities are created by removing material from one or both sides of the PCB, resulting in a step-like structure.
The primary purpose of using a Cavity Step PCB is to integrate components or devices into the PCB itself, providing a more compact and streamlined design. By embedding components within the board, the overall footprint of the electronic device can be reduced, making it more space-efficient. Adicionalmente, embedding components can also enhance the performance and reliability of the device by reducing the length of signal traces and minimizing electromagnetic interference (EMI).
Cavity Step PCBs are commonly used in applications where size constraints are critical, such as in portable electronics, wearable devices, and aerospace systems. They are also used in high-frequency and high-speed applications where signal integrity is paramount.
The process of manufacturing Cavity Step PCBs involves several steps. First, the PCB substrate is typically made from materials such as FR-4, Un tipo de laminado epoxi reforzado con fibra de vidrio, or more specialized materials like Rogers or Teflon-based substrates, Dependiendo de los requisitos específicos de la aplicación. Próximo, the cavities are created using techniques such as routing, perforación, or milling. These cavities can be filled with components such as integrated circuits (Ics), sensors, or passive devices like resistors and capacitors. Finally, the PCB is assembled with the remaining components and undergoes testing to ensure functionality and reliability.
En general, Cavity Step PCBs offer a versatile solution for designing compact and high-performance electronic devices, allowing engineers to maximize space utilization while maintaining optimal functionality and reliability.
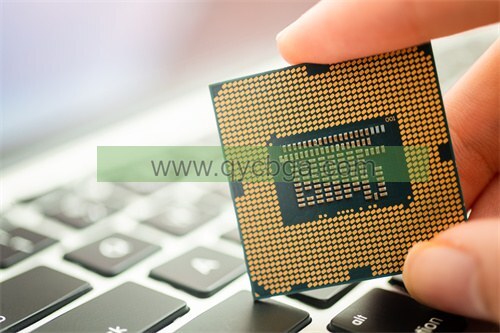
Cavity Step PCB Manufacturer
What are the Cavity Step PCB Design Guidelines?
Designing a Cavity Step PCB requires careful consideration of various factors to ensure optimal performance, fiabilidad, y fabricabilidad. Here are some guidelines to follow:
- Clearance and Creepage: Maintain adequate clearance and creepage distances between conductive elements within the cavities to prevent electrical breakdown and ensure safety compliance.
- Selección de materiales:Choose PCB substrate materials suitable for cavity fabrication and compatible with the intended application’s requirements, such as high-frequency operation or environmental conditions.
- Cavity Dimensions: Design cavities with appropriate dimensions to accommodate the embedded components while ensuring structural integrity and avoiding mechanical stress concentrations.
- Edge Plating: Apply edge plating or other reinforcement techniques to strengthen the edges of the cavities and prevent delamination or damage during PCB assembly and handling.
- Gestión térmica: Consider thermal management strategies to dissipate heat generated by embedded components effectively, such as incorporating thermal vias or metal core layers.
- Integridad de la señal: Optimize signal routing within the PCB, minimizing signal path lengths and avoiding impedance mismatches to maintain signal integrity, especially in high-speed applications.
- EMI Shielding: Implement shielding techniques, such as grounded planes or shielding layers, to mitigate electromagnetic interference (EMI) caused by embedded components and nearby signals.
- Component Accessibility: Ensure accessibility to embedded components for assembly, ensayo, and potential rework, considering factors like component height, tool access, and solder joint accessibility.
- Capacidad de fabricación: Diseñe la placa de circuito impreso teniendo en cuenta la capacidad de fabricación, considering fabrication processes such as routing, perforación, y montaje, and ensuring compatibility with standard PCB manufacturing equipment and techniques.
- Pruebas e inspección: Plan for testing and inspection methods to verify the integrity and functionality of embedded components and ensure quality control throughout the manufacturing process.
Siguiendo estas pautas, engineers can design Cavity Step PCBs that meet performance requirements, manufacturing constraints, and reliability standards for a wide range of applications.
What is the Cavity Step PCB Fabrication Process?
The fabrication process for Cavity Step PCBs involves several steps, incluida la preparación del sustrato, cavity creation, Colocación de componentes, y montaje. Here’s an overview of the typical fabrication process:
- Substrate Selection: Choose a suitable PCB substrate material based on the application requirements, such as FR-4 for general-purpose applications or specialized materials for high-frequency or high-temperature environments.
