77G Millimeter Wave Radar PCB Manufacturer
77G Millimeter Wave Radar PCB Manufacturer,77G millimeter-wave radar PCBs are specifically designed to support millimeter-wave radar systems operating at approximately 77 GHz frequency. These high-performance PCBs utilize special materials and design techniques to ensure signal integrity and stability in high-frequency environments. Widely used in automotive advanced driver-assistance systems (ADAS) such as collision avoidance and blind-spot detection, these PCBs enable precise target detection and tracking functionalities.
What is a 77G Millimeter Wave Radar PCB?
A 77G Millimeter Wave Radar PCB (Printed Circuit Board) is a specialized type of circuit board designed to support the operation of millimeter wave radar systems that operate at frequencies around 77 GHz. This type of radar technology is commonly used in automotive applications, particularly in advanced driver-assistance systems (ADAS) for functions like collision avoidance, adaptive cruise control, and blind-spot detection.
The 77 GHz frequency band offers several advantages, including high resolution and accuracy, which are essential for the precise detection and measurement of objects in the vehicle’s surroundings. The use of such high frequencies allows the radar to detect smaller objects at greater distances and with better accuracy compared to lower frequency radars.
The PCB itself is critical in these applications because it hosts and interconnects all the electronic components necessary for the radar to function. This includes transmitters, receivers, antennas, and signal processing units. The design of a 77G Millimeter Wave Radar PCB must carefully consider aspects like material selection to minimize signal losses at high frequencies, layout to avoid interference among components, and thermal management to handle heat generated by the circuit.
High-frequency PCBs such as those used for 77G radar applications often use advanced materials like Rogers or Teflon-based laminates, which have lower dielectric losses and can support the integrity of the transmitted and received signals at millimeter-wave frequencies. Zusätzlich, these PCBs might feature sophisticated technologies such as HDI (High-Density Interconnect) to accommodate more functionality in a compact space, essential for automotive applications.
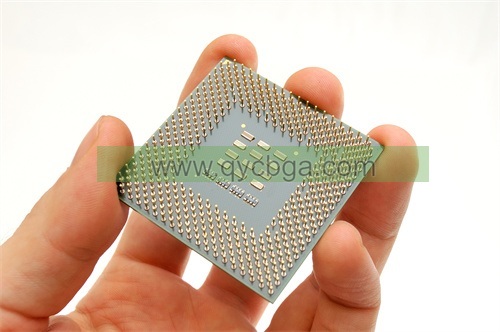
77G Millimeter Wave Radar PCB Manufacturer
What are the PCB Design Guidelines for 77G Millimeter Wave Radar PCB?
Designing a PCB for a 77G millimeter-wave radar system requires careful attention to various factors to ensure optimal performance. Here are some key guidelines:
- Materialauswahl: Choose PCB materials with low dielectric loss tangent and consistent dielectric constant across a wide frequency range. Materials like Rogers RO4000 series or Teflon-based laminates are commonly used for their excellent high-frequency performance.
- Transmission Line Design: Use controlled impedance transmission lines to minimize signal distortion and reflections. Match the characteristic impedance of the transmission lines to the impedance of the radar system components (usually 50 ohms). This helps maintain signal integrity at high frequencies.
- Ground Plane Design: Ensure a solid ground plane beneath the transmission lines and critical components to provide a low-impedance return path for RF signals and reduce electromagnetic interference (EMI). Avoid routing high-frequency traces over splits or voids in the ground plane.
- Component Placement: Place critical components such as transceivers, antennas, and signal processing units close together to minimize signal path lengths and reduce parasitic capacitance and inductance. This helps maintain signal integrity and reduces losses.
- Signal Routing: Route high-frequency traces as short and direct as possible to minimize signal losses and reduce electromagnetic interference. Use wide traces to minimize impedance variations and reduce signal attenuation.
