Showa Denko MCL-E-705G Package Substrate Manufacturer
Showa Denko MCL-E-705G Package Substrate Manufacturer,Showa Denko MCL-E-705G package substrates represent the pinnacle of innovation in semiconductor packaging technology. Engineered with precision and expertise by Showa Denko, a global leader in electronic materials, these substrates offer unparalleled performance and reliability for advanced electronic devices.
Crafted from high-quality organic laminate materials, MCL-E-705G substrates provide exceptional electrical conductivity, Thermomanagement, and signal integrity. Their high-density interconnects and low electrical noise ensure optimal performance even in the most demanding applications, such as consumer electronics, automotive systems, telecommunications infrastructure, and high-performance computing.
With a commitment to excellence, Showa Denko meticulously manufactures MCL-E-705G substrates using state-of-the-art production processes and stringent quality control measures. Each substrate undergoes thorough inspection and testing to meet the highest industry standards, guaranteeing consistent performance and durability.
From their superior material composition to their precise construction, Showa Denko MCL-E-705G package substrates exemplify reliability, efficiency, and innovation, making them the preferred choice for semiconductor packaging solutions in today’s dynamic electronics market.
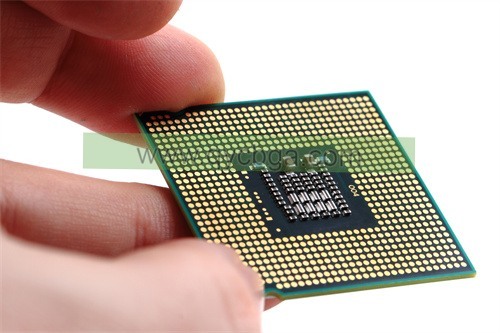
Showa Denko MCL-E-705G Package Substrate Manufacturer
What is the Showa Denko MCL-E-705G package substrate?
The Showa Denko MCL-E-705G package substrate is a type of material used in the packaging of semiconductor chips. It belongs to a class of substrates known as organic substrates, which are crucial components in the creation of integrated circuit (ISCH) packages. These substrates provide the necessary mechanical support and connection points for semiconductor devices to interact with external circuits.
Specifically, the MCL-E-705G is an example of a high-performance organic laminate substrate. Such substrates are typically composed of a layered structure that includes a core material (often fiberglass-reinforced epoxy resin) and multiple layers of copper circuitry separated by dielectric materials. This construction allows for the efficient routing of electrical signals between the chip and the package’s external leads.
Showa Denko, the manufacturer of MCL-E-705G, is a Japanese chemical company known for its contributions to the electronic materials industry, among other sectors. The MCL-E-705G substrate is likely designed to meet high thermal and electrical performance requirements, making it suitable for use in advanced semiconductor devices that require robust and reliable packaging solutions.
Key characteristics of such substrates may include:
– High-density interconnects: Ability to support a large number of connections per area, which is important for modern, high-pin-count ICs.
– Thermal management capabilities: Efficiently dissipates heat generated by the semiconductor device, helping to maintain optimal operating temperatures.
– Low electrical noise: Designed to minimize interference and signal degradation, which is critical for maintaining the performance of high-speed electronic circuits.
This type of substrate is vital in numerous applications, including consumer electronics, Fahrzeugelektronik, and high-performance computing devices, where reliability and efficiency are paramount.
What are the Showa Denko MCL-E-705G package substrate Design Guidelines?
Specific design guidelines for the Showa Denko MCL-E-705G package substrate may vary depending on factors such as the specific requirements of the semiconductor device being packaged and the manufacturer’s recommendations. Aber, some general design considerations typically apply when working with high-performance organic laminate substrates like the MCL-E-705G. Here are some common design guidelines:
- Materialauswahl: Ensure that the substrate materials, including the core material, copper layers, and dielectric materials, meet the required specifications for thermal performance, Elektrische Eigenschaften, and mechanical strength. The MCL-E-705G datasheet or technical documentation provided by Showa Denko should specify the material properties and limitations.
- Layer Stackup Design:Design the layer stackup of the substrate to optimize signal integrity, Energieverteilung, und Thermomanagement. Berücksichtigen Sie Faktoren wie das Signalrouting, via placement, Verteilung der Leistungsebene, and impedance control.
- Signalintegrität: Minimize signal distortion, Übersprechen, and electromagnetic interference (EMI) by adhering to best practices for signal routing, impedance matching, and ground plane design. Follow recommended trace geometries and keep signal traces as short and direct as possible.
