Multilayer R&D PCB Manufacturer
Multilayer R&D PCB Manufacturer,Multilayer R&D PCBs are specialized printed circuit boards designed for research and development purposes. Featuring multiple layers of conductive material separated by insulating layers, these PCBs offer enhanced performance and flexibility for prototyping and testing electronic designs. They enable engineers and researchers to experiment with complex circuit layouts, high-density component placement, and advanced signal routing. Multilayer R&D PCBs facilitate iterative development, allowing for thorough testing and optimization of electronic systems before mass production. With their superior signal integrity and reduced electromagnetic interference, they play a crucial role in innovation and technological advancement.
What is a Multilayer R&D PCB?
A Multilayer R&D PCB refers to a printed circuit board (PLATINE) designed for research and development purposes, typically characterized by multiple layers of conductive material separated by insulating layers. These PCBs are used in the prototyping and testing phases of electronic product development.
The “multilayer” aspect denotes that the PCB has more than two layers of conductive material. These layers are interconnected through drilled holes called vias, allowing complex circuits to be designed with minimal space requirements. Multilayer PCBs offer advantages such as higher component density, better signal integrity, and reduced electromagnetic interference.
In the context of research and development (R&D), these PCBs are crucial for testing new electronic designs, evaluating performance, and identifying any issues or improvements needed before mass production. They allow engineers and researchers to experiment with different circuit layouts, components, and configurations without the need to manufacture custom single-purpose boards for each iteration.
Moreover, the “R&D” designation suggests that these PCBs may be tailored for specific research projects or experimental purposes. They might include features like test points, jumper pads, or specialized signal traces to facilitate debugging and data collection during testing phases.
Insgesamt, Multilayer R&D PCBs play a vital role in the innovation process by enabling efficient and iterative development of electronic devices and systems. Their flexibility and versatility make them indispensable tools for engineers and researchers working on cutting-edge technologies.
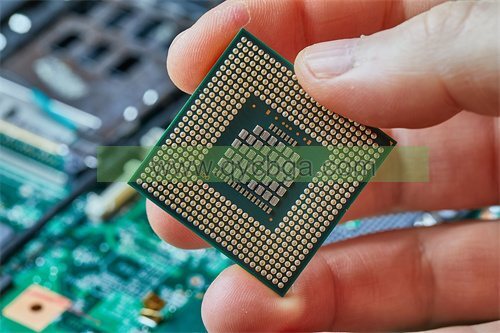
Multilayer R&D PCB Manufacturer
What are the Multilayer R&D PCB Design Guidelines?
Designing multilayer R&D PCBs requires careful consideration of various factors to ensure optimal performance, Zuverlässigkeit, and ease of testing. Here are some general guidelines for designing such PCBs:
- Layer Stackup:Plan the layer stackup carefully, considering signal integrity, Energieverteilung, und Thermomanagement. Assign signal layers, power planes, and ground planes strategically to minimize signal interference and maintain signal integrity.
- Signalintegrität: Follow best practices for signal integrity, such as minimizing trace lengths, controlling impedance, and avoiding signal crosstalk. Use proper termination techniques and ensure controlled impedance for high-speed signals.
- Component Placement: Place components strategically to minimize signal distortion and ensure efficient routing. Group related components together and consider the thermal implications of component placement for effective heat dissipation.
- Power Distribution: Design robust power distribution networks (PDNs) with low impedance paths to deliver clean power to all components. Use multiple power planes and bypass capacitors to minimize voltage fluctuations and noise.
- Grounding: Implement a solid grounding scheme to minimize ground loops and ensure a stable reference potential. Use ground planes effectively and connect all ground points directly to the ground plane to reduce ground bounce and noise.
- Routing: Follow good routing practices, such as minimizing trace lengths, maintaining uniform trace widths, and avoiding sharp corners. Route high-speed signals with controlled impedance and differential pairs with matched lengths.
- Thermisches Management: Design the PCB with adequate thermal relief and consider the placement of heat-generating components to facilitate heat dissipation. Use thermal vias and heat sinks as needed to manage thermal hotspots.
