Metal Substrate PCB Manufacturer
Metal Substrate PCB Manufacturer,Metal Substrate PCBs, also known as metal-core PCBs, are designed to provide superior thermal management and structural support for high-power and high-heat applications. These PCBs feature a metal base, typically aluminum or copper, which helps dissipate heat away from sensitive electronic components, ensuring reliable operation and longevity. The metal core is combined with a dielectric layer and a conductive copper layer to form a robust circuit board that supports efficient heat transfer and electrical performance. Metal Substrate PCBs are commonly used in LED lighting, Fahrzeugelektronik, and power supplies, where effective heat dissipation and durability are essential for optimal functionality.
What is a Metal Substrate PCB?
A Metal Substrate PCB, commonly referred to as IMS (Insulated Metal Substrate) PLATINE, is a type of printed circuit board designed to handle higher power densities and provide superior thermal management compared to traditional FR4 PCBs. Unlike standard PCBs, which are typically made with a fiberglass-reinforced epoxy laminate, metal substrate PCBs utilize a metal base, often aluminum or copper, as the primary material.
The structure of an IMS PCB consists of three layers: a metal base layer, an insulating dielectric layer, and a copper circuit layer. The metal base layer acts as a heat sink, efficiently dissipating heat generated by high-power components. The insulating dielectric layer provides electrical insulation between the metal base and the copper circuit layer, ensuring reliable operation and preventing short circuits. The copper circuit layer carries the electrical signals and components of the PCB.
The key advantage of IMS PCBs is their ability to manage heat more effectively, which is crucial for applications with high thermal loads, such as LED lighting, power electronics, and automotive electronics. By effectively transferring heat away from sensitive components, IMS PCBs help improve the reliability and longevity of electronic devices. Zusätzlich, they can be designed to be compact and lightweight, making them suitable for use in space-constrained environments.
Zusammenfassend, Metal Substrate PCBs offer enhanced thermal performance and durability, making them an ideal choice for high-power and high-heat applications.
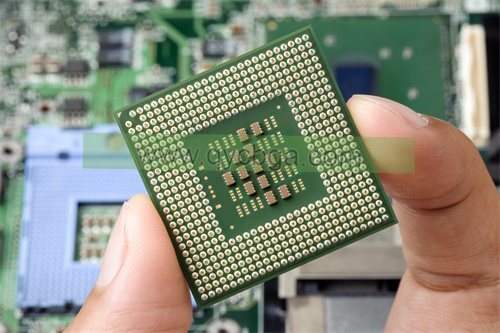
Metal Substrate PCB Manufacturer
What is the Metal Substrate PCB Design Guidelines?
Designing a Metal Substrate PCB (IMS PCB) requires specific considerations to maximize performance and ensure reliability. Here are some essential guidelines to follow:
- Thermisches Management: Proper heat dissipation is crucial for IMS PCBs. Ensure that the thermal vias are strategically placed to connect the heat-sensitive components to the metal base layer. The size and placement of these vias should be optimized to effectively spread heat across the metal substrate.
- Copper Thickness: Use an appropriate copper thickness for the circuit layer based on the current carrying requirements and thermal performance. Thicker copper layers can handle higher currents and dissipate more heat but may affect the board’s flexibility and cost.
- Thermal Pad Design: For components that generate significant heat, use large thermal pads and connect them to the metal base layer. This improves heat transfer and helps prevent thermal stress on the components.
- Insulation Considerations: Select a high-quality dielectric layer with good thermal conductivity and electrical insulation properties. Ensure that the insulation material is compatible with the metal base material and the operating temperature range of your application.
- Component Placement: Arrange high-power components to be close to the metal base layer for optimal heat dissipation. Avoid placing sensitive components directly above heat sources to prevent thermal damage.
- Layer Stack-Up: Design the layer stack-up carefully, considering the metal base layer, dielectric thickness, and copper layer requirements. The stack-up should support the mechanical and thermal performance needed for your specific application.
- Manufacturing Tolerances: Be aware of the tolerances for metal substrate PCBs, as the metal base layer and dielectric material can affect the final dimensions of the PCB. Ensure that your design accounts for these tolerances to avoid manufacturing issues.
- Testing and Validation: After fabrication, conduct thorough thermal and electrical testing to validate that the PCB performs as intended under real-world conditions. This step helps identify and address any issues related to heat management or electrical performance.
By adhering to these design guidelines, you can create an IMS PCB that effectively manages heat, supports high-power components, and maintains reliability throughout its lifecycle.
What is the Metal Substrate PCB Fabrication Process?