- Thermisches Management: Design the substrate with adequate thermal vias, thermal pads, and heat spreaders to dissipate heat generated by the semiconductor device efficiently. Ensure proper thermal coupling between the device and the substrate to prevent thermal issues such as hot spots.
- Package Dimensions and Layout: Ensure that the package dimensions and layout accommodate the size and shape of the semiconductor device, as well as any external mechanical or electrical requirements. Pay attention to clearance and spacing requirements to prevent short circuits or mechanical interference.
- Überlegungen zur Zuverlässigkeit: Design the substrate to withstand mechanical stresses, Thermische Zyklen, and environmental factors such as moisture and humidity. Follow industry standards and guidelines for reliability testing and qualification.
- Herstellbarkeit: Consider manufacturability factors such as panelization, tooling holes, fiducial markers, and solder mask design to facilitate the fabrication and assembly processes. Work closely with the substrate manufacturer to optimize the design for production efficiency.
- Documentation and Communication: Dokumentieren Sie das Substratdesign gründlich, including schematics, layout files, fabrication drawings, and assembly instructions. Communicate effectively with all stakeholders, including the substrate manufacturer, semiconductor device designer, and assembly contractor.
It’s essential to consult with Showa Denko or a qualified substrate design expert for specific design guidelines and recommendations tailored to the MCL-E-705G substrate and your application requirements.
What is the Showa Denko MCL-E-705G package substrate Fabrication Process?
The specific fabrication process for the Showa Denko MCL-E-705G package substrate is proprietary information and may not be publicly available. Aber, I can provide a general overview of the typical fabrication process for organic laminate substrates like the MCL-E-705G:
- Material Preparation: The fabrication process begins with the preparation of substrate materials, including the core material (often fiberglass-reinforced epoxy resin), copper foil, and dielectric materials. These materials are inspected for quality and may undergo surface treatment processes to improve adhesion and compatibility.
- Layer Stackup Formation: Multiple layers of core material, copper foil, and dielectric materials are laminated together to form a layered structure. This layer stackup is designed to provide the necessary electrical connectivity and mechanical support for the semiconductor device.
- Circuit Patterning: Copper foil layers are selectively etched using photolithography and chemical etching processes to define the circuitry patterns, including signal traces, power planes, and ground planes. These processes require the use of photoresist masks to protect desired areas of the copper surface while etching away unwanted areas.
- Über die Formation: Vias, which are small holes drilled or formed through the substrate layers, are created to establish electrical connections between different circuit layers. Vias may be formed using mechanical drilling, laser drilling, or sequential build-up (SBU) processes, depending on the substrate design requirements.
- Oberflächengüte: The exposed copper surfaces are typically treated with surface finishes to improve solderability, corrosion resistance, und Zuverlässigkeit. Common surface finishes include electroless nickel immersion gold (ENIG), organic solderability preservative (OSP), and immersion silver.
- Solder Mask Application: A solder mask layer is applied over the substrate surface to define the areas where solder will adhere during the assembly process. Solder mask material is typically applied using screen printing or liquid photoimageable (LPI) processes, followed by curing and exposure to UV light to define the mask openings.
- Final Inspection and Testing: The fabricated substrate undergoes thorough inspection and testing to ensure quality and compliance with specifications. This may include dimensional measurements, electrical continuity testing, solderability testing, and visual inspection for defects.
- Verpackung und Versand: Once the substrates pass inspection, they are packaged according to customer requirements and shipped to semiconductor device manufacturers for assembly into integrated circuits.
It’s important to note that the actual fabrication process may vary depending on factors such as substrate design complexity, manufacturing equipment capabilities, and specific customer requirements. Zusätzlich, Showa Denko may have proprietary processes and technologies that are not disclosed to the public. For detailed information on the fabrication process for the MCL-E-705G substrate, it’s best to consult directly with Showa Denko or their authorized representatives.
How do you manufacture a Showa Denko MCL-E-705G package substrate?
The specific manufacturing process for the Showa Denko MCL-E-705G package substrate is proprietary information owned by Showa Denko, and the company may not publicly disclose all the details. Aber, I can provide a generalized overview of the typical steps involved in manufacturing organic laminate substrates like the MCL-E-705G:
- Material Preparation: The manufacturing process begins with the preparation of raw materials, including the core material (often fiberglass-reinforced epoxy resin), copper foil, and dielectric materials. These materials undergo quality control checks and may be subjected to surface treatment processes to enhance adhesion and compatibility.
- Layer Stackup Formation: Multiple layers of core material, copper foil, and dielectric materials are laminated together to form a layered substrate structure. This layer stackup provides the necessary electrical connectivity and mechanical support for the semiconductor device.