- Testability: Include test points, access points, and debug features to facilitate testing and troubleshooting during the R&D phase. Incorporate built-in self-test (BIST) features if applicable to automate testing procedures.
- Documentation: Document the design thoroughly, including schematic diagrams, layout files, fabrication notes, and assembly instructions. Maintain clear communication with manufacturers and assembly vendors to ensure accurate production.
- Compliance: Ensure compliance with relevant industry standards and regulations, such as IPC standards for PCB design and fabrication. Consider environmental factors, safety requirements, and electromagnetic compatibility (EMC) considerations.
By adhering to these guidelines, designers can create multilayer R&D PCBs that meet the performance, Zuverlässigkeit, and testing requirements of their research projects while enabling efficient development and prototyping processes.
What is the Multilayer R&D PCB Fabrication Process?
The fabrication process for multilayer R&D PCBs involves several steps, from design transfer to final inspection. Here’s an overview of the typical fabrication process:
- Design Transfer:The PCB design, usually created using software like Altium Designer or Eagle, is transferred to the fabrication house. This involves generating Gerber files, NC drill files, and fabrication drawings that contain all the necessary information for manufacturing.
- Materialauswahl:The fabrication house selects the appropriate materials for the PCB based on the design specifications, einschließlich des Trägermaterials (typically FR-4 epoxy fiberglass), copper foil thickness, and prepreg (Harz) thickness for the core and inner layers.
- Layer Preparation: The copper-clad laminate sheets are cleaned and prepared for the inner layer process. The layers are inspected for defects, and any necessary adjustments are made to ensure uniformity.
- Inner Layer Processing: The inner layers are coated with a photoresist material, onto which the circuit pattern is transferred using photolithography. After exposure to UV light through a mask, the unexposed areas are removed, leaving behind the circuit traces. The layers are then etched to remove excess copper.
- Layer Alignment and Lamination: Once the inner layers are processed, they are aligned and stacked together with prepreg layers to create the multilayer stack. The stack is then pressed under heat and pressure to bond the layers together, forming a solid panel.
- Drilling: Precision drills are used to create holes (Vias) that connect the traces between different layers. These vias are plated with copper to ensure electrical conductivity.
- Plating: A thin layer of copper is electroplated onto the surface of the panel to reinforce the circuit traces and provide a solderable surface.
- Outer Layer Processing: The outer layers are coated with photoresist and patterned using the same photolithography process as the inner layers. After etching, a protective solder mask is applied to the surface to protect the copper traces and facilitate soldering.
- Oberflächengüte: The PCB surface is treated with a surface finish to protect against oxidation and improve solderability. Common surface finishes include HASL (hot air solder leveling), ENIG (electroless nickel immersion gold), and OSP (organic solderability preservative).
- Silkscreen Printing: Finally, component designators, logos, and other markings are printed onto the PCB surface using a silkscreening process for identification and assembly guidance.
- Testing and Inspection: The fabricated PCBs undergo electrical testing to ensure that all connections are intact and that there are no short circuits or open circuits. Visual inspection is also performed to check for any defects or irregularities in the PCB surface.
- Panelization and Separation: If multiple PCBs are fabricated on a single panel, they are separated into individual boards using routing or V-scoring techniques.
- Final Inspection and Packaging: The finished PCBs are inspected one last time to ensure quality and adherence to specifications. They are then packaged and shipped to the customer or assembly house for component placement and soldering.
By following these steps, the fabrication house can produce high-quality multilayer R&D PCBs that meet the design requirements and specifications provided by the customer.
How do you manufacture a Multilayer R&D PCB?
Manufacturing a multilayer R&D PCB involves several steps, from designing the circuit to assembling the components. Here’s a detailed overview of the process:
- Designing the Circuit: The PCB design process begins with creating a schematic diagram of the circuit using PCB design software like Altium Designer, Eagle, or KiCad. Components are placed and connected logically to form the desired functionality.
- PCB Layout: Once the schematic is complete, the layout phase begins. Components are arranged on the PCB surface according to their electrical connections and mechanical constraints. Traces are routed between components to establish electrical connections, considering factors such as signal integrity, Energieverteilung, und Thermomanagement.