The fabrication process for Metal Substrate PCBs (IMS PCBs) involves several key steps to ensure the final product meets performance and reliability requirements. Here’s a detailed overview of the process:
- Material Preparation: Start with the metal base material, which is usually aluminum or copper. The metal base layer is cleaned and prepared to ensure proper adhesion of subsequent layers.
- Dielectric Layer Application: Apply a dielectric layer to the metal base. This layer is crucial for electrical insulation and thermal conductivity. The dielectric material is typically pre-preg (pre-impregnated with resin) and is bonded to the metal base layer through a lamination process.
- Copper Foil Lamination:Laminate a copper foil onto the dielectric layer. This step involves pressing the copper foil onto the dielectric material under heat and pressure to ensure a strong bond. The copper foil will form the circuit layer of the PCB.
- Photolithography: Use photolithography to define the circuit pattern. A photosensitive resist is applied to the copper layer, and the desired circuit pattern is exposed using UV light. The exposed areas are developed, revealing the copper that will form the circuit paths.
- Etching: Etch away the unwanted copper from the areas not protected by the resist. This process creates the electrical pathways on the PCB. The remaining resist is then removed, leaving behind the desired circuit pattern.
- Drilling and Plating: Drill holes for vias and component leads as required by the design. These holes are then plated with copper to create electrical connections between different layers of the PCB.
- Solder Mask Application: Apply a solder mask to protect the circuit traces and prevent solder from bridging between pads during assembly. The solder mask is applied as a liquid or film and cured to adhere to the PCB surface.
- Silkscreen Printing: Print silkscreen markings onto the PCB. This step involves applying text and symbols that provide component placement information and other details for assembly.
- Final Inspection:Conduct a thorough inspection to check for defects and ensure that the PCB meets design specifications. This may include electrical testing, visual inspection, and thermal testing.
- Cutting and Finishing: Cut the PCB to the final size and shape. Additional finishing processes may include edge plating, surface finish application (such as HASL, ENIG), and preparation for assembly.
- Testing and Quality Control: Perform final testing to verify the functionality and reliability of the PCB. This includes electrical tests to ensure that all connections are correct and thermal tests to confirm proper heat dissipation.
By following these fabrication steps, you can produce high-quality Metal Substrate PCBs that deliver excellent thermal management and electrical performance for demanding applications.
How do you manufacture a Metal Substrate PCB?
Manufacturing a Metal Substrate PCB (IMS PCB) involves several detailed steps to ensure proper construction and performance. Here’s a comprehensive guide to the process:
- Materialauswahl: Choose the appropriate metal base material (aluminum or copper) and dielectric layer (typically an insulating resin or ceramic). The selection depends on the thermal and electrical requirements of the application.
- Material Preparation: Prepare the metal base by cleaning and degreasing it to remove any contaminants. This ensures strong adhesion of the dielectric layer.
- Dielectric Layer Application: Apply the dielectric layer to the metal base. This can be done using a pre-impregnated resin (pre-preg) or a liquid resin that is later cured. The dielectric layer acts as an insulating and thermal transfer medium.
- Copper Foil Lamination: Laminate a thin copper foil onto the dielectric layer. This is typically done using a heat and pressure lamination process, where the copper foil is bonded to the dielectric layer under controlled conditions to ensure a strong adhesion.
- Pattern Transfer: Use photolithography to transfer the circuit design onto the copper layer. Apply a photosensitive resist, expose it to UV light through a mask of the circuit design, and develop it to reveal the copper areas to be etched away.
- Etching: Etch the exposed copper to create the circuit pattern. This is done by applying an etching solution that removes the unwanted copper, leaving the desired circuit traces.
- Drilling: Drill holes for vias and component leads as required by the design. These holes are necessary for electrical connections between different layers and for component mounting.
- Plating: Plate the drilled holes with copper to create electrical connections between layers (for multi-layer boards) and to provide a surface for soldering component leads. This process involves electroplating or electroless plating techniques.
- Solder Mask Application: Apply a solder mask over the circuit traces to prevent solder bridging and protect the copper traces from damage. The solder mask is typically a liquid or film that is cured after application.
- Silkscreen Printing: Print identifying marks, text, and symbols onto the PCB using a silkscreen process. This helps with component placement and identification during assembly.
- Final Inspection: Conduct a thorough inspection of the PCB. This includes checking for any manufacturing defects, ensuring proper circuit patterns, and verifying dimensions. Electrical tests may also be performed to check for continuity and functionality.
- Cutting and Finishing: Cut the PCB to its final size and shape. Apply any additional finishes such as edge plating or surface finishes (zum Beispiel., HASL, ENIG) to enhance solderability and protect the PCB.
