RO4350B PCB | High Frequency PCB Manufacturer
RO4350B PCB | High Frequency PCB Manufacturer,RO4350B PCB is a type of printed circuit board designed specifically for high-frequency applications, utilizing Rogers Corporation’s RO4350B high-frequency laminate material. This material boasts low dielectric loss, stable electrical properties, and excellent thermal conductivity, making it an ideal choice for high-frequency circuit designs. RO4350B PCBs offer outstanding signal integrity and reliability, suitable for various high-frequency applications such as RF and microwave circuits, communication equipment, antenna systems, and high-speed digital circuits. Their advantages include predictable electrical performance, good thermal management capabilities, and adaptability to high-density circuit designs. Designing RO4350B PCBs requires attention to controlled impedance, proper grounding, routing, und Thermomanagement. The fabrication of RO4350B PCBs typically follows standard PCB manufacturing processes, including material preparation, circuit design and layout, Bohrung, copper plating, circuit patterning, surface treatment, solder mask, and silkscreen printing. RO4350B PCBs excel in various high-frequency applications, providing essential support for the reliable operation of electronic products.
What is a RO4350B PCB?
RO4350B is a type of high-frequency laminate material commonly used in the fabrication of printed circuit boards (Leiterplatten). It belongs to the RO4000® series of circuit materials developed by Rogers Corporation, a leading manufacturer of advanced materials for electronics.
RO4350B PCBs are engineered to offer excellent electrical performance, particularly in high-frequency applications such as RF (Radiofrequenz) and microwave circuits. Some key characteristics of RO4350B material include low dielectric loss, stable electrical properties over a wide frequency range, and good thermal conductivity.
These properties make RO4350B PCBs suitable for various applications in telecommunications, aerospace, defense, automotive radar systems, and other industries where high-frequency signal integrity and reliability are critical.
Insgesamt, RO4350B PCBs are valued for their high performance, Zuverlässigkeit, and consistency, making them a popular choice for demanding electronic designs.
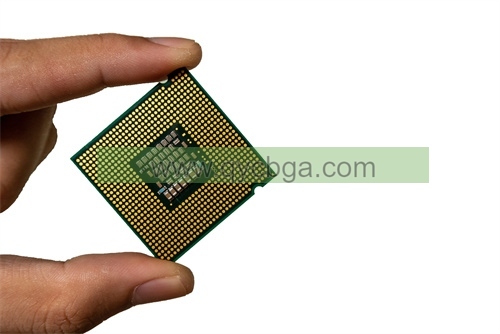
RO4350B PCB | High Frequency PCB Manufacturer
What are the RO4350B PCB Design Guidelines?
Designing with RO4350B PCBs requires adherence to specific guidelines to ensure optimal performance and reliability. Here are some general design guidelines for RO4350B PCBs:
- Materialauswahl: Choose RO4350B laminate material with the appropriate thickness and copper foil weight based on your application requirements.
- Trace Width and Spacing: Maintain adequate trace widths and spacing to minimize signal losses, Übersprechen, and impedance variations. Use impedance calculation tools to determine the required trace dimensions for your desired impedance.
- Ground Plane: Ensure a solid ground plane on one or both sides of the PCB to provide a low impedance return path for signals and to reduce electromagnetic interference (EMI).
- Via Design:Use short, stub-free vias with low inductance and impedance for signal transitions between layers. Avoid excessive via stubs, as they can introduce signal integrity issues.
- Component Placement: Place high-frequency components, such as RF connectors, transmission lines, and matching networks, with care to minimize signal path lengths and impedance mismatches.
- Thermisches Management: Consider thermal management techniques, such as heat sinks or thermal vias, to dissipate heat generated by high-power components or dense circuitry.
- Solder Mask and Silkscreen: Apply solder mask and silkscreen layers carefully to prevent solder bridging and ensure clear component labeling without obstructing critical signal paths.
- Edge Treatment: Apply appropriate edge treatments, such as beveling or chamfering, to reduce fringing fields and prevent potential signal reflections at the board edges.
- Signal Integrity Simulation: Perform signal integrity simulations using specialized software to analyze high-frequency behavior, predict impedance mismatches, and optimize the PCB layout accordingly.
- Quality Control: Implement stringent quality control measures during fabrication and assembly processes to ensure consistent impedance, tight tolerances, and minimal defects in the final PCB.
By following these guidelines, designers can maximize the performance and reliability of RO4350B PCBs in high-frequency applications. Zusätzlich, consulting with experienced RF and microwave engineers or utilizing design tools specific to high-frequency PCB design can further enhance the design process.
