Porcelain Ceramic Substrate Manufacturer
Porcelain Ceramic Substrate Manufacturer,Porcelain ceramic substrates are high-performance materials known for their excellent electrical insulation, mechanical strength, and thermal stability. Made from high-purity alumina, these substrates offer low dielectric loss and high thermal conductivity, making them ideal for applications in electronics, telecommunications, and automotive industries. The robust nature of porcelain ceramic allows it to withstand harsh environments and high temperatures without degrading, ensuring long-term reliability and performance. Additionally, its smooth surface finish and precise dimensional control make it suitable for fine-line circuitry and complex electronic assemblies. Porcelain ceramic substrates are essential components in the production of advanced electronic devices and systems.
What is a Porcelain Ceramic Substrate?
A porcelain ceramic substrate is a type of substrate material used for electronic components, known for its excellent thermal performance and mechanical strength. It is typically made from high-purity ceramic materials, such as alumina, aluminum nitride, or other oxides, and is formed through high-temperature sintering. Due to its unique physical and chemical properties, porcelain ceramic substrates perform exceptionally well in high-frequency and high-temperature applications.
The advantages of porcelain ceramic substrates include outstanding insulation properties, good thermal conductivity, and high chemical resistance. These characteristics make them particