Buried Cavity Package Substrate Manufacturer
Buried Cavity Package Substrate Manufacturer,Buried Cavity Package Substrates are specialized components used in semiconductor packaging, featuring integrated cavities within the substrate structure. These cavities are embedded beneath the surface layers, providing space for housing sensitive components or enhancing thermal management. Buried Cavity Package Substrates offer advantages such as reduced package size, improved electrical performance, and enhanced heat dissipation compared to traditional substrates. They are crucial in applications requiring compact and efficient designs, such as high-density integrated circuits, RF/microwave modules, and power electronics. Their innovative design supports advanced packaging techniques and facilitates the integration of multiple functions within a single substrate, meeting the evolving demands of modern electronic devices.
What is a Buried Cavity Package Substrate?
A Buried Cavity Package Substrate refers to a specialized type of substrate used in semiconductor packaging. It involves creating cavities within the substrate material itself, which are then buried under layers of material. These cavities are strategically placed to accommodate various components such as chips, passive components, or even other substrates.
The primary purpose of a Buried Cavity Package Substrate is to enable dense integration of components while managing heat dissipation and electrical performance. By embedding components within the substrate, the overall size of the package can be reduced, which is crucial for applications where space is limited, such as in mobile devices or high-performance computing.
Manufacturing Buried Cavity Package Substrates involves precise etching and filling processes to create the cavities and ensure they are properly insulated and protected. The design also considers thermal management and electrical routing to maintain performance and reliability. This substrate type is often chosen for its ability to enhance the functionality and miniaturization of electronic devices.
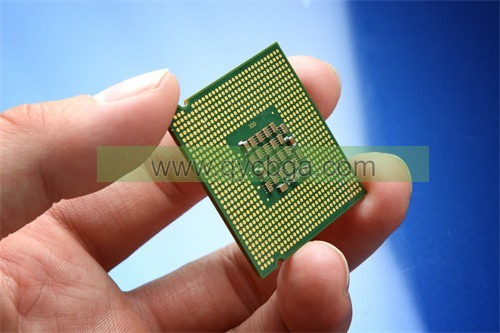
Buried Cavity Package Substrate Manufacturer
What are the Buried Cavity Package Substrate Design Guidelines?
Design guidelines for Buried Cavity Package Substrates typically include several key considerations to ensure optimal performance and manufacturability:
- Cavity Design and Placement: Determine the size, shape, and placement of cavities based on the components to be embedded. Ensure adequate clearance and spacing for neighboring components and signal routing.
- Selección del material del sustrato: Choose substrate materials with suitable thermal conductivity, Propiedades dieléctricas, and mechanical strength to support the embedded components and maintain reliability under operational conditions.
- Apilamiento de capas: Define the layer stackup considering the number of signal, power, and ground planes required. Ensure proper isolation and impedance control for signal integrity.
- Cavity Etching and Filling: Specify the etching technique for creating cavities within the substrate material. Ensure precise control to achieve the desired depth and dimensions. Select appropriate filling materials (p. ej.., epoxy resin) to encapsulate the cavities and provide structural integrity.
- Gestión térmica:Incorporate thermal vias and thermal pads to enhance heat dissipation from embedded components to the substrate and external heatsinks. Optimize the placement of thermal vias to minimize thermal resistance.
- Electrical Routing: Plan the routing of electrical traces to connect embedded components to the rest of the substrate. Maintain signal integrity by avoiding sharp bends, minimizing crosstalk, and ensuring controlled impedance.
- Mechanical Considerations: Design the substrate to withstand mechanical stresses during handling and operation. Tenga en cuenta factores como el coeficiente de expansión térmica (CTE) matching with components and assembly materials to prevent solder joint failures.
- Assembly and Testing: Define assembly processes compatible with the substrate design, such as component placement and soldering techniques. Implement testing procedures to verify electrical continuity, thermal performance, and overall reliability.
- Diseño para la fabricación (DFM): Optimize the design for ease of manufacturing, including considerations for material availability, cost-effectiveness, and compatibility with fabrication processes (p. ej.., aguafuerte, lamination, filling).
- Reliability and Quality Assurance: Implement measures to ensure long-term reliability, such as adherence to industry standards (p. ej.., IPC standards), reliability testing (p. ej.., Ciclo térmico, solderability), and quality control throughout the manufacturing process.
By adhering to these design guidelines, engineers can develop Buried Cavity Package Substrates that meet performance requirements while facilitating efficient manufacturing and ensuring reliability in electronic applications.
What is the Buried Cavity Package Substrate Fabrication Process?