- Layer Stackup Design: For multilayer PCBs, the layer stackup is designed to accommodate the required number of signal layers, power planes, and ground planes. The stackup determines the arrangement of copper layers and insulating materials, optimizing signal integrity and electromagnetic compatibility.
- Gerber File Generation: After completing the PCB layout, Gerber files, NC drill files, and other manufacturing documentation are generated. These files contain the necessary information for fabricating the PCB, including copper traces, hole locations, solder mask layers, and silkscreen markings.
- Fabrication Preparation: The Gerber files and other manufacturing documents are sent to a PCB fabrication house for production. The fabrication house reviews the files and prepares the manufacturing process, including selecting appropriate materials and equipment.
- Inner Layer Processing: The fabrication process begins with preparing the inner layers of the PCB. Copper-clad laminate sheets are cleaned and coated with a photosensitive film. The circuit pattern is transferred onto the film using photolithography and etched to remove excess copper, leaving behind the traces.
- Layer Alignment and Lamination: After processing the inner layers, they are aligned and stacked together with prepreg layers to form the multilayer stack. The stack is then pressed under heat and pressure to bond the layers together, creating a solid panel.
- Drilling and Plating: Precision drills are used to create holes (Vias) that connect the traces between different layers. These vias are plated with copper to ensure electrical continuity. Through-holes and component mounting holes are also drilled at this stage.
- Outer Layer Processing: The outer layers of the PCB are processed similarly to the inner layers, with copper traces patterned using photolithography and etched to remove excess copper. A solder mask is applied to protect the copper traces and facilitate soldering, and silkscreen printing is used to add component designators and other markings.
- Oberflächengüte: The PCB surface is treated with a surface finish to protect against oxidation and improve solderability. Common surface finishes include HASL (hot air solder leveling), ENIG (electroless nickel immersion gold), and OSP (organic solderability preservative).
- Testing and Inspection: The fabricated PCB undergoes electrical testing to ensure all connections are intact and that there are no short circuits or open circuits. Visual inspection is also performed to check for defects or irregularities.
- Panelization and Separation: If multiple PCBs are fabricated on a single panel, they are separated into individual boards using routing or V-scoring techniques.
- Final Assembly: Once the PCBs pass inspection, they are ready for component assembly. Surface mount components are placed using pick-and-place machines, and through-hole components are inserted manually or using automated insertion equipment.
- Soldering: Components are soldered onto the PCB using reflow soldering or wave soldering techniques, depending on the type of components and assembly requirements.
- Testing and Quality Control: The assembled PCBs undergo functional testing to ensure they operate correctly. Additional quality control checks may include visual inspection, X-ray inspection, and automated optical inspection (AOI) to verify solder joints and component placement.
- Verpackung und Versand: Once the PCBs pass all tests and quality checks, they are packaged according to customer requirements and shipped to the end destination for integration into electronic devices or further testing.
By following these steps, manufacturers can produce high-quality multilayer R&D PCBs that meet the design specifications and performance requirements of their customers.
How much should a Multilayer R&D PCB cost?
The cost of a multilayer R&D PCB can vary widely depending on several factors. Given that R&D projects often involve unique designs and limited production runs, costs can be higher per unit compared to mass-produced PCBs. Here are some of the key factors that influence the cost:
- Number of Layers: The more layers a PCB has, the more complex and costly it is to manufacture. Each additional layer requires more material and additional processing steps for alignment, lamination, and drilling.
- Size of the PCB: Larger PCBs consume more materials and take up more space during manufacturing, which can increase the cost.
- Material Used: The type of substrate material (zum Beispiel., standard FR-4, high-frequency materials like Rogers), copper thickness, and other material choices impact the cost. Specialty materials cost more but might be necessary for high-performance applications.
- Complexity of Design: Complexity includes the density of the board, the number of components, the intricacy of routing, and the presence of special features like blind and buried vias, which require more advanced manufacturing processes.
- Oberflächengüte: Options like HASL, ENIG, and OSP vary in price, with ENIG generally being more expensive but providing better reliability for fine pitch components.