- Panelization: Arrange multiple PCB designs on a panel to maximize material usage and facilitate the manufacturing process. Panelization involves adding tooling holes, fiducial markers, and routing paths between individual PCBs.
- Circuit Imaging: Apply a layer of photoresist to the substrate and use a photomask to transfer the PCB design onto the photoresist layer. Expose the photoresist to ultraviolet (UV) light, develop it to remove unexposed areas, and etch away the exposed copper to create the circuit traces.
- Cavity Creation: Use precision milling, perforación, or routing techniques to create cavities or recessed areas within the PCB substrate. These cavities can be sized and shaped to accommodate embedded components such as integrated circuits (Ics), sensors, or passive devices.
- Plating and Surface Finish: Plate the exposed copper surfaces with a thin layer of conductive material to protect against oxidation and facilitate soldering. Aplicar un acabado superficial, such as HASL (Nivelación de soldadura de aire caliente), ENIG (Oro de inmersión de níquel químico), o OSP (Soldabilidad orgánica Conservantes), to improve solderability and prevent corrosion.
- Colocación de componentes: Use automated pick-and-place machines to accurately position surface-mount components (SMDs) onto the PCB substrate, including any components to be embedded within the cavities. Ensure proper alignment and orientation of components according to the PCB design.
- Soldering: Securely attach the components to the PCB substrate using soldering techniques such as reflow soldering or wave soldering. Ensure proper solder joint formation and inspect for defects such as solder bridges or insufficient solder coverage.
- Pruebas e inspección: Conduct electrical testing, such as continuity checks and functional testing, to verify the integrity and functionality of the assembled PCBs. Inspect the PCBs visually and using automated inspection equipment to detect any defects or manufacturing issues.
- Acabado final: Trim excess material from the panel and perform final finishing operations, such as depanelization and edge profiling, to separate individual PCBs and prepare them for packaging and shipment.
Durante todo el proceso de fabricación, quality control measures should be implemented to ensure consistency, fiabilidad, and compliance with specifications and standards. Collaboration between design engineers, fabricators, and assemblers is crucial to successfully manufacture Cavity Step PCBs that meet performance requirements and customer expectations.
How do you manufacture a Cavity Step PCB?
Manufacturing a Cavity Step PCB involves several steps, from designing the board to assembling components. Here’s a detailed overview of the process:
- Diseño: The process begins with PCB design using specialized software. Designers create the layout, including the placement of components and the configuration of cavities. They consider factors like component dimensions, clearance, and signal integrity.
- Selección de materiales: Choose a suitable substrate material based on the application’s requirements. Common materials include FR-4 epoxy fiberglass, high-frequency laminates like Rogers or Teflon-based substrates, or metal core laminates for enhanced thermal conductivity.
- Preparation: Prepare the substrate by cleaning and surface treatment to ensure proper adhesion of the copper layers and other materials applied during the manufacturing process.
- Cavity Creation: Use precision milling, perforación, or routing techniques to create the cavities or recessed areas within the PCB substrate. This step requires precise control to achieve the desired cavity dimensions and ensure structural integrity.
- Copper Deposition: Apply a thin layer of copper onto the substrate surface, typically through a process like electroplating or electroless plating. This copper layer forms the conductive traces and pads on the PCB.
- Patrón de circuitos: Use photolithography to transfer the PCB design onto the copper layer. This involves applying a photoresist material, exposing it to UV light through a photomask, developing the resist to remove unwanted areas, and etching away the exposed copper to create the circuit traces.
- Acabado superficial: Apply a surface finish to the exposed copper traces to improve solderability and protect against oxidation. Los acabados superficiales comunes incluyen HASL (Nivelación de soldadura de aire caliente), ENIG (Oro de inmersión de níquel químico), y OSP (Soldabilidad orgánica Conservantes).
- Ensamblaje de componentes: Place surface-mount components (SMDs) onto the PCB substrate using automated pick-and-place machines. Ensure proper alignment and orientation of components, including those to be embedded within the cavities.
- Soldering: Securely attach the components to the PCB substrate using soldering techniques such as reflow soldering or wave soldering. This step forms reliable electrical connections between the components and the circuit traces.
- Pruebas e inspección: Conduct electrical testing and visual inspection to verify the functionality and quality of the assembled PCBs. This includes continuity checks, functional testing, and inspection for defects such as solder bridges or insufficient solder coverage.
