Radar/Antenna Substrate Manufacturer
Radar/Antenna Substrate Manufacturer,The radar/antenna substrate is a crucial electronic material used to support the performance of radar systems and antennas. It is typically composed of high-frequency electronic materials such as ceramics or polymers, possessing excellent electrical characteristics and weather resistance. The design of radar/antenna substrates must take into account factors such as frequency response, dielectric constant, thermal conductivity, and mechanical strength. These substrates often need to have low losses to ensure the efficient performance of radar systems. Zusätzlich, they must have sufficient durability to reliably operate in various environmental conditions, including high temperatures, Feuchtigkeit, and pressure. The precision manufacturing and optimized design of radar/antenna substrates are essential for achieving high-performance radar systems, and they have widespread applications in military, civil aviation, and communication sectors.
What is a Radar/Antenna Substrate?
A radar/antenna substrate, also known as a radome, is a protective covering that encapsulates radar or antenna systems. It serves several critical functions:
- Protection: The substrate shields the delicate radar or antenna components from harsh environmental conditions such as rain, wind, dust, and temperature extremes. It ensures the longevity and operational integrity of the system.
- Electromagnetic Transparency: It allows electromagnetic signals to pass through with minimal interference. This transparency is crucial for maintaining the performance and accuracy of radar and antenna systems.
- Durability: Radar/antenna substrates are designed to withstand physical impact and maintain structural integrity over time. They are often made from robust materials like fiberglass, composites, or specialized plastics.
- Aerodynamic Design:In applications such as aircraft or vehicles, radomes are aerodynamically shaped to minimize drag and maintain the overall performance of the platform.
- Cosmetic Appearance: In some cases, the substrate also contributes to the aesthetic appeal of the radar or antenna system, especially in consumer electronics or architectural installations.
Insgesamt, radar/antenna substrates play a crucial role in ensuring the functionality, Haltbarkeit, and performance of radar and antenna systems across various applications, from military defense to telecommunications and weather monitoring.
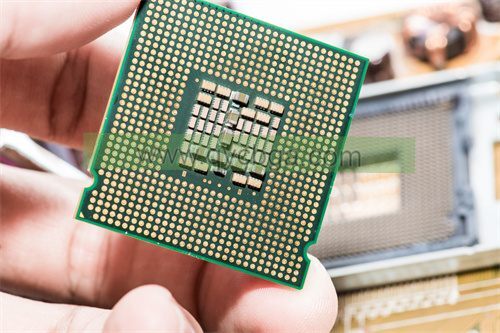
Radar/Antenna Substrate Manufacturer
What are the Radar/Antenna Substrate Design Guidelines?
Designing radar/antenna substrates requires careful consideration of various factors to ensure optimal performance and durability. Here are some key design guidelines:
- Materialauswahl: Choose materials that are transparent to the frequencies of interest. Common materials include fiberglass, composites, plastics, and specialized coatings. The material should also provide adequate structural strength and durability.
- Thickness and Shape: The thickness and shape of the substrate should be optimized for the specific application. Thinner substrates reduce signal loss but may sacrifice durability, while thicker substrates offer more protection but may introduce greater signal attenuation.
- Dielectric Constant: The substrate’s dielectric constant affects the propagation of electromagnetic waves. It should be chosen to minimize signal distortion and phase shift.
- Weather Resistance: Ensure that the substrate can withstand environmental factors such as rain, wind, temperature fluctuations, and UV exposure. Weather-resistant coatings or materials may be necessary, especially for outdoor installations.
- Aerodynamic Considerations: For applications in aerospace or automotive industries, design the substrate to minimize aerodynamic drag while maintaining structural integrity. Smooth, streamlined shapes are preferred.
- Mounting and Installation: Consider how the substrate will be mounted and integrated with the radar or antenna system. It should be securely attached without introducing additional signal loss or interference.
- Herstellbarkeit: Design the substrate for ease of manufacturing and assembly. Consider factors such as molding processes, material availability, und Wirtschaftlichkeit.
- Maintenance and Accessibility: Ensure that the substrate design allows for easy access to the underlying radar or antenna system for maintenance and repairs. Access panels or removable covers may be necessary.
- Electromagnetic Compatibility (EMC):Minimize electromagnetic interference (EMI) from the substrate itself by using materials with low conductivity and proper shielding techniques.