- Circuit Patterning: Copper foil layers are selectively etched to define the circuitry patterns, including signal traces, power planes, and ground planes. This process typically involves photolithography to transfer the circuit patterns onto the copper surface using photoresist masks, followed by chemical etching to remove unwanted copper.
- Über die Formation: Vias are created to establish electrical connections between different circuit layers. Vias may be formed using mechanical drilling, laser drilling, or sequential build-up (SBU) processes, depending on the substrate design requirements.
- Oberflächengüte:Exposed copper surfaces are treated with surface finishes to improve solderability, corrosion resistance, und Zuverlässigkeit. Common surface finishes include electroless nickel immersion gold (ENIG), organic solderability preservative (OSP), and immersion silver.
- Solder Mask Application: A solder mask layer is applied over the substrate surface to define the areas where solder will adhere during the assembly process. Solder mask material is typically applied using screen printing or liquid photoimageable (LPI) processes, followed by curing and exposure to UV light to define the mask openings.
- Final Inspection and Testing: The manufactured substrates undergo comprehensive inspection and testing to ensure quality and compliance with specifications. This may include dimensional measurements, electrical continuity testing, solderability testing, and visual inspection for defects.
- Verpackung und Versand:Once the substrates pass inspection, they are packaged according to customer requirements and shipped to semiconductor device manufacturers for assembly into integrated circuits.
It’s important to note that the actual manufacturing process may vary depending on factors such as substrate design complexity, available manufacturing equipment, and specific customer requirements. For detailed information on the manufacturing process for the MCL-E-705G substrate, it’s best to consult directly with Showa Denko or their authorized representatives.
How much should a Showa Denko MCL-E-705G package substrate cost?
The cost of a Showa Denko MCL-E-705G package substrate can vary based on several factors, including the substrate’s size, thickness, material specifications, volume of purchase, and market conditions. Since pricing information for specific components like the MCL-E-705G substrate is often proprietary and subject to negotiation between the buyer and the supplier, it may not be readily available to the public.
Factors affecting the cost of package substrates may include:
- Size and Thickness: Larger substrates or those with thicker layers may cost more due to increased material usage and manufacturing complexity.
- Material Specifications: Different substrate materials and surface finishes can affect the cost. Higher-performance materials or specialized surface finishes may come at a premium.
- Volume of Purchase: Bulk orders typically result in lower per-unit costs due to economies of scale. Larger quantities may also allow for negotiation of discounts with the supplier.
- Customization and Additional Features: Any customization, such as specific layer stackups, unique designs, or additional features, may increase the cost of the substrate.
- Marktlage: Supply and demand dynamics, as well as fluctuations in raw material prices, can impact substrate pricing over time.
To obtain accurate pricing information for the Showa Denko MCL-E-705G package substrate, it’s best to directly contact Showa Denko or their authorized distributors. They can provide quotes based on your specific requirements and volume needs. Zusätzlich, consulting with multiple suppliers can help you compare prices and negotiate favorable terms.
What is the Showa Denko MCL-E-705G package substrate base material?
The base material of the Showa Denko MCL-E-705G package substrate is typically an organic laminate material. Organic laminate substrates are commonly used in the semiconductor packaging industry due to their excellent electrical properties, thermal performance, and mechanical reliability.
While the exact composition and formulation of the base material may be proprietary information held by Showa Denko, organic laminate substrates typically consist of several layers:
- Core Material: The core material forms the foundation of the substrate and provides mechanical support. It is often composed of fiberglass-reinforced epoxy resin (FR-4), though other materials such as BT (bismaleimide triazine) resin or polyimide may also be used depending on the specific requirements of the application.
- Copper Foil: Thin layers of copper foil are typically bonded to both sides of the core material to form conductive pathways for electrical connections. The copper foil is patterned and etched to create the desired circuitry.
- Dielectric Layers: Dielectric materials are interspersed between the copper layers to insulate and separate conductive traces. These dielectric layers help prevent electrical shorts and provide impedance control for high-speed signal transmission.
The combination of these materials provides the necessary electrical, mechanical, and thermal properties required for semiconductor packaging applications. Zusätzlich, surface finishes and solder mask layers are applied to the substrate to enhance solderability, protect against corrosion, and define the areas for solder attachment during the assembly process.
For specific information on the base material composition of the MCL-E-705G substrate, it would be best to refer to Showa Denko’s technical documentation or contact the company directly for details.
Which company manufactures Showa Denko MCL-E-705G package substrate?