- Avoidance of Crosstalk: Maintain adequate spacing between high-speed signal traces to minimize crosstalk. Crosstalk can degrade signal quality and lead to erroneous readings in the radar system.
- Thermisches Management: Ensure proper thermal management to dissipate heat generated by active components such as transceivers and signal processors. Adequate heat sinking or thermal vias can help maintain component reliability and prevent thermal-induced performance degradation.
- EMI/EMC Considerations: Design the PCB layout to minimize electromagnetic interference (EMI) emissions and ensure compliance with electromagnetic compatibility (EMC) standards. This includes proper shielding, grounding, and filtering techniques.
- Testability: Design the PCB with test points and access to critical signals for ease of testing and debugging during development and manufacturing.
- Simulation and Prototyping: Use electromagnetic simulation tools to analyze the PCB layout and validate its performance at millimeter-wave frequencies before fabrication. Prototyping and testing are essential to verify the design’s functionality and performance in real-world conditions.
Following these guidelines will help ensure the successful design and implementation of a PCB for a 77G millimeter-wave radar system, meeting the stringent performance requirements of automotive applications.
What is the 77G Millimeter Wave Radar PCB Fabrication Process?
The fabrication process for a 77G millimeter-wave radar PCB involves several steps, from initial design to final production. Here’s a general overview of the process:
- Design Phase: The process begins with the design of the PCB layout using specialized PCB design software. During this phase, the designer follows the PCB design guidelines for 77G millimeter-wave radar systems, considering factors such as material selection, transmission line design, component placement, and signal routing.
- Materialauswahl: Once the design is finalized, the appropriate PCB materials are selected based on their dielectric properties, signal integrity, and thermal characteristics. Materials like Rogers RO4000 series or Teflon-based laminates are commonly used for high-frequency radar applications.
- Manufacturing Documentation: Detailed manufacturing documentation, including Gerber files, drill files, and assembly drawings, is generated from the PCB design files. This documentation provides instructions for the fabrication process.
- Preparation of Substrates: The selected PCB materials are prepared by cutting them to the required size and cleaning them to remove any contaminants that could affect the fabrication process.
- Inner Layer Processing: If the PCB has multiple layers, inner layers are fabricated first. This involves laminating copper foil onto both sides of the substrate, then etching away the excess copper to form the desired circuit patterns using photolithography and chemical etching processes.
- Drilling: After the inner layers are processed, precision CNC drilling machines are used to drill holes at specified locations for through-hole components and vias. Laser drilling may be used for microvias in high-density interconnect (HDI) Leiterplatten.
- Through-Hole Plating: Through-holes are plated with copper to provide electrical connectivity between different layers of the PCB. This is typically achieved through an electroplating process.
- Outer Layer Processing: Outer layers of the PCB are fabricated using a similar process to the inner layers, including laminating copper foil, applying photoresist, exposing the circuit patterns, and etching away the excess copper.
- Oberflächengüte: Once the circuit patterns are defined, the PCB surface is finished with a suitable surface treatment to protect the copper traces and ensure solderability. Common surface finishes include HASL (Hot Air Solder Leveling), ENIG (Electroless Nickel Immersion Gold), and OSP (Organic Solderability Preservatives).
- Solder Mask and Legend Printing:A solder mask is applied to the PCB surface to insulate the copper traces and prevent solder bridges during assembly. Legend printing is also applied to identify component locations and polarity markings.
- Quality Control: The fabricated PCBs undergo rigorous quality control checks to ensure they meet the required specifications and standards. This may include electrical testing, dimensional inspection, and visual inspection of the circuitry.
- Assembly: After fabrication, the PCBs are assembled with electronic components such as transceivers, antennas, and signal processing units using automated surface mount technology (SMT) or manual soldering techniques.
- Testing and Validation: The assembled PCBs undergo functional testing and validation to ensure they meet the performance requirements of the 77G millimeter-wave radar system. This may include RF testing, signal integrity analysis, and environmental testing.