- Testing and Validation: Conduct thorough testing and validation of the substrate design to ensure that it meets performance specifications under real-world conditions. This may involve simulation studies, laboratory testing, and field trials.
By following these design guidelines, engineers can develop radar/antenna substrates that meet the requirements for performance, Haltbarkeit, and reliability in a wide range of applications.
What is the Radar/Antenna Substrate Fabrication Process?
The fabrication process for radar/antenna substrates involves several steps, including material selection, shaping, und Montage. Here’s a general overview of the typical fabrication process:
- Materialauswahl: Choose a suitable substrate material based on factors such as electromagnetic transparency, mechanische Festigkeit, weather resistance, und Herstellbarkeit. Common materials include fiberglass, composites, plastics, and specialized coatings.
- Molding or Shaping: Depending on the chosen material and substrate design, molding or shaping processes may be used to form the substrate into the desired shape. This can involve techniques such as injection molding, compression molding, or vacuum forming.
- Vorbereitung der Oberfläche: Prepare the substrate surface for further processing or coating. This may involve cleaning, sanding, or applying adhesion promoters to ensure proper bonding of subsequent layers.
- Coating Application: Apply any necessary coatings to the substrate surface to enhance weather resistance, electromagnetic transparency, or other performance characteristics. Coatings may include protective layers, weatherproofing treatments, or specialized materials to control electromagnetic properties.
- Integration of Components: If the radar/antenna substrate includes integrated components such as feed horns, waveguides, or mounting hardware, these components are assembled onto the substrate according to the design specifications. This may involve mechanical fastening, adhesive bonding, or other attachment methods.
- Quality Control: Conduct quality control checks throughout the fabrication process to ensure that the substrate meets the required specifications for dimensional accuracy, material properties, and performance characteristics. This may involve visual inspection, dimensional measurement, and functional testing.
- Final Finishing:Once the substrate assembly is complete, perform any final finishing operations such as trimming excess material, smoothing edges, or applying surface treatments to improve aesthetics and functionality.
- Verpackung und Versand: Package the finished radar/antenna substrates securely for transport to their intended destination. This may involve protective packaging materials to prevent damage during shipping and handling.
Throughout the fabrication process, it’s essential to adhere to industry standards and best practices to ensure the quality, Zuverlässigkeit, and performance of the radar/antenna substrates. Zusätzlich, documentation and traceability measures should be implemented to track materials, processes, and quality control procedures for future reference and quality assurance.
How do you manufacture a Radar/Antenna Substrate?
Manufacturing a radar/antenna substrate involves a series of steps to create a protective housing that allows electromagnetic signals to pass through with minimal interference. Here’s a general outline of the manufacturing process:
- Materialauswahl: Choose a substrate material that is transparent to the frequencies of interest and provides the necessary structural integrity and weather resistance. Common materials include fiberglass, composites, and specialized plastics.
- Design and Engineering: Develop detailed design specifications for the radar/antenna substrate, taking into account factors such as shape, dimensions, electromagnetic properties, and environmental requirements.
- Molding or Shaping: Form the substrate material into the desired shape using molding or shaping techniques such as injection molding, compression molding, or vacuum forming. This step creates the basic structure of the substrate.
- Vorbereitung der Oberfläche: Prepare the surface of the substrate for further processing or coating by cleaning, sanding, or applying adhesion promoters to ensure proper bonding of subsequent layers.
- Coating Application: Apply any necessary coatings to the substrate surface to enhance weather resistance, electromagnetic transparency, or other performance characteristics. Coatings may include protective layers, weatherproofing treatments, or specialized materials to control electromagnetic properties.
- Integration of Components: Assemble any integrated components such as feed horns, waveguides, or mounting hardware onto the substrate according to the design specifications. This may involve mechanical fastening, adhesive bonding, or other attachment methods.
- Quality Control: Conduct quality control checks throughout the manufacturing process to ensure that the substrate meets the required specifications for dimensional accuracy, material properties, and performance characteristics. This may involve visual inspection, dimensional measurement, and functional testing.
- Final Finishing: Perform any final finishing operations such as trimming excess material, smoothing edges, or applying surface treatments to improve aesthetics and functionality.