The fabrication process for Buried Cavity Package Substrates involves several key steps to ensure precise construction and integration of embedded components. Here’s an overview of the typical process:
- Selección de materiales: Choose suitable substrate materials, often FR-4 or other high-performance laminates, based on thermal, eléctrico, and mechanical requirements.
- Layer Preparation: Start with the base substrate material, which is laminated into multiple layers according to the design specifications. The layers may include signal, power, and ground planes.
- Cavity Definition: Use photolithography to define the cavity pattern on the substrate. A photosensitive material is applied, exposed to light, and developed to create a mask for etching.
- Aguafuerte: Employ chemical or laser etching to create cavities in the defined areas. This step requires precision to achieve the desired depth and dimensions for the cavities.
- Cavity Cleaning: Clean the etched cavities to remove any residues and prepare the surfaces for filling. This step is crucial for ensuring adhesion and performance.
- Cavity Filling: Fill the cavities with a suitable material, such as epoxy or other resins. This material supports the embedded components and provides mechanical stability.
- Curing: Cure the filling material to solidify it, typically involving heat or UV light, depending on the resin used. This step ensures the embedded components are securely held in place.
- Electrical Routing: Implement the necessary electrical routing by drilling vias and etching traces on the surface layers. This allows for connections between embedded components and external circuitry.
- Lamination and Bonding: Laminate additional layers if needed, ensuring proper adhesion and alignment. This step may involve heat and pressure to fuse layers together.
- Procesamiento final: Complete any additional processes such as surface finishing, applying solder mask, or screen printing for component identification and protection.
- Testing and Quality Assurance: Conduct thorough testing to verify electrical performance, Gestión térmica, and overall integrity of the substrate. This may include continuity testing, Ciclo térmico, and visual inspections.
Siguiendo estos pasos:, manufacturers can produce high-quality Buried Cavity Package Substrates that meet the demanding requirements of modern electronic applications.
How do you manufacture a Buried Cavity Package Substrate?
Manufacturing a Buried Cavity Package Substrate involves several detailed steps to ensure precision and functionality. Here’s an overview of the process:
- Selección de materiales: Choose a suitable substrate material, typically a high-performance laminate like FR-4 or other advanced materials, based on thermal and electrical properties.
- Layer Preparation: Prepare the base substrate by laminating multiple layers, including signal, ground, and power planes as required by the design.
- Cavity Design: Utilize CAD software to create a design that specifies the size, shape, and placement of cavities. This design is crucial for the subsequent etching process.
- Photolithography: Apply a photosensitive coating (photoresist) on the substrate. Expose it to UV light through a mask that defines the cavity pattern, then develop the photoresist to reveal the areas for etching.
- Aguafuerte: Use chemical etching or laser etching to create cavities in the exposed areas. This process must be carefully controlled to achieve the desired depth and profile.
- Cleaning: Thoroughly clean the cavities to remove any residues, ensuring a clean surface for the next steps.
- Cavity Filling: Fill the cavities with a suitable material, such as epoxy or resin, that provides mechanical support for embedded components. This filling can be done using dispensing techniques.
- Curing: Cure the filling material using heat or UV light to ensure it hardens and securely holds the embedded components in place.
- Electrical Routing: Drill vias and etch traces on the substrate surface to create necessary electrical connections. This involves using techniques like laser drilling and chemical etching.
- Lamination of Additional Layers: If the design requires, laminate additional layers onto the substrate, ensuring proper alignment and bonding through heat and pressure.
- Acabado superficial: Apply surface finishes such as solder mask or surface treatments to protect the substrate and prepare it for component assembly.
- Testing and Quality Assurance: Conduct comprehensive testing to assess electrical performance, thermal characteristics, and structural integrity. This includes continuity tests, Ciclo térmico, and visual inspections.
Siguiendo estos pasos:, manufacturers can produce high-quality Buried Cavity Package Substrates that meet the needs of advanced electronic applications.
How much should a Buried Cavity Package Substrate cost?
The cost of a Buried Cavity Package Substrate can vary widely based on several factors, Incluido:
- Material: The choice of substrate material (p. ej.., FR-4, Laminados de alta frecuencia) affects pricing. Advanced materials may increase costs.
- Complexity:The complexity of the design, including the number and size of cavities, Recuento de capas, and routing requirements, can impact manufacturing costs.
- Volume: Production volume plays a significant role; larger quantities often reduce per-unit costs due to economies of scale.
- Manufacturing Techniques: The specific processes used (p. ej.., aguafuerte, filling, curing) can influence costs. More advanced manufacturing methods may be pricier.
- Testing and Quality Control: Additional costs may arise from testing and quality assurance measures to ensure reliability.
- Supplier: Prices may vary between suppliers based on their capabilities, location, and reputation.