- Menge: Production volume significantly impacts cost. Prototypes are generally more expensive on a per-unit basis because the setup costs are distributed across fewer units. Ordering larger quantities can reduce the cost per PCB.
- Turnaround Time: Expedited orders increase costs. Faster turnaround times require prioritizing a specific job over others, potentially incurring overtime or special handling charges.
- Testing and Quality Requirements: Additional testing like electrical tests, Impedanzkontrolle, and thermal cycling can add to the cost. Higher standards for quality control and certification (zum Beispiel., for aerospace or medical applications) also increase production costs.
- Location of Manufacturing: The cost can vary depending on whether the PCBs are manufactured domestically or overseas. Offshore manufacturing might offer lower costs but can add logistics complexity and longer lead times.
To give a rough estimate, a simple 4-layer R&D PCB might cost anywhere from $50 An $200 for a small batch of prototypes, depending on the size and complexity. For more complex 8-layer or 10-layer designs, prices can range from $200 An $500 or more per board in low volumes. These prices can drop significantly in higher volumes.
For the most accurate pricing, it’s best to obtain quotes from several PCB manufacturers, providing them with complete design files and specifications. This will help you get a clearer picture of the costs involved and ensure that you find the best balance between cost, quality, and lead time suitable for your R&D project.
What is Multilayer R&D PCB base material?
The choice of base material for multilayer R&D PCBs depends on various factors, including the intended application, Leistungsanforderungen, and budget constraints. Aber, one of the most commonly used base materials for multilayer PCBs, including those used in research and development, is FR-4.
FR-4, or Flame Retardant 4, is a type of epoxy fiberglass material that provides excellent electrical insulation and mechanical strength. It consists of layers of woven fiberglass cloth impregnated with an epoxy resin binder. FR-4 is widely available, cost-effective, and suitable for a wide range of applications, making it a popular choice for multilayer PCBs.
In addition to FR-4, other base materials may be used for specialized applications or to meet specific performance requirements. Some examples include:
- High-Frequency Materials: For applications requiring enhanced signal integrity at high frequencies, specialized materials such as Rogers or Taconic laminates may be used. These materials offer lower dielectric constant and loss tangent, allowing for improved signal transmission and reduced signal distortion.
- High-Temperature Materials: In environments with elevated temperatures or demanding thermal requirements, base materials with enhanced thermal properties may be employed. These materials can withstand higher temperatures without significant degradation, ensuring reliability in harsh operating conditions.
- Flexible Materials: For flexible or bendable PCBs, flexible base materials like polyimide (zum Beispiel., Kapton) or liquid crystal polymer (LCP) are used. These materials offer flexibility and excellent mechanical properties, making them suitable for applications such as wearable electronics or curved displays.
- Metal Core Materials: In applications requiring efficient heat dissipation, metal core materials such as aluminum or copper-clad laminates may be used as the base material. These materials provide superior thermal conductivity, helping to dissipate heat generated by high-power components.
When selecting the base material for a multilayer R&D PCB, it’s essential to consider factors such as electrical performance, mechanical properties, thermal characteristics, und Wirtschaftlichkeit. The choice should be made based on the specific requirements of the application and the desired performance objectives. Zusätzlich, consulting with PCB manufacturers or materials suppliers can provide valuable insights into selecting the most suitable base material for your project.
Which company makes Multilayer R&D PCBs?
There are many companies specializing in the production of multilayer R&D PCBs, including well-known companies such as Foxconn, Eurocircuits, Texas Instruments, and LCSC. These companies have advanced manufacturing equipment, extensive experience, and professional teams, enabling them to provide high-quality multilayer R&D PCB products.
As a company focused on electronic manufacturing, we can also produce multilayer R&D PCBs. We have advanced production equipment and technology to meet various customer requirements for multilayer PCBs. Here are some advantages of multilayer R&D PCBs that we can provide:
- Customized Design: We can customize designs according to customer requirements, einschließlich der Anzahl der Schichten, Größe, materials, surface treatment, and other specifications. Whether it’s a simple double-layer PCB or a complex high-layer PCB, we can provide solutions that meet customer needs.
