Polycarbonate Substrate Manufacturer
Polycarbonate Substrate Manufacturer,Polycarbonate substrates are versatile materials widely used in electronic and optical applications. Known for their excellent impact resistance and optical clarity, polycarbonate substrates offer a robust and durable solution for various devices. They are lightweight and provide good thermal stability, making them suitable for high-performance environments. These substrates are often utilized in the manufacturing of LED panels, display screens, and protective covers. Their ease of fabrication and ability to be molded into complex shapes contribute to their popularity in both consumer electronics and industrial applications, where durability and clarity are essential.
What is a Polycarbonate Substrate?
Polycarbonate substrates are thin, flexible sheets made from polycarbonate, a versatile and durable plastic material known for its high impact resistance, optical clarity, and thermal stability. These substrates are used in various applications across different industries, including electronics, automotive, Medizinisch, and packaging.
In electronics, polycarbonate substrates serve as a base material for manufacturing flexible printed circuit boards (Leiterplatten) and other electronic components. Their flexibility allows for the creation of intricate and compact circuit designs, which is essential in modern electronic devices like smartphones, Tabletten, and wearable technology. Zusätzlich, polycarbonate’s excellent dielectric properties and thermal resistance make it suitable for use in environments where electronic components are subjected to high temperatures and mechanical stress.
The automotive industry utilizes polycarbonate substrates for various interior and exterior applications, including instrument panels, display screens, and light covers. The material’s lightweight nature and high impact resistance contribute to enhanced vehicle safety and fuel efficiency.
In the medical field, polycarbonate substrates are employed in the production of medical devices and diagnostic equipment. The material’s biocompatibility, sterilizability, and resistance to chemicals and high temperatures make it ideal for use in environments that require stringent hygiene standards.
Polycarbonate substrates are also used in packaging applications due to their clarity, Haltbarkeit, and resistance to impact and heat. They provide excellent protection for products while allowing for easy inspection of the contents.
Insgesamt, polycarbonate substrates offer a combination of durability, Flexibilität, and optical clarity, making them a preferred choice in a wide range of applications. Their ability to withstand harsh conditions and maintain performance over time underscores their importance in advanced manufacturing and technological innovation.
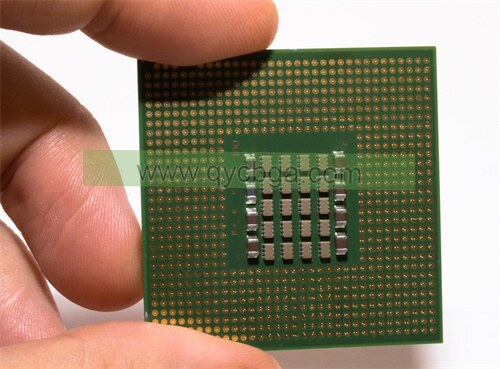
Polycarbonate Substrate Manufacturer
What is the Polycarbonate Substrate Design Guidelines?
Polycarbonate substrate design guidelines are crucial for ensuring that polycarbonate materials are effectively utilized in various applications, particularly in electronics, automotive, Medizinisch, and packaging sectors. These guidelines help optimize the performance and reliability of polycarbonate substrates. Here are some key design considerations:
- Thickness and Flexibility: Choose the substrate thickness based on the mechanical requirements of the application. Thicker substrates offer greater rigidity but less flexibility, while thinner substrates provide more flexibility but may be less robust. Ensure that the selected thickness balances mechanical strength and flexibility according to the application’s needs.
- Thermisches Management: Polycarbonate substrates have good thermal stability but can be affected by high temperatures. Design for adequate thermal management by incorporating heat dissipation features such as heat sinks or thermal pads if the substrate will be exposed to high temperatures.
- Optical Clarity and Coatings: For applications requiring optical clarity, such as display screens or lenses, ensure that the polycarbonate substrate is free from defects and has a smooth surface finish. Apply appropriate coatings to enhance scratch resistance, UV protection, and anti-reflective properties as needed.
- Electrical Insulation:When used in electronic applications, polycarbonate substrates should provide excellent electrical insulation. Ensure that the material’s dielectric properties meet the electrical requirements of the circuit or component.