- Acabado final:Trim excess material from the panel, perform final finishing operations like depanelization and edge profiling, and prepare the PCBs for packaging and shipment.
Durante todo el proceso de fabricación, quality control measures are essential to ensure consistency, fiabilidad, and compliance with specifications and standards. Collaboration between design engineers, fabricators, and assemblers is crucial to successfully manufacture Cavity Step PCBs that meet performance requirements and customer expectations.
How much should a Cavity Step PCB cost?
The cost of a Cavity Step PCB can vary significantly depending on several factors, including the complexity of the design, the size of the board, the number of layers, the type of substrate material used, and the quantity ordered. Here are some factors that can influence the cost:
- Complexity of Design: The more intricate the design, with features such as multiple layers, fine pitch components, or densely packed cavities, the higher the manufacturing cost.
- Costos de material: Different substrate materials have varying costs. High-frequency laminates or specialized materials may be more expensive than standard FR-4.
- Number of Layers: Cavity Step PCBs can be single-sided, double-sided, or multi-layered. Each additional layer increases manufacturing complexity and cost.
- Cavity Machining: Creating cavities within the PCB substrate requires specialized machining techniques, which can add to the manufacturing cost.
- Surface Finish and Coating:The choice of surface finish, such as ENIG or OSP, can impact the cost. Additional coatings or finishes may also be required for specific applications, adding to the overall cost.
- Component Costs: The cost of components, including any embedded components within the cavities, contributes to the total cost of the PCB assembly.
- Quantity Ordered: Típicamente, larger quantities result in lower per-unit costs due to economies of scale. Sin embargo, prototyping or small batch orders may have higher per-unit costs.
- Assembly and Testing: Additional costs may be associated with component assembly, ensayo, and quality control processes.
To get an accurate cost estimate for a Cavity Step PCB, it’s essential to provide detailed specifications and requirements to PCB manufacturers or assembly houses. They can then provide a quote based on the specific parameters of the project. Adicionalmente, using online PCB prototyping services or getting quotes from multiple suppliers can help compare costs and find the most competitive pricing.
What is Cavity Step PCB base material?
The base material used for Cavity Step PCBs can vary depending on the specific requirements of the application. Sin embargo, some common base materials include:
- FR-4: FR-4 is a widely used substrate material for PCBs due to its cost-effectiveness, good electrical insulation properties, y resistencia mecánica. It consists of layers of woven fiberglass cloth impregnated with epoxy resin.
- High-Frequency Laminates: For applications requiring high-frequency operation, specialized laminates such as Rogers or Teflon-based materials may be used. These materials offer low dielectric loss, excellent electrical performance at high frequencies, and good thermal stability.
- Metal Core Laminates:In applications where thermal management is critical, metal core laminates may be used as the base material. These laminates typically consist of a layer of thermally conductive metal, como el aluminio o el cobre, intercalado entre capas de material aislante.
- Sustratos cerámicos:Sustratos cerámicos, such as alumina (Al2O3) or aluminum nitride (Aln), are used in high-power and high-temperature applications where excellent thermal conductivity and mechanical stability are required.
- Flexible Substrates: Flexible substrates, such as polyimide (PI) or polyester (PET), are used in applications requiring bendable or conformal PCBs, such as wearable electronics or flexible displays.
The choice of base material depends on various factors, including the operating environment, thermal requirements, Rendimiento eléctrico, and cost considerations. Designers select the most suitable material based on these factors to ensure the desired performance and reliability of the Cavity Step PCB.
Which company makes Cavity Step PCB?
Actualmente, there are many companies in the market that manufacture Cavity Step PCBs, some of which include Mouser Electronics from the United States, Würth Elektronik from Germany, and Shenzhen Aoshuo Innovative Electronics Co., Ltd. from China. These companies possess advanced manufacturing equipment and technology to meet various customer needs, ranging from common FR-4 materials to high-frequency Rogers materials, and even metal substrates. Their manufacturing processes and quality control procedures have undergone strict certification and testing to ensure that the produced Cavity Step PCBs meet various industry standards and specifications.
Like other professional PCB manufacturers, our company also has the capability to produce Cavity Step PCBs. We have advanced production equipment and an experienced team of engineers capable of customizing various types of PCBs, including Cavity Step PCBs, according to customer requirements. We employ advanced manufacturing processes and stringent quality control procedures to ensure that each PCB has excellent performance and reliability.