- Quality Assurance:We strictly adhere to international standards and industry regulations in production, ensuring stable and reliable product quality. We have a comprehensive quality management system, controlling every aspect from raw material procurement to production processing to ensure that products meet customer requirements.
- Fast Delivery:We have efficient production processes and flexible production schedules, enabling us to respond quickly to customer needs and provide timely delivery. Whether it’s small-scale sample production or large-scale orders, we can complete production on time and ensure product quality.
- Technical Support: We have a professional technical team and extensive experience, able to provide comprehensive technical support and solutions for customers. Whether it’s technical consultation during the design stage or problem-solving during the production process, we can provide timely assistance and support.
- Competitive Pricing: We are committed to providing customers with competitive prices while ensuring product quality and service levels. We focus on cost control and efficiency improvement, striving to create more value and benefits for customers.
Zusammenfassend, we have the equipment, technology, and experience required to produce multilayer R&D PCBs, providing customers with high-quality, customized products and excellent services. We are willing to work with customers to promote the development and progress of the electronic manufacturing industry.
What are the 7 qualities of good customer service?
Good customer service is characterized by several key qualities that contribute to positive interactions and relationships with customers. Here are seven essential qualities:
- Attentiveness: Good customer service begins with attentiveness. Customer service representatives should actively listen to customers, pay attention to their needs and concerns, and demonstrate empathy and understanding.
- Responsiveness:Customers appreciate prompt responses to their inquiries, whether through phone calls, emails, or social media channels. A quick response time demonstrates that the company values their time and is committed to addressing their issues promptly.
- Empathy: Empathy involves understanding and sharing the feelings of customers. Customer service representatives should put themselves in the customer’s shoes, acknowledge their emotions, and respond with compassion and understanding.
- Clarity: Clear communication is essential for effective customer service. Representatives should communicate information clearly and concisely, avoiding technical jargon or confusing language. Providing accurate and understandable explanations helps customers feel informed and empowered.
- Patience: Dealing with customer inquiries or complaints often requires patience, especially in challenging situations. Customer service representatives should remain calm, composed, and patient, even when faced with difficult customers or complex issues.
- Problem-solving skills: Good customer service involves resolving customer issues and complaints effectively. Representatives should possess strong problem-solving skills, identify root causes of problems, and offer practical solutions or alternatives to address customer concerns.
- Professionalism: Maintaining professionalism is essential in all customer interactions. Representatives should conduct themselves with professionalism, courtesy, and respect, regardless of the circumstances. Demonstrating professionalism fosters trust and confidence in the company and its services.
By embodying these qualities, companies can deliver exceptional customer service experiences that leave a positive impression on customers and contribute to long-term customer satisfaction and loyalty.
FAQs
What are the advantages of multilayer R&D PCBs?
Multilayer R&D PCBs offer higher component density, better signal integrity, reduced electromagnetic interference, and greater design flexibility compared to single or double-layer PCBs.
How are multilayer R&D PCBs different from standard PCBs?
Multilayer R&D PCBs are similar to standard PCBs but typically have more layers, allowing for more complex circuit designs and improved performance. They are often used in prototyping and testing phases of electronic product development.
What factors should be considered when designing multilayer R&D PCBs?
Design considerations include layer stackup, signal integrity, component placement, Energieverteilung, grounding, routing, Thermomanagement, testability, compliance with standards, and documentation.
What materials are used in multilayer R&D PCBs?
The base material is typically FR-4 epoxy fiberglass, but specialized materials like high-frequency laminates or flexible substrates may be used for specific applications.
How are multilayer R&D PCBs fabricated?
The fabrication process involves steps such as layer preparation, inner layer processing, layer alignment and lamination, drilling and plating, outer layer processing, surface finish, Testen, inspection, and final assembly.
What are the costs associated with multilayer R&D PCBs?
Costs vary depending on factors such as the number of layers, Größe, Kompliziertheit, material used, Menge, turnaround time, testing requirements, and location of manufacturing.
Where can I find a manufacturer for multilayer R&D PCBs?
Many PCB manufacturers specialize in multilayer R&D PCBs. Researching online, contacting industry associations, or seeking recommendations from colleagues can help identify suitable manufacturers.