- Chemical Resistance: Evaluate the potential exposure to chemicals and solvents. Polycarbonate substrates are generally resistant to many chemicals but may degrade under prolonged exposure to strong acids, bases, or organic solvents. Design with protective coatings or barriers if necessary.
- 6. Mechanical Strength: Consider the impact resistance and tensile strength of the polycarbonate substrate. Reinforce or choose a substrate with higher mechanical strength for applications where the substrate will be subjected to physical stress or impact.
- Fabrication and Processing: Account for the fabrication processes, such as cutting, Bohrung, and molding. Polycarbonate substrates can be machined using standard techniques, but precision in cutting and forming is essential to avoid stress concentrations and maintain performance.
- Environmental Considerations: Assess the environmental conditions where the substrate will be used, including exposure to UV light, temperature fluctuations, and humidity. Design with appropriate protective measures to ensure longevity and performance under these conditions.
- Cost and Performance Trade-offs: Balance the cost of polycarbonate substrates with performance requirements. High-performance applications may require premium grades of polycarbonate, while less demanding applications might utilize standard grades to optimize cost.
By adhering to these design guidelines, you can ensure that polycarbonate substrates are effectively utilized and perform optimally in their intended applications.
What is the Polycarbonate Substrate Fabrication Process?
The polycarbonate substrate fabrication process involves several key steps to transform raw polycarbonate material into functional substrates used in various applications such as electronics, automotive, medizinprodukte, and packaging. Here is an overview of the typical fabrication process:
- Materialauswahl: Start by selecting high-quality polycarbonate resin that meets the specific requirements of the application. Polycarbonate resins come in different grades, so choose one that offers the desired mechanical, thermisch, and optical properties.
- Extrusion: The polycarbonate resin is first melted and formed into sheets or films through an extrusion process. In diesem Schritt, the resin is heated to a molten state and pushed through a die to create flat sheets or films of the required thickness. The extruded material is then cooled and cut into sheets of the desired size.
- Cutting and Shaping: The polycarbonate sheets are cut to the desired dimensions using techniques such as laser cutting, water jet cutting, or CNC machining. Precision cutting ensures that the substrates meet the exact specifications required for their intended use.
- Surface Treatment:Depending on the application, surface treatments may be applied to enhance the substrate’s properties. Common treatments include polishing for optical clarity, coating for UV protection, anti-scratch, or anti-reflective properties. Surface treatment improves the performance and durability of the substrate.
- Drilling and Punching: For applications such as electronic circuit boards, polycarbonate substrates may need to be drilled or punched to create holes or cutouts for components and connections. This step requires precision to avoid damage to the substrate and ensure proper alignment of components.
- Lamination: In some cases, polycarbonate substrates are laminated with additional layers for added strength or functionality. This can include laminating with adhesive films, protective coatings, or other materials to achieve specific properties such as enhanced impact resistance or thermal insulation.
- Thermal Forming: For certain applications, the polycarbonate substrate may need to be thermoformed into specific shapes or contours. This involves heating the substrate until it becomes pliable and then molding it into the desired shape using various forming techniques.
- Quality Control and Inspection: Rigorous quality control is essential to ensure that the fabricated polycarbonate substrates meet the required standards. This includes inspecting the material for defects, verifying dimensions, and testing mechanical and optical properties.
- Assembly and Integration:The final polycarbonate substrates are then assembled or integrated into their end-use products. This may involve further processing such as bonding, soldering, or fitting with other components, depending on the application.
- Verpackung und Versand: Once the substrates are completed and inspected, they are carefully packaged to prevent damage during transportation and shipped to customers or manufacturers for further use.
By following these fabrication steps, manufacturers can produce high-quality polycarbonate substrates tailored to specific applications, ensuring optimal performance and durability in their end products.
How do you Manufacture a Polycarbonate Substrate?
Manufacturing a polycarbonate substrate involves several key steps to transform polycarbonate resin into a finished substrate ready for use in various applications. Here’s a detailed overview of the manufacturing process:
- Materialauswahl: Choose high-quality polycarbonate resin based on the desired properties for the substrate. Polycarbonate resins are available in various grades, so select one that meets the requirements for mechanical strength, Thermische Stabilität, optical clarity, or other specific needs.