- Assembly Preparation: Prepare the PCB for assembly, which may include adding mounting holes, component pads, and other features required for the final product.
By following these steps, manufacturers can produce high-quality Metal Substrate PCBs that provide effective thermal management and reliable electrical performance for demanding applications.
How much should a Metal Substrate PCB cost?
The cost of a Metal Substrate PCB (IMS PCB) can vary widely based on several factors, einschließlich:
- Material Costs: The type of metal used (Aluminium, Kupfer, etc.) and the dielectric material affect costs. High-quality or specialized materials may increase the price.
- Layer Count: The complexity of the PCB design, such as the number of layers and the thickness of each layer, impacts the cost. More layers generally increase the manufacturing cost.
- Copper Thickness: Thicker copper layers can handle higher currents and improve thermal performance but may also increase the cost.
- Board Size and Complexity: Larger and more complex PCBs with intricate designs or tighter tolerances will be more expensive to manufacture.
- Menge: The production volume can significantly affect the per-unit cost. Larger quantities typically result in lower per-unit costs due to economies of scale.
- Features: Additional features such as thermal vias, specific surface finishes, or custom shapes can add to the cost.
- Lead Time: Rush orders or expedited manufacturing processes may incur higher costs.
To get an accurate quote for a Metal Substrate PCB, it’s best to provide detailed specifications to PCB manufacturers. They can give you a precise estimate based on your design requirements and order quantity.
What is Metal Substrate PCB base material?
The base material of a Metal Substrate PCB (IMS PCB) consists of several key components that collectively ensure effective thermal management, electrical insulation, and structural integrity. Here’s a breakdown of the base material components:
- Metal Base Layer: The core of the Metal Substrate PCB is a metal base layer, usually made from aluminum or copper. This layer acts as a heat sink, providing excellent thermal conductivity to dissipate heat away from high-power components. Aluminum is commonly used due to its cost-effectiveness and good thermal properties, while copper offers superior thermal and electrical conductivity but at a higher cost.
- Dielektrische Schicht:The dielectric layer is applied directly on top of the metal base layer. It serves as an insulating medium between the metal and the copper circuit layer. The dielectric material must have good thermal conductivity to efficiently transfer heat from the copper layer to the metal base. Common dielectric materials include:
– Polyimid: Known for its excellent thermal stability and electrical insulation properties.
– Keramik: Offers high thermal conductivity and stability at elevated temperatures.
– Epoxy: A more cost-effective option with decent thermal and electrical properties.
- Copper Circuit Layer: Laminated onto the dielectric layer, this copper layer forms the circuit paths. It carries electrical signals and components and is etched to create the desired circuit pattern. The thickness of the copper layer can vary depending on the current-carrying requirements and thermal performance needs.
The construction of these layers is designed to provide optimal heat dissipation, electrical insulation, and mechanical support. The metal base layer’s primary function is to manage heat, while the dielectric layer ensures electrical isolation, and the copper layer facilitates electrical connections.
Zusammenfassend, the base material of a Metal Substrate PCB consists of a metal layer (typically aluminum or copper), a dielectric insulating layer, and a copper circuit layer. Each component plays a crucial role in ensuring the PCB’s performance in high-power and high-heat applications.
Which company makes Metal Substrate PCBs?
Many companies manufacture Metal Substrate PCBs, each with varying technology and production capabilities. Here are some notable manufacturers:
- AT&S: Based in Austria, AT&S is one of the leading global PCB manufacturers, offering various types of Metal Substrate PCBs, especially for high-power and high-heat management applications.
- Finisar: A major supplier in the optical communication sector, Finisar provides high-performance Metal Substrate PCBs suitable for various communication and electronic devices.
- Lingyin Technology:Based in China, Lingyin Technology specializes in high-frequency and high-heat load Metal Substrate PCBs, serving industries such as LED lighting, Fahrzeugelektronik, und Industrieelektronik.
- Cimtech: Cimtech offers a range of Metal Substrate PCB solutions, widely used in consumer electronics and industrial equipment.
- Zhen Ding Technology: A major PCB manufacturer in China, Zhen Ding Technology provides various PCB products, including Metal Substrate PCBs, primarily for automotive and consumer electronics applications.
- Advanced Circuits: Based in the USA, Advanced Circuits offers a range of PCB solutions, including Metal Substrate PCBs, aiming to meet high-quality and high-performance requirements.
Our company also manufactures Metal Substrate PCBs, offering the following features:
- Excellent Thermal Management: We use high-quality metal substrates (wie Aluminium oder Kupfer) to ensure effective thermal conductivity, helping to rapidly dissipate heat in high-power applications and improve the reliability and lifespan of electronic devices.