As a rough estimate, the cost can range from a few dollars to over $50 per unit, depending on these factors. For precise pricing, it’s best to consult with manufacturers or suppliers directly, providing them with specific design requirements and volume needs.
What is Buried Cavity Package Substrate base material?
The base material for Buried Cavity Package Substrates typically includes:
- FR-4: A widely used glass-reinforced epoxy laminate, known for its good electrical properties, Resistencia mecánica, y eficacia en función de los costos.
- High-Frequency Laminates: Materials such as PTFE (Teflon) or other advanced composites are used for applications requiring low loss and high-frequency performance.
- Polyimide: Used for applications needing excellent thermal stability and flexibility, often in high-temperature environments.
- Ceramic Materials: Some substrates may utilize ceramics for their excellent thermal conductivity and electrical insulation properties, suitable for high-performance applications.
The choice of base material depends on the specific application requirements, including thermal management, Rendimiento eléctrico, and mechanical integrity.
Which company makes Buried Cavity Package Substrates?
Many companies manufacture Buried Cavity Package Substrates, primarily including electronic manufacturing companies and semiconductor packaging service providers worldwide. These companies typically possess advanced manufacturing technologies and specialized engineering teams to meet diverse customer needs and technical standards.
Buried Cavity Package Substrates are an advanced semiconductor packaging technology that enables higher integration and superior thermal management in electronic devices. These substrates are commonly used in applications requiring high performance and compact size, such as mobile devices, high-performance computing, and communication equipment.
The manufacturing of Buried Cavity Package Substrates involves critical technologies and processes, including precise photolithography, Grabado químico, selection of filling materials, and curing. Each step requires strict process control and quality assurance to ensure the substrate’s reliability and performance.
Our company is also a manufacturer capable of producing Buried Cavity Package Substrates. We have advanced production equipment and a technical team that can manufacture high-quality Buried Cavity Package Substrates according to customer design requirements and specifications. Our manufacturing process adheres strictly to industry standards, ensuring that every aspect of the product meets the highest quality and performance criteria.
As a manufacturer, we not only focus on technological innovation and production capabilities but also prioritize collaboration with customers to understand their specific needs and provide customized solutions. We offer competitive pricing and excellent customer service, ensuring that clients are satisfied with product quality and delivery times.
If you have further questions about Buried Cavity Package Substrates or are interested in our products, please feel free to contact us. We are dedicated to providing you with support and service.
¿Cuáles son los 7 Cualidades de un buen servicio al cliente?
Good customer service typically embodies the following seven qualities:
- Respuesta: Timely responses to customer inquiries and concerns demonstrate that a company values its customers’ time and needs.
- Empatía: Understanding and acknowledging customers’ feelings and perspectives helps build rapport and trust.
- Knowledge: Staff should be well-informed about products, services, and policies to provide accurate information and assistance.
- Habilidades de comunicación: Claro, conciso, and polite communication helps ensure that customers feel heard and understood.
- Problem-Solving Ability: Being proactive in addressing issues and finding solutions enhances customer satisfaction and loyalty.
- Profesionalismo: Maintaining a respectful and courteous demeanor at all times reflects positively on the company.
- Seguimiento: Checking in with customers after their issues have been resolved shows commitment to their satisfaction and fosters long-term relationships.
Preguntas frecuentes
What are the advantages of using Buried Cavity Package Substrates?
Advantages include improved thermal management, enhanced electrical performance, reduced package size, and increased component integration.
What materials are used for Buried Cavity Package Substrates?
Common materials include FR-4, Laminados de alta frecuencia (such as PTFE), Polyimide, and ceramics, depending on the specific application requirements.
What industries use Buried Cavity Package Substrates?
These substrates are widely used in the electronics industry, particularly in applications like mobile devices, high-performance computing, Electrónica automotriz, and communication systems.
How are Buried Cavity Package Substrates manufactured?
The manufacturing process involves material selection, fotolitografía, aguafuerte, cavity filling, curing, electrical routing, and quality testing.
What are the key design considerations for Buried Cavity Package Substrates?
Key considerations include cavity size and placement, Gestión térmica, electrical routing, Apilamiento de capas, y fabricabilidad.
Can Buried Cavity Package Substrates be customized?
Sí, they can be tailored to meet specific customer requirements, including design specifications, material choices, and performance characteristics.
What is the typical lead time for production?
Lead times can vary based on complexity and order volume, but generally range from a few weeks to several months.
What testing is performed on Buried Cavity Package Substrates?
Testing may include electrical continuity, Ciclo térmico, mechanical reliability, and visual inspections to ensure quality and performance.