- Compounding: The selected polycarbonate resin is compounded, which involves mixing it with additives such as colorants, UV stabilizers, or flame retardants. This process ensures that the resin has the required properties and performance characteristics.
- Extrusion: The compounded polycarbonate resin is heated until it melts and is then forced through an extrusion die to form sheets or films. During extrusion, the molten resin is shaped into flat sheets of the desired thickness. The material is cooled and solidified, then cut into standard sizes.
- Annealing: To relieve internal stresses and improve dimensional stability, the extruded sheets or films may undergo annealing. This heat treatment process involves heating the polycarbonate to a specific temperature and then cooling it slowly to reduce residual stresses.
- Cutting and Shaping: The polycarbonate sheets are cut to the required dimensions using techniques such as laser cutting, water jet cutting, or CNC machining. This step ensures that the substrates meet precise size and shape specifications.
- Surface Treatment: Depending on the intended application, surface treatments may be applied to enhance the substrate’s properties. Common treatments include coating with anti-scratch, UV-resistant, or anti-reflective coatings. These treatments improve the substrate’s durability and performance.
- Drilling and Punching: For applications that require holes or cutouts, such as electronic circuit boards, the polycarbonate substrate is drilled or punched with precision equipment. This step is crucial for ensuring that components fit correctly and the substrate performs as intended.
- Lamination: In some cases, the polycarbonate substrate is laminated with additional layers or films. This can provide extra protection, enhance mechanical strength, or improve specific performance characteristics. Laminating can be done using adhesive films or other materials.
- Thermoforming: For substrates that need to be shaped or contoured, thermoforming is used. The polycarbonate sheet is heated until it becomes pliable, then molded into the desired shape using forming tools. This step is essential for creating substrates with complex geometries.
- Quality Control: Rigorous quality control measures are implemented throughout the manufacturing process to ensure that the polycarbonate substrates meet required specifications. This includes inspecting the substrates for defects, verifying dimensions, and testing for mechanical and optical properties.
- Assembly and Integration:Once the polycarbonate substrates are manufactured and inspected, they are assembled or integrated into final products. This might involve further processes such as bonding, fitting with other components, or final adjustments.
- Verpackung und Versand: Finally, the finished polycarbonate substrates are carefully packaged to protect them during transportation. Proper packaging ensures that the substrates arrive at their destination in good condition.
Indem Sie diese Fertigungsschritte befolgen, producers can create high-quality polycarbonate substrates that meet specific performance and application requirements, ensuring their effectiveness and reliability in various end-use scenarios.
How Much Should a Polycarbonate Substrate Cost?
The cost of a polycarbonate substrate can vary widely depending on several factors. Here’s a breakdown of the main elements that influence the price:
- Material Grade: High-quality or specialized polycarbonate grades, such as those with enhanced optical clarity or specific chemical resistance, will typically cost more than standard grades.
- Thickness and Size: Thicker substrates and larger sheet sizes generally come at a higher cost due to increased material usage and processing requirements.
- Surface Treatment: Additional treatments such as UV coating, anti-scratch layers, or anti-reflective coatings add to the cost of the substrate. These treatments improve performance but also increase manufacturing expenses.
- Production Volume: Bulk orders usually benefit from economies of scale, reducing the per-unit cost. Smaller quantities or custom orders may be more expensive due to higher production costs and setup fees.
- Complexity of Fabrication:Processes such as precision cutting, Bohrung, or thermoforming can add to the cost, particularly if complex shapes or detailed specifications are required.
- Supplier and Region: Prices can vary based on the supplier’s pricing strategy and geographic location. Costs might differ between regions due to factors like local material costs, labor rates, and shipping expenses.
- Quality and Certification: Substrates meeting high-quality standards or specific certifications (zum Beispiel., for medical use or automotive safety) might command higher prices.
For accurate pricing, it’s best to consult with suppliers or manufacturers who can provide quotes based on specific requirements and order details.
What is Polycarbonate Substrate Base Material?