- High Precision Manufacturing: We employ advanced manufacturing technologies and equipment to ensure high precision and quality of Metal Substrate PCBs, meeting various design and performance requirements.
- Diverse Options: We provide different types of Metal Substrate PCBs based on customer needs, including single-layer and multi-layer structures suitable for applications in LED lighting, Fahrzeugelektronik, and power electronics.
- Custom Services:We offer custom design and manufacturing services according to specific customer requirements, including options for board size, copper thickness, Dielektrische Materialien, und mehr, ensuring the products meet special application needs.
- Comprehensive Quality Control: We rigorously control every stage of the production process to ensure high quality and reliability of the final products, with strict testing and inspection to meet industry standards.
Our Metal Substrate PCB solutions are suitable for various high-power and high-heat load applications, providing high-quality products and services. If you have any needs or questions, please feel free to contact us, and we will be happy to assist you.
What are the 7 qualities of good customer service?
Good customer service is crucial for maintaining customer satisfaction and loyalty. Here are seven key qualities that define excellent customer service:
- Empathy: Understanding and sharing the feelings of your customers is essential. Empathetic service involves listening to customers, recognizing their concerns, and addressing their needs with genuine care. This helps build a connection and makes customers feel valued.
- Responsiveness:Promptly addressing customer inquiries and issues is crucial. Quick response times demonstrate that you prioritize their concerns and are committed to resolving problems efficiently. This includes providing timely updates and follow-ups.
- Professionalism: Maintaining a professional demeanor at all times is vital. This includes being courteous, respectful, and knowledgeable. Professionalism helps build trust and ensures that interactions are positive and productive.
- Patience: Handling customer inquiries and complaints with patience is important, especially when dealing with frustrated or upset customers. Giving them the time and attention they need without rushing or becoming irritated shows respect and understanding.
- Clear Communication:Communicating clearly and effectively is essential. This involves using simple, jargon-free language, providing accurate information, and ensuring that customers fully understand the solutions or steps being offered. Good communication helps prevent misunderstandings and confusion.
- Problem-Solving Skills: The ability to address and resolve issues effectively is a key quality. This involves identifying the root cause of problems, offering viable solutions, and taking ownership of the resolution process. Strong problem-solving skills ensure that customer issues are resolved to their satisfaction.
- Follow-Up: Checking in with customers after resolving their issues to ensure their satisfaction demonstrates commitment to their overall experience. Follow-ups show that you care about their long-term satisfaction and are willing to go the extra mile to ensure their needs are met.
By embodying these qualities, businesses can deliver exceptional customer service that enhances customer satisfaction, fosters loyalty, and contributes to overall success.
FAQs
What is a Metal Substrate PCB?
A Metal Substrate PCB, also known as IMS (Insulated Metal Substrate) PLATINE, is a type of printed circuit board that uses a metal base, typically aluminum or copper, to improve heat dissipation. It consists of three layers: a metal base layer, an insulating dielectric layer, and a copper circuit layer.
What are the benefits of using Metal Substrate PCBs?
Metal Substrate PCBs offer superior thermal management, which helps dissipate heat more effectively than traditional FR4 PCBs. This makes them ideal for high-power applications, such as LED lighting and power electronics, where heat management is critical.
In which applications are Metal Substrate PCBs commonly used?
They are commonly used in applications that generate significant heat, such as LED lighting, power converters, Fahrzeugelektronik, and high-frequency circuits. Their ability to manage heat improves the reliability and performance of these devices.
What materials are used for the metal base in Metal Substrate PCBs?
The metal base is typically made of aluminum or copper. Aluminum is cost-effective and has good thermal conductivity, while copper provides superior thermal and electrical conductivity but is more expensive.
How are Metal Substrate PCBs different from traditional FR4 PCBs?
Unlike traditional FR4 PCBs, which use fiberglass-reinforced epoxy laminates, Metal Substrate PCBs use a metal base layer to enhance thermal management. This makes Metal Substrate PCBs better suited for applications with high thermal loads.
Can Metal Substrate PCBs be used for both single-layer and multi-layer designs?
Yes, Metal Substrate PCBs can be designed as single-layer or multi-layer boards. The choice depends on the complexity of the circuit and the specific requirements of the application.
What are the typical challenges in manufacturing Metal Substrate PCBs?
Challenges include ensuring proper adhesion between the metal base and the dielectric layer, managing thermal expansion differences between layers, and maintaining precision in drilling and etching. High-quality manufacturing processes are essential to address these challenges.