- Verpackung und Versand: Package the finished radar/antenna substrates securely for transport to their intended destination. This may involve protective packaging materials to prevent damage during shipping and handling.
Während des gesamten Herstellungsprozesses, it’s crucial to adhere to industry standards and best practices to ensure the quality, Zuverlässigkeit, and performance of the radar/antenna substrates. Documentation and traceability measures should also be implemented to track materials, processes, and quality control procedures for future reference and quality assurance.
How much should a Radar/Antenna Substrate cost?
The cost of a radar/antenna substrate can vary widely depending on several factors, einschließlich:
- Material: The type of material used for the substrate can significantly impact its cost. More advanced materials with specialized properties, such as high-frequency transparency or extreme weather resistance, may be more expensive than standard materials.
- Complexity: The complexity of the substrate design and manufacturing process can influence its cost. Substrates with intricate shapes, integrated components, or advanced coatings may require more time and resources to produce, increasing their cost.
- Quality:Higher quality substrates that meet stringent performance standards and undergo thorough testing and quality control processes may command a higher price.
- Menge:Economies of scale typically apply in manufacturing, meaning that larger production runs can lead to lower per-unit costs. Ordering larger quantities of radar/antenna substrates may result in volume discounts.
- Anpassung: Customized substrates tailored to specific requirements or applications may incur additional costs for design, engineering, and tooling.
- Supplier: The choice of supplier or manufacturer can impact the cost of radar/antenna substrates. Different suppliers may offer varying levels of quality, expertise, and pricing.
Without specific details about the requirements and specifications of the radar/antenna substrate, it’s challenging to provide an exact cost. Aber, to get an accurate estimate, it’s advisable to consult with manufacturers or suppliers directly, providing them with detailed information about the desired substrate specifications, Menge, and any customization needs. Zusätzlich, obtaining quotes from multiple suppliers can help compare costs and find the most competitive option.
What is Radar/Antenna Substrate Base Material?
The base material for radar/antenna substrates can vary depending on the specific requirements of the application and the desired properties of the substrate. Some common base materials used for radar/antenna substrates include:
- Fiberglas: Fiberglass is a popular choice for radar/antenna substrates due to its excellent strength-to-weight ratio, Haltbarkeit, and resistance to environmental factors such as moisture and corrosion. It can be molded into various shapes and is relatively cost-effective.
- Composite Materials: Composite materials, such as carbon fiber composites or glass-reinforced plastics (GRP), offer high strength and stiffness combined with lightweight properties. They are often used in aerospace and high-performance applications where weight reduction and structural integrity are critical.
- Specialized Plastics:Certain plastics, such as polycarbonate or acrylic, may be suitable for radar/antenna substrates, particularly in applications where transparency to electromagnetic signals is essential. These materials can be formed into complex shapes and offer good weather resistance.
- Ceramics:In some high-temperature or harsh environment applications, ceramics may be used as the base material for radar/antenna substrates due to their excellent heat resistance and mechanical properties.
- Metal Alloys: In certain cases, metal alloys such as aluminum or stainless steel may be used as the base material for radar/antenna substrates, particularly when high mechanical strength or thermal conductivity is required.
The choice of base material depends on factors such as the operating frequency of the radar/antenna system, environmental conditions, mechanical requirements, and cost considerations. Zusätzlich, coatings or surface treatments may be applied to the base material to enhance specific properties such as weather resistance, electromagnetic transparency, or durability.
Which company manufactures Radar/Antenna Substrates?
Many companies manufacture radar/antenna substrates, including aerospace companies that utilize advanced technologies and materials, communication equipment manufacturers, and specialized radar/antenna component suppliers. These companies typically have advanced design, engineering, and manufacturing capabilities to meet the requirements of various applications.
For our company, we can also manufacture radar/antenna substrates. We have advanced manufacturing equipment and technology, focusing on high-quality, customized product manufacturing. Here are our company’s capabilities and advantages in producing radar/antenna substrates:
- Engineering Design Capability: We have a seasoned engineering team capable of customizing the design of radar/antenna substrates according to customer requirements and specifications. We can provide professional consultation and technical support to ensure products meet performance and quality standards.
- Advanced Manufacturing Equipment: Equipped with advanced manufacturing equipment and processes, including injection molding, compression molding, coating technology, etc. These equipment can ensure products have high precision and consistent quality.