- Final Inspection and Packaging: Once testing is complete, the PCBs are inspected for any defects and packaged according to customer requirements for shipping and installation in the radar systems.
Insgesamt, the fabrication process for a 77G millimeter-wave radar PCB requires precision and attention to detail to ensure the reliable performance of the radar system in automotive applications.
How do you manufacture a 77G Millimeter Wave Radar PCB?
Manufacturing a 77G millimeter-wave radar PCB involves a series of steps, from initial design to final assembly. Here’s an overview of the manufacturing process:
- Design Phase: The process starts with the design of the PCB layout using specialized software. Designers follow guidelines for high-frequency radar systems, considering factors like material selection, transmission line design, component placement, and signal routing.
- Materialauswahl: Based on the design requirements, suitable PCB materials are selected. Materials with low dielectric loss tangent and consistent properties across a wide frequency range, such as Rogers RO4000 series or Teflon-based laminates, are often chosen for millimeter-wave radar applications.
- Manufacturing Documentation: Detailed manufacturing documentation, including Gerber files, drill files, and assembly drawings, is generated from the PCB design files. This documentation guides the fabrication process.
- Preparation of Substrates: PCB materials are prepared by cutting them to the required size and cleaning them to remove contaminants.
- Inner Layer Processing: If the PCB is multilayered, inner layers are processed first. This involves laminating copper foil onto both sides of the substrate, applying photoresist, exposing the circuit patterns, and etching away the excess copper using photolithography and chemical etching processes.
- Drilling: Precision CNC drilling machines are used to drill holes at specified locations for through-hole components and vias. Laser drilling may be used for microvias in HDI PCBs.
- Through-Hole Plating: Through-holes are plated with copper to provide electrical connectivity between different layers of the PCB. This is typically achieved through an electroplating process.
- Outer Layer Processing: Outer layers of the PCB are processed similarly to inner layers, including laminating copper foil, applying photoresist, exposing the circuit patterns, and etching away the excess copper.
- Oberflächengüte: The PCB surface is finished with a suitable surface treatment to protect the copper traces and ensure solderability. Common surface finishes include HASL, ENIG, and OSP.
- Solder Mask and Legend Printing: A solder mask is applied to insulate the copper traces and prevent solder bridges during assembly. Legend printing is applied to identify component locations and markings.
- Quality Control: Fabricated PCBs undergo rigorous quality control checks, including electrical testing, dimensional inspection, and visual inspection of the circuitry.
- Assembly: After fabrication, the PCBs are assembled with electronic components such as transceivers, antennas, and signal processing units using SMT or manual soldering techniques.
- Testing and Validation: Assembled PCBs undergo functional testing and validation to ensure they meet performance requirements. This may include RF testing, signal integrity analysis, and environmental testing.
- Final Inspection and Packaging: PCBs are inspected for defects and packaged for shipping and installation in radar systems.
Während des gesamten Herstellungsprozesses, attention to detail, precision, and adherence to quality standards are essential to ensure the reliability and performance of the 77G millimeter-wave radar PCBs.
How much should a 77G Millimeter Wave Radar PCB cost?
The cost of a 77G millimeter-wave radar PCB can vary widely depending on several factors, einschließlich:
- Complexity: The complexity of the PCB design, einschließlich der Anzahl der Schichten, density of components, and sophistication of features such as controlled impedance traces and HDI technology, can significantly impact the cost.
- Materials: The choice of materials for the PCB can affect the cost. High-performance materials with superior dielectric properties, such as Rogers RO4000 series or Teflon-based laminates, may be more expensive than standard FR-4 materials.
- Herstellungsprozess: The manufacturing process involved in producing the PCB, including processes like multilayer lamination, precision drilling, and advanced surface finishes, kann die Kosten beeinflussen.
- Volume: The quantity of PCBs ordered can affect the unit cost. Larger production runs typically result in lower unit costs due to economies of scale.