Our company can provide the following services and advantages:
- Diseño personalizado: Our engineering team can provide customized Cavity Step PCB design services tailored to the specific requirements of our customers, including circuit layout, Selección de materiales, and dimensional specifications.
- Advanced Manufacturing Equipment:We possess advanced manufacturing equipment, including high-precision CNC machines and automated production lines, enabling high-quality PCB production and processing.
- Estricto control de calidad: We implement a rigorous quality control system, from raw material procurement to production processing and final product testing, ensuring that the produced Cavity Step PCBs meet our customers’ requirements and standards.
- Timely Delivery Service: We prioritize customer satisfaction and strive to provide timely and efficient services. We can arrange production schedules according to customer needs and ensure on-time delivery of orders.
En resumen, our company has extensive experience and a professional team capable of meeting various customer requirements for Cavity Step PCBs. We are committed to providing high-quality, reliable PCB products and services to our customers, working hand in hand to create a bright future together.
¿Cuáles son los 7 Cualidades de un buen servicio al cliente?
Good customer service is essential for building and maintaining strong relationships with customers. Seven qualities of good customer service include:
- Respuesta: Being prompt in addressing customer inquiries, Preocupaciones, and requests. Responding quickly shows that you value the customer’s time and are committed to providing assistance when needed.
- Empatía: Showing understanding and compassion towards customers’ Sentimientos, necesidades, y situaciones. Empathy helps create a positive interaction and builds rapport with customers, incluso en situaciones difíciles.
- Claridad:Communicating clearly and effectively to ensure that customers understand the information provided. Using simple language, avoiding jargon, and providing concise explanations help prevent misunderstandings and confusion.
- Profesionalismo:Maintaining professionalism in all interactions with customers, including being courteous, respetuoso, y mantener una actitud positiva. Professionalism instills confidence in customers and reflects well on the company’s reputation.
- Problem-solving skills: Being able to identify and resolve customer issues efficiently and effectively. Having strong problem-solving skills allows representatives to address customer concerns promptly and find satisfactory solutions.
- Adaptabilidad: Being flexible and adaptable to meet the diverse needs and preferences of different customers. Adaptability involves adjusting communication styles, problem-solving approaches, and service delivery methods based on individual customer requirements.
- Consistencia: Providing consistent service experiences across all customer touchpoints and interactions. Consistency builds trust and reliability, ensuring that customers know what to expect when interacting with the company.
Al encarnar estas cualidades, Las empresas pueden ofrecer un servicio al cliente excepcional que supere las expectativas, fosters customer loyalty, and contributes to long-term success.
Preguntas frecuentes
What is a Cavity Step PCB?
A Cavity Step PCB, also known as an Embedded Step PCB, is a type of printed circuit board that incorporates recessed areas or cavities within the board itself. These cavities are created to embed components, reducing the overall footprint of the electronic device.
What are the advantages of using Cavity Step PCBs?
Cavity Step PCBs offer several advantages, including space-saving design, improved thermal management, Integridad de la señal mejorada, and reduced electromagnetic interference (EMI). They are ideal for applications with size constraints, high-frequency operation, or stringent performance requirements.
What types of components can be embedded in Cavity Step PCBs?
Various components can be embedded in Cavity Step PCBs, incluidos los circuitos integrados (Ics), sensors, passive devices like resistors and capacitors, and even small modules or connectors. Embedding components within the board reduces the need for external components and simplifies assembly.
How are cavities created in Cavity Step PCBs?
Cavities in Cavity Step PCBs are typically created using precision milling, perforación, or routing techniques. These techniques remove material from one or both sides of the PCB substrate to create recessed areas where components can be embedded.
What materials are commonly used for Cavity Step PCBs?
Common substrate materials for Cavity Step PCBs include FR-4 epoxy fiberglass, high-frequency laminates like Rogers or Teflon-based materials, metal core laminates for thermal management, and ceramic substrates for high-power applications.
What are the design considerations for Cavity Step PCBs?
Design considerations for Cavity Step PCBs include cavity dimensions, clearance and creepage requirements, Gestión térmica, Integridad de la señal, component accessibility, y fabricabilidad.
Can any PCB manufacturer produce Cavity Step PCBs?
While many PCB manufacturers have the capability to produce Cavity Step PCBs, it’s essential to choose a manufacturer with experience and expertise in this specialized type of PCB design and fabrication. Working with a reputable manufacturer ensures quality and reliability.