- Material Selection and Processing Technology: We are familiar with various common materials and processing technologies used for radar/antenna substrates, including fiberglass, composite materials, plastics, etc. We can choose the most suitable materials and adopt appropriate processing techniques according to customer requirements.
- Quality Control System: We have a strict quality control system to ensure compliance with specifications at every production step. Comprehensive quality checks and tests are conducted to ensure high-quality products that meet customer expectations.
- Customization Capability: We can customize radar/antenna substrates according to specific customer requirements, including shape, Größe, material, coating, etc. We can work closely with customers to provide personalized solutions.
Zusammenfassend, our company has the capabilities and experience to produce radar/antenna substrates, committed to providing high-quality, customized products and services. We welcome customers to contact us to learn more about our capabilities and solutions to meet their needs and expectations.
What are the 7 qualities of good customer service?
Good customer service is characterized by several key qualities that contribute to positive interactions and relationships between businesses and customers. Here are seven qualities of good customer service:
- Responsiveness:Good customer service involves being responsive to customer inquiries, requests, and concerns in a timely manner. This includes promptly answering phone calls, emails, and messages, as well as addressing customer issues promptly and efficiently.
- Empathy: Empathy is essential in understanding and acknowledging the emotions and perspectives of customers. Good customer service representatives show empathy by actively listening to customer concerns, expressing understanding, and showing genuine concern for their needs.
- Professionalism: Professionalism involves maintaining a courteous, respectful, and knowledgeable demeanor when interacting with customers. This includes using proper language and tone, adhering to company policies and procedures, and providing accurate information and assistance.
- Problem-Solving Skills: Good customer service representatives are adept at resolving customer issues and complaints effectively. This requires analytical thinking, creativity, and resourcefulness to identify solutions and address customer concerns to their satisfaction.
- Consistency: Consistency is key to building trust and credibility with customers. Good customer service is consistent across all interactions and touchpoints, ensuring that customers receive the same level of service and quality regardless of when or how they interact with the business.
- Personalization: Personalized customer service involves tailoring interactions and solutions to meet the individual needs and preferences of customers. This may include remembering customer preferences, addressing them by name, and offering personalized recommendations or solutions based on their specific situation.
- Follow-Up: Good customer service doesn’t end with resolving an immediate issue; it also involves following up with customers to ensure their satisfaction and to address any lingering concerns. Follow-up communication demonstrates care and commitment to customer satisfaction, fostering long-term relationships and loyalty.
By embodying these qualities, businesses can provide exceptional customer service that leaves a positive impression on customers and helps to build lasting relationships and brand loyalty.
FAQs
What is a radar/antenna substrate?
A radar/antenna substrate, also known as a radome, is a protective covering that encapsulates radar or antenna systems. It shields the delicate components from environmental factors while allowing electromagnetic signals to pass through with minimal interference.
What materials are used to make radar/antenna substrates?
Common materials for radar/antenna substrates include fiberglass, composites, specialized plastics, and coatings that offer electromagnetic transparency, Haltbarkeit, and weather resistance.
What are the key design considerations for radar/antenna substrates?
Design considerations include material selection, thickness, shape, electromagnetic transparency, weather resistance, aerodynamics (for aerospace applications), mounting and installation methods, manufacturability, and electromagnetic compatibility (EMC).
How are radar/antenna substrates manufactured?
The manufacturing process typically involves molding or shaping the substrate material, applying coatings for protection and performance enhancement, integrating components such as feed horns or waveguides, conducting quality control checks, and final finishing operations.
What are the applications of radar/antenna substrates?
Radar/antenna substrates are used in various applications, including aerospace and defense for radar systems on aircraft and missiles, telecommunications for satellite dishes and base station antennas, weather monitoring, automotive radar systems, und Unterhaltungselektronik.
How do radar/antenna substrates affect system performance?
Radar/antenna substrates can impact system performance by influencing signal transmission, reception, and overall system integrity. Proper substrate design and material selection are crucial to minimize signal loss, distortion, and interference.
What maintenance is required for radar/antenna substrates?
Maintenance may involve periodic inspection for damage or wear, cleaning to remove debris or contaminants that could affect signal transmission, and repair or replacement of damaged substrates to ensure continued performance and longevity of the radar or antenna system.