- Supplier: The pricing structure of the PCB supplier or manufacturer, including factors like overhead costs, profit margins, and pricing policies, can also impact the final cost.
Given these variables, it’s challenging to provide a specific cost without detailed information about the PCB design specifications, materials, Herstellungsprozess, and volume. Aber, a rough estimate for a single 77G millimeter-wave radar PCB with moderate complexity and standard materials could range from several hundred to a few thousand dollars. For larger quantities or more complex designs, the cost per unit would likely decrease. It’s essential to obtain quotes from multiple PCB suppliers or manufacturers to compare prices and ensure competitiveness.
What is the base material used in 77G Millimeter Wave Radar PCB?
The base material used in 77G millimeter-wave radar PCBs is typically selected based on its dielectric properties, thermal performance, and suitability for high-frequency applications. Commonly used base materials for these PCBs include:
- Rogers RO4000 Series: This series of high-frequency laminates, such as RO4350B, RO4003C, and RO3003, are popular choices for millimeter-wave radar PCBs. These materials offer low dielectric loss, consistent electrical properties over a wide frequency range, and excellent thermal stability.
- Teflon-Based Laminates:Laminates based on Teflon (polytetrafluoroethylene or PTFE) are known for their low dielectric constant, low loss tangent, and stable electrical properties at high frequencies. These materials, often branded as “Teflon PCBs,” are suitable for demanding millimeter-wave radar applications.
- Arlon Materials: Arlon materials, such as AD250 and AD255, are engineered for high-frequency applications and offer low loss, tight dielectric constant control, and good thermal performance. These materials are commonly used in radar systems and other RF/microwave applications.
- Isola FR408: FR408 is a high-performance, lead-free PCB material with low dielectric loss and excellent signal integrity characteristics. While not specifically designed for millimeter-wave frequencies, it can still be suitable for certain radar applications.
These base materials are chosen for their ability to maintain signal integrity, minimize signal losses, and provide reliable performance at the high frequencies used in millimeter-wave radar systems. Zusätzlich, they often have good thermal conductivity properties, which help dissipate heat generated by active components on the PCB. The specific choice of base material depends on the design requirements, performance goals, and cost considerations of the radar system.
Which companies make 77G Millimeter Wave Radar PCBs?
There are many companies that manufacture 77G millimeter-wave radar PCBs. Some well-known companies include:
- Rogers Corporation: As a leading global manufacturer of high-performance materials, Rogers Corporation offers a variety of PCB materials suitable for high-frequency applications, such as the RO4000 series and RO3000 series, which are widely used in the manufacturing of millimeter-wave radar PCBs.
- Isola Group: Isola Group is a supplier focused on high-performance PCB materials. Their products include series like FR408, Tachyon, and TerraGreen, which exhibit excellent performance in high-frequency environments and are suitable for millimeter-wave radar systems.
- Arlon Electronic Materials: Arlon Electronic Materials produces series like AD250 and AD255, which offer outstanding high-frequency performance and thermal stability, making them suitable for radar systems and other high-frequency applications.
Zusätzlich, there are many other suppliers that offer similar high-performance PCB materials suitable for manufacturing 77G millimeter-wave radar systems.
As for our company, we have advanced PCB manufacturing equipment and technology to produce high-performance 77G millimeter-wave radar PCBs. Our manufacturing process adheres strictly to engineering standards and quality control procedures to ensure the stability and reliability of PCB performance. Our engineering team has extensive experience and expertise in PCB design, Materialauswahl, und Herstellungsverfahren, enabling us to provide technical support and optimization suggestions. We can customize PCBs according to customer requirements, including layer count, materials, and special process requirements, to meet performance and reliability requirements in different application scenarios. Please feel free to contact us for more detailed information about the 77G millimeter-wave radar PCBs manufactured by our company.
What are the 7 qualities of good customer service?