What is the RO4350B PCB Fabrication Process?
The fabrication process for RO4350B PCBs is similar to that of standard PCBs, but there are specific considerations due to the high-frequency characteristics of the material. Here’s an overview of the typical fabrication process for RO4350B PCBs:
- Material Preparation: Begin by selecting RO4350B laminate material in the desired thickness and copper foil weight based on the specific requirements of the application. Ensure that the material is stored and handled properly to prevent any damage or contamination.
- Circuit Design and Layout: Create the PCB layout using specialized design software that takes into account the high-frequency characteristics of RO4350B material. Pay careful attention to trace widths, spacing, Impedanzkontrolle, ground plane configuration, and via placement to optimize signal integrity and minimize losses.
- Film Generation: Generate the necessary films for the PCB fabrication process, including the artwork films for the copper layers, solder mask, and silkscreen layers. These films serve as templates for the subsequent manufacturing steps.
- Drilling: Use precision drilling equipment to create holes for component mounting and via connections. Ensure that the drill sizes and tolerances are compatible with the design requirements and the capabilities of the fabrication equipment.
- Copper Plating: Apply a thin layer of copper through the process of electroplating to the walls of the drilled holes, forming the vias that will provide electrical connections between different layers of the PCB.
- Circuit Patterning: Apply a layer of photoresist material onto the copper-clad laminate and expose it to UV light through the artwork films to transfer the circuit pattern onto the board. Then, develop and etch the exposed areas to remove unwanted copper, leaving behind the desired circuit traces.
- Oberflächengüte: Apply a surface finish to protect the exposed copper traces from oxidation and facilitate solderability during assembly. Common surface finish options include immersion gold, immersion silver, ENIG (Electroless Nickel Immersion Gold), and HASL (Hot Air Solder Leveling).
- Solder Mask Application: Apply solder mask material over the entire surface of the PCB, leaving openings for component pads and vias. The solder mask provides insulation and protection for the circuit traces while allowing soldering only where necessary.
- Silkscreen Printing: Print component designators, logos, and other identifying information onto the PCB surface using a silkscreen printing process. This step helps in component placement and identification during assembly.
- Final Inspection: Conduct a thorough inspection of the fabricated PCBs to ensure that they meet the specified design requirements, including dimensional accuracy, trace continuity, Impedanzkontrolle, and solder mask alignment.
Following these steps with precision and attention to detail is crucial for producing high-quality RO4350B PCBs that meet the stringent performance requirements of high-frequency applications. Collaboration with experienced PCB manufacturers familiar with RF and microwave circuitry can further ensure the success of the fabrication process.
How do you manufacture a RO4350B PCB?
Manufacturing a RO4350B PCB involves several steps, from material preparation to final inspection. Here’s a detailed overview of the manufacturing process:
- Materialauswahl: Choose RO4350B laminate material with the appropriate thickness and copper foil weight based on the application requirements.
- Preparation of Substrate: Cut the RO4350B laminate sheets to the required size using precision cutting equipment. Ensure that the material is handled carefully to prevent any damage or contamination.
- Cleaning and Surface Treatment: Clean the substrate surface thoroughly to remove any dirt, grease, or contaminants that could affect adhesion or solderability. Apply surface treatments as necessary to promote proper adhesion of copper and other materials during subsequent processing steps.
- Copper Cladding: Laminate a thin layer of copper foil onto one or both sides of the RO4350B substrate using a lamination press or adhesive bonding process. The thickness of the copper foil should be selected based on the specific application requirements and impedance targets.
- Drilling: Use precision drilling equipment to create holes for component mounting and interconnection vias. Ensure that the drill sizes and tolerances are compatible with the design requirements and the capabilities of the fabrication equipment.
- Circuit Patterning: Apply a layer of photoresist material onto the copper-clad laminate and expose it to UV light through the artwork films to transfer the circuit pattern onto the board. Develop and etch the exposed areas to remove unwanted copper, leaving behind the desired circuit traces.
- Oberflächengüte: Apply a surface finish to protect the exposed copper traces from oxidation and facilitate solderability during assembly. Common surface finish options for RO4350B PCBs include immersion gold, immersion silver, ENIG (Electroless Nickel Immersion Gold), and HASL (Hot Air Solder Leveling).
- Solder Mask Application: Apply solder mask material over the entire surface of the PCB, leaving openings for component pads and vias. The solder mask provides insulation and protection for the circuit traces while allowing soldering only where necessary.