Polycarbonate substrate base material refers to the fundamental polycarbonate resin used as the primary material for fabricating substrates. This base material is crucial for determining the properties and performance of the final substrate. Here’s a detailed overview of polycarbonate substrate base material:
- Material Composition: Polycarbonate substrates are made from polycarbonate resin, a high-performance thermoplastic polymer. The base material consists primarily of polycarbonate polymer, which is known for its strength, Haltbarkeit, and optical clarity. It is synthesized through the polymerization of bisphenol A (BPA) and phosgene.
- Physical Properties: Polycarbonate base material is characterized by its:
– Impact Resistance: High resistance to impact and mechanical stress, making it suitable for applications requiring durability.
– Optical Clarity: Excellent transparency and clarity, often used in applications where visibility or light transmission is important.
– Thermal Stability: Good thermal stability, with a high glass transition temperature, allowing it to withstand varying temperatures.
– Dimensional Stability: Maintains its shape and size over a wide range of temperatures and conditions.
- Mechanical Properties: The base material exhibits high tensile strength, rigidity, and resistance to deformation. These properties are essential for applications requiring structural integrity and mechanical reliability.
- Chemical Resistance: Polycarbonate base material is resistant to many chemicals but may be affected by strong acids, bases, or organic solvents. Understanding its chemical compatibility is important for applications involving exposure to various substances.
- Processing Characteristics: The polycarbonate resin is thermoplastic, meaning it can be heated and re-melted without significant degradation. This allows for various fabrication techniques such as extrusion, injection molding, and thermoforming.
- Applications: Polycarbonate base material is used in a wide range of applications, einschließlich:
– Electronics: As a substrate for flexible printed circuit boards (Leiterplatten) and other electronic components.
– Automotive: For components such as instrument panels, light covers, and window glazing.
– Medizinprodukte: In devices requiring biocompatibility and sterilizability.
– Packaging: For transparent and impact-resistant packaging solutions.
- Grades and Variants: Different grades of polycarbonate resin are available to meet specific requirements. These include standard grades, impact-resistant grades, flame-retardant grades, and high-temperature grades, each tailored for particular applications.
- Environmental Considerations: Polycarbonate substrates can be recycled, but their environmental impact should be considered in terms of disposal and sustainability. Efforts to enhance recycling processes and develop more environmentally friendly variants are ongoing.
Zusammenfassend, the polycarbonate substrate base material is a versatile and high-performance thermoplastic polymer with properties that make it suitable for a variety of demanding applications. Its impact resistance, optical clarity, and thermal stability are key factors that contribute to its widespread use across different industries.
Which Company Makes Polycarbonate Substrates?
Several leading companies around the world manufacture polycarbonate substrates, catering to various industries such as electronics, automotive, Medizinisch, and packaging. Here are some notable manufacturers:
- Bayer MaterialScience: As a leading global producer of polycarbonate materials, Bayer offers various high-performance polycarbonate products, including substrates for the electronics and automotive industries. Bayer’s products are renowned for their excellent physical properties and reliability.
- SABIC: SABIC produces a range of polycarbonate materials, including transparent and flame-retardant grades. Its polycarbonate substrates are widely used in electronics, Medizinisch, and construction applications.
- Teijin: Teijin focuses on high-performance plastics and composites, with its polycarbonate substrates excelling in electronics and industrial applications. Teijin’s materials are known for their outstanding mechanical strength and thermal stability.
- Covestro: Covestro is another major supplier in the polycarbonate sector, offering a variety of polycarbonate products that are used to manufacture high transparency and high-impact resistance substrates. Covestro’s polycarbonate materials are suitable for multiple industries, including automotive and electronic devices.
- LG Chem: LG Chem provides various polycarbonate substrates for the electronics and display industries. Their products feature excellent optical performance and durability, making them suitable for high-demand applications.
- Asahi Kasei: Asahi Kasei produces polycarbonate materials used in medical devices and packaging. Their substrates are recognized for their high quality and reliability.
In addition to these well-known companies, our company also manufactures polycarbonate substrates. We possess advanced production equipment and technology, enabling us to provide high-quality polycarbonate substrates that meet various customer needs. Our products offer the following advantages:
- High Transparency:Our polycarbonate substrates feature excellent optical clarity, making them suitable for applications requiring high transparency, such as displays and optical devices.