Good customer service is characterized by several key qualities that contribute to positive interactions and satisfaction for customers. Here are seven qualities of good customer service:
- Responsiveness: Good customer service involves promptly addressing customer inquiries, concerns, and requests. Responsiveness demonstrates that the company values the customer’s time and is committed to providing timely assistance.
- Empathy: Empathy involves understanding and acknowledging the customer’s feelings, concerns, and perspective. It requires customer service representatives to listen actively, show compassion, and demonstrate understanding, even in challenging situations.
- Clear Communication: Effective communication is essential for good customer service. Customer service representatives should communicate clearly, using language that is easy to understand, and provide relevant information or instructions to address the customer’s needs or questions.
- Professionalism: Professionalism entails maintaining a courteous and respectful demeanor when interacting with customers. Customer service representatives should demonstrate competence, integrity, and reliability in their actions and communication.
- Problem-Solving Skills: Good customer service involves being proactive in resolving customer issues or complaints. Customer service representatives should possess strong problem-solving skills, be resourceful, and take initiative to find solutions that meet the customer’s needs.
- Adaptability:Adaptability is crucial for providing good customer service in diverse situations. Customer service representatives should be flexible and able to adjust their approach based on the customer’s preferences, communication style, and unique circumstances.
- Consistency:Consistency is key to building trust and loyalty with customers. Good customer service requires maintaining consistent standards of service quality, regardless of the channel or touchpoint through which the customer interacts with the company.
By embodying these qualities, organizations can deliver exceptional customer service experiences that foster customer satisfaction, loyalty, and positive word-of-mouth recommendations.
FAQs
What is a 77G millimeter-wave radar PCB?
A 77G millimeter-wave radar PCB is a specialized printed circuit board designed to support the operation of millimeter-wave radar systems that operate at frequencies around 77 GHz. These PCBs are critical components in automotive applications, particularly in advanced driver-assistance systems (ADAS) for functions like collision avoidance and blind-spot detection.
What are the key features of 77G millimeter-wave radar PCBs?
Key features of 77G millimeter-wave radar PCBs include high-frequency performance, low signal loss, controlled impedance traces, and compatibility with advanced radar signal processing algorithms. These PCBs often incorporate specialized materials and design techniques to maintain signal integrity at millimeter-wave frequencies.
What materials are used in 77G millimeter-wave radar PCBs?
77G millimeter-wave radar PCBs commonly use high-performance materials such as Rogers RO4000 series or Teflon-based laminates. These materials offer low dielectric loss, consistent electrical properties, and excellent thermal stability, making them suitable for high-frequency radar applications.
What design considerations are important for 77G millimeter-wave radar PCBs?
Design considerations for 77G millimeter-wave radar PCBs include controlled impedance transmission lines, proper grounding techniques, signal routing optimization, Thermomanagement, and electromagnetic compatibility (EMC) considerations. These factors are critical for ensuring optimal performance and reliability of the radar system.
What are the applications of 77G millimeter-wave radar PCBs?
77G millimeter-wave radar PCBs are primarily used in automotive applications, particularly in advanced driver-assistance systems (ADAS). They enable functions such as adaptive cruise control, collision avoidance, lane departure warning, and blind-spot detection by accurately detecting and tracking objects in the vehicle’s surroundings.
How are 77G millimeter-wave radar PCBs manufactured?
The manufacturing process for 77G millimeter-wave radar PCBs involves several steps, including design, Materialauswahl, substrate preparation, circuit fabrication, Versammlung, Testen, und Qualitätskontrolle. Specialized techniques and materials are used to ensure high-frequency performance and reliability.
What are the advantages of using 77G millimeter-wave radar PCBs?
The advantages of using 77G millimeter-wave radar PCBs include high resolution, accuracy, and sensitivity in detecting objects, particularly small objects at greater distances. These PCBs enable advanced safety and driver-assistance features in vehicles, contributing to improved road safety and driver comfort.