- Silkscreen Printing: Print component designators, logos, and other identifying information onto the PCB surface using a silkscreen printing process. This step helps in component placement and identification during assembly.
- Final Inspection: Conduct a comprehensive inspection of the fabricated PCBs to ensure that they meet the specified design requirements, including dimensional accuracy, trace continuity, Impedanzkontrolle, solder mask alignment, and surface finish quality.
- Testing and Electrical Characterization: Perform electrical testing and characterization of the fabricated PCBs to verify their performance and functionality. This may involve impedance testing, continuity testing, and other electrical measurements to ensure compliance with the desired specifications.
- Verpackung und Versand: Package the finished PCBs securely to protect them from damage during transit, and arrange for their shipment to the customer or assembly facility.
By following these steps with precision and attention to detail, manufacturers can produce high-quality RO4350B PCBs that meet the stringent performance requirements of high-frequency applications. Collaboration with experienced PCB manufacturers familiar with RF and microwave circuitry can further ensure the success of the manufacturing process.
How much should a RO4350B PCB cost?
The cost of a RO4350B PCB can vary depending on several factors, einschließlich:
- Board Size and Complexity: Larger boards with more complex designs require more materials and processing time, which can increase the cost.
- Layer Count: The number of layers in the PCB affects manufacturing complexity and material usage. RO4350B PCBs can range from single-layer to multi-layer designs.
- Material Specifications: The thickness and copper weight of the RO4350B laminate, as well as any additional features like surface finish and solder mask type, kann die Kosten beeinflussen.
- Menge: Economies of scale often apply in PCB manufacturing, meaning that larger production runs generally result in lower per-unit costs.
- Turnaround Time: Expedited or quick-turn PCB fabrication services may incur additional fees compared to standard lead times.
- Quality Standards:Meeting specific quality standards or certifications may involve additional testing and inspection procedures, which can impact the overall cost.
- Lieferant und Standort: PCB fabrication costs can vary between different suppliers and regions due to factors such as labor costs, overheads, and market competitiveness.
To get an accurate cost estimate for a RO4350B PCB, it’s best to consult with PCB manufacturers or suppliers directly. Provide them with detailed specifications, including board dimensions, layer count, material requirements, surface finish, quantity needed, and any special considerations. Many PCB manufacturers offer online quotation tools or can provide custom quotes based on your specific requirements.
What is RO4350B PCB base material?
RO4350B PCBs are constructed using a specialized high-frequency laminate material known as RO4350B. This laminate is a proprietary product of Rogers Corporation, a leading manufacturer of advanced materials for electronics. RO4350B is part of the RO4000® series of circuit materials, which are specifically engineered for high-frequency applications.
The base material of RO4350B consists of a ceramic-filled hydrocarbon thermoset resin system with woven glass reinforcement. This combination of materials provides excellent electrical performance, dimensional stability, and mechanical strength, making RO4350B well-suited for use in high-frequency PCBs.
Key characteristics of RO4350B base material include:
- Low Dielectric Loss: RO4350B exhibits low loss tangent, which minimizes signal attenuation and ensures high signal integrity, particularly at microwave frequencies.
- Stable Electrical Properties: The dielectric constant and dissipation factor of RO4350B are stable over a wide frequency range, allowing for predictable performance in high-frequency circuits.
- Uniformity: RO4350B material offers excellent dimensional stability and uniformity, which is crucial for maintaining consistent impedance and signal integrity across the PCB.
- Thermal Conductivity: While not as high as some metal-core PCB materials, RO4350B still exhibits good thermal conductivity, aiding in heat dissipation from high-power components.
- Flammschutzmittel: RO4350B laminate meets various industry standards for flame retardancy, ensuring compliance with safety requirements.
Insgesamt, the RO4350B base material provides a reliable foundation for the fabrication of high-performance PCBs, particularly in applications where low loss and stable electrical properties are critical, such as RF (Radiofrequenz) and microwave circuits.
Which company makes RO4350B PCB?
RO4350B PCBs are produced by Rogers Corporation. Rogers Corporation is a globally leading electronic materials manufacturer, specializing in providing high-performance material solutions for various industries. Their RO4000® series products are specifically developed for high-frequency circuit designs, among which RO4350B is one of the materials.
RO4350B PCBs utilize the RO4350B substrate developed by Rogers Corporation, which features low dielectric loss, stable electrical performance, and excellent mechanical properties. This substrate is a ceramic-filled thermoset resin system with glass fiber reinforcement, suitable for applications requiring stable signal transmission and reliability in high-frequency domains.