The Showa Denko MCL-E-705G package substrates are manufactured by Showa Denko, a Japanese company. Showa Denko is a globally renowned chemical company with a long history and extensive experience. The company possesses outstanding technological prowess and innovative capabilities in the field of electronic materials. With advanced manufacturing processes and equipment in the realm of package substrates, Showa Denko can produce high-performance MCL-E-705G package substrates to meet the demands of customers for high-speed, high-density, and highly reliable electronic packaging.
As a professional electronic materials manufacturer, our company also has the capability to manufacture Showa Denko MCL-E-705G package substrates. We have advanced production equipment and a skilled technical team to customize and produce high-quality substrates according to customer requirements. We are committed to continuously improving our technological expertise and optimizing production processes to ensure the delivery of products that meet customer needs. Quality management is paramount to us, and we strictly adhere to international standards and regulations to ensure stable and reliable product quality. Zusätzlich, we prioritize communication and collaboration with customers, actively listening to their needs and feedback to provide satisfactory service and solutions.
Through our efforts and unwavering dedication, we believe that we can become a reliable supplier of Showa Denko MCL-E-705G package substrates, offering customers high-quality products and services to collectively promote the development and advancement of the electronics industry.
What are the 7 qualities of good customer service?
Good customer service is characterized by several key qualities that contribute to positive interactions and experiences for customers. Here are seven qualities of good customer service:
- Responsiveness: Good customer service involves promptly addressing customer inquiries, concerns, and requests. Responding in a timely manner shows customers that their needs are valued and that the company is attentive to their concerns.
- Empathy: Empathy is the ability to understand and share the feelings of others. Customer service representatives who demonstrate empathy show genuine concern for customers’ experiences and strive to understand their perspectives. Empathetic responses help build rapport and trust with customers.
- Clear Communication: Effective communication is essential for providing good customer service. Customer service representatives should communicate clearly and concisely, using language that is easy for customers to understand. They should also actively listen to customers and provide accurate information and guidance.
- Problem-Solving Skills: Good customer service involves resolving customer issues and problems effectively. Customer service representatives should be equipped with problem-solving skills to identify root causes, explore solutions, and address customers’ concerns in a satisfactory manner.
- Professionalism: Professionalism encompasses qualities such as courtesy, politeness, and respectfulness in interactions with customers. Customer service representatives should maintain a professional demeanor at all times, even when faced with challenging situations or difficult customers.
- Product Knowledge: A good understanding of the company’s products or services is essential for providing effective customer service. Customer service representatives should be knowledgeable about the features, benefits, and uses of the products or services they support, enabling them to answer questions and provide helpful recommendations to customers.
- Follow-Up and Resolution: After resolving a customer issue, good customer service involves following up with the customer to ensure their satisfaction and to address any lingering concerns. Following through on commitments and ensuring that customer issues are fully resolved demonstrates dedication to customer satisfaction and retention.
By embodying these qualities, businesses can cultivate a customer-centric culture and build strong relationships with their customer base, ultimately leading to increased loyalty, positive word-of-mouth referrals, and business growth.
FAQs
What is Showa Denko MCL-E-705G package substrate?
The Showa Denko MCL-E-705G package substrate is a type of high-performance organic laminate substrate used in the packaging of semiconductor chips. It provides electrical interconnects and thermal management for integrated circuits.
What are the key features of MCL-E-705G package substrates?
MCL-E-705G substrates offer high-density interconnects, excellent thermal management capabilities, and low electrical noise. They are designed to meet the demanding requirements of modern semiconductor devices.
What are the advantages of using MCL-E-705G substrates?
MCL-E-705G substrates provide superior electrical performance, Zuverlässigkeit, and thermal dissipation compared to conventional packaging substrates. They enable the development of high-speed, high-density electronic devices.
What applications are suitable for MCL-E-705G package substrates?
MCL-E-705G substrates are suitable for a wide range of applications, including consumer electronics, Fahrzeugelektronik, Telekommunikation, and high-performance computing.
What sizes and configurations are available for MCL-E-705G substrates?
MCL-E-705G substrates are available in various sizes and configurations to accommodate different semiconductor device requirements. Customization options may also be available to meet specific customer needs.
What is the manufacturing process for MCL-E-705G package substrates?
The manufacturing process typically involves material preparation, layer stackup formation, circuit patterning, via formation, oberflächenveredelung, solder mask application, final inspection, and packaging.
Where can I obtain more information or request a quote for MCL-E-705G substrates?
For more information about MCL-E-705G package substrates or to request a quote, you can contact Showa Denko directly or their authorized distributors. They can provide detailed technical specifications, pricing information, and assistance with product selection.