- Superior Mechanical Properties: Our substrates exhibit excellent strength and toughness, capable of withstanding various mechanical stresses, ideal for applications requiring high impact resistance.
- Outstanding Thermal Stability:Our polycarbonate substrates have excellent thermal stability, maintaining performance in high-temperature environments, suitable for the electronics and automotive industries.
- Customization Services: We offer customized polycarbonate substrate solutions based on specific customer requirements, including different thicknesses, sizes, and surface treatments.
- Quality Control: We strictly control every aspect of the production process to ensure that each polycarbonate substrate meets high-quality standards.
With our expertise and production capabilities, we provide high-performance, high-quality polycarbonate substrates to support various application needs.
What Are the 7 Qualities of Good Customer Service?
Good customer service is crucial for building strong relationships with customers and ensuring their satisfaction. Here are seven key qualities that define excellent customer service:
- Responsiveness: Good customer service involves being prompt and attentive in addressing customer inquiries and concerns. Quick response times demonstrate that you value the customer’s time and are committed to resolving their issues efficiently. Whether it’s answering a phone call, responding to an email, or handling a live chat, being responsive shows that you are proactive and attentive.
- Empathy: Empathetic customer service means understanding and sharing the feelings of your customers. It involves listening to their concerns, acknowledging their emotions, and providing support in a compassionate manner. When customers feel that their concerns are understood and their problems are validated, it enhances their overall experience and builds trust.
- Knowledge and Expertise: Providing accurate and helpful information is a hallmark of good customer service. Representatives should have a deep understanding of the products or services offered and be able to provide clear, knowledgeable answers to customer questions. This expertise helps in resolving issues effectively and builds credibility with the customer.
- Patience: Patience is essential in customer service, especially when dealing with frustrated or confused customers. Taking the time to listen and address their concerns without rushing them shows respect and a commitment to finding the best solution. Patience helps in de-escalating tense situations and ensures that customers feel valued.
- Effective Communication: Clear and effective communication is crucial for good customer service. This includes not only conveying information accurately but also ensuring that it is done in a manner that is easy for the customer to understand. Good communication also involves active listening, which helps in accurately assessing and addressing customer needs.
- Consistency:Consistent customer service means providing the same level of quality and care in every interaction. This involves adhering to established service standards and ensuring that all customers receive a uniform experience, regardless of the representative or the channel used. Consistency builds reliability and trust with customers.
- Problem-Solving Skills: Effective problem-solving skills are vital for resolving customer issues. This involves identifying the root cause of the problem, exploring possible solutions, and implementing the most appropriate resolution. Good problem-solving ensures that customer concerns are addressed satisfactorily and can lead to improved processes and products.
Zusammenfassend, good customer service is characterized by responsiveness, empathy, knowledge, patience, effective communication, consistency, and problem-solving skills. These qualities work together to create positive customer experiences, foster loyalty, and enhance overall satisfaction.
FAQs
What is a polycarbonate substrate?
A polycarbonate substrate is a flat, rigid material made from polycarbonate resin, used as a base for various applications like electronic circuits, display panels, and protective covers. It offers high impact resistance, optical clarity, and thermal stability.
What are the typical thicknesses for polycarbonate substrates?
Polycarbonate substrates come in various thicknesses, typically ranging from 0.5 mm to 5 mm. The specific thickness depends on the application requirements and the desired mechanical properties.
Can polycarbonate substrates be customized?
Yes, polycarbonate substrates can be customized in terms of size, thickness, surface treatment, and other specifications to meet particular application needs.
Are polycarbonate substrates recyclable?
Yes, polycarbonate substrates can be recycled. Aber, the recycling process may vary depending on local regulations and facilities. It’s important to follow proper disposal and recycling practices to minimize environmental impact.
How should polycarbonate substrates be handled and stored?
Polycarbonate substrates should be handled carefully to avoid scratches and damage. They should be stored in a clean, dry environment away from direct sunlight and extreme temperatures to maintain their quality and performance.
What are the typical costs of polycarbonate substrates?
The cost of polycarbonate substrates depends on factors such as material grade, thickness, Größe, and additional treatments. Typischerweise, prices range from $5 An $50 per square meter, but it’s best to consult with suppliers for specific quotes based on your requirements.