Our company is also capable of manufacturing RO4350B PCBs. As a professional PCB manufacturer, we possess advanced production equipment and technology to meet customers’ demands for high-frequency circuits. Our experienced team can provide customized solutions for RO4350B PCBs, including single-layer to multi-layer boards, high-frequency characteristic control, and precision hole drilling. We strictly adhere to manufacturing processes and quality management systems to ensure the production of high-quality RO4350B PCBs that meet customer specifications.
By choosing our company as your partner, you will benefit from:
- Professional Team Support: Our experienced engineering team can provide technical support and customized solutions.
- Advanced Equipment: We have invested in state-of-the-art production equipment to ensure the production of high-quality RO4350B PCBs.
- Strict Quality Control: We strictly adhere to quality management processes to ensure that each PCB meets customer specifications and requirements.
- Flexible Production: We can provide flexible production solutions according to customer needs, including small batch and large batch production.
By choosing our company as your RO4350B PCB manufacturer, you can confidently obtain high-quality, reliable products and enjoy professional technical support and excellent customer service.
What are the 7 qualities of good customer service?
Good customer service is characterized by several key qualities that contribute to positive experiences for customers. Here are seven qualities of good customer service:
- Responsiveness: Good customer service involves being prompt and proactive in addressing customer inquiries, concerns, and requests. Responding promptly to customer inquiries shows that you value their time and are committed to providing assistance when needed.
- Empathy: Empathy involves understanding and acknowledging the customer’s perspective, feelings, and needs. Good customer service representatives demonstrate empathy by actively listening to customers, showing understanding of their situation, and expressing genuine concern for their satisfaction.
- Professionalism: Professionalism in customer service encompasses aspects such as politeness, courtesy, and professionalism in communication and interactions with customers. Maintaining a professional demeanor, even in challenging situations, helps to build trust and credibility with customers.
- Knowledgeability: Good customer service representatives are knowledgeable about the products or services they are supporting. They possess the expertise to answer customer questions accurately, provide relevant information, and offer helpful recommendations or solutions to address customer needs.
- Problem-solving skills: Effective problem-solving skills are essential for resolving customer issues and concerns efficiently and satisfactorily. Good customer service involves identifying the root cause of problems, proposing viable solutions, and taking proactive steps to resolve issues to the customer’s satisfaction.
- Adaptability: Good customer service requires adaptability to meet the diverse needs and preferences of customers. This involves being flexible and willing to adjust communication styles, approaches, and solutions to accommodate individual customer preferences and circumstances.
- Consistency: Consistency in customer service ensures that customers receive a consistently high level of service across all interactions and touchpoints with the organization. Maintaining consistency in service delivery helps to build trust, loyalty, and positive relationships with customers over time.
By embodying these qualities, organizations can provide exceptional customer service experiences that foster customer satisfaction, loyalty, and advocacy.
FAQs
What is RO4350B PCB?
RO4350B PCB is a type of printed circuit board (PLATINE) that uses RO4350B laminate material as its base. This material is specifically designed for high-frequency applications, such as RF (Radiofrequenz) and microwave circuits, due to its low dielectric loss and stable electrical properties.
What are the key characteristics of RO4350B PCBs?
The key characteristics of RO4350B PCBs include low dielectric loss, stable electrical properties over a wide frequency range, excellent thermal conductivity, and dimensional stability. These properties make them ideal for high-frequency applications where signal integrity and reliability are critical.
What are the advantages of using RO4350B PCBs?
Some advantages of using RO4350B PCBs include high performance in high-frequency applications, minimal signal loss, predictable electrical properties, and good thermal management capabilities. They are also suitable for applications requiring high-density circuitry and impedance-controlled designs.
What are typical applications for RO4350B PCBs?
RO4350B PCBs are commonly used in various applications, including telecommunications, aerospace, defense, automotive radar systems, wireless communication devices, and high-speed digital circuits. They are suitable for RF amplifiers, antennas, transceivers, power dividers, and other high-frequency components.
How do I design a RO4350B PCB?
Designing a RO4350B PCB involves considerations such as trace widths and spacing for controlled impedance, ground plane configuration, via design, Thermomanagement, and adherence to manufacturer’s design guidelines. Using specialized PCB design software and consulting with experienced RF engineers can help optimize the design for high-frequency performance.
What are the fabrication options for RO4350B PCBs?
RO4350B PCBs can be fabricated using standard PCB manufacturing processes, including material preparation, circuit design and layout, Bohrung, copper plating, circuit patterning, surface finish application, solder mask application, silkscreen printing, final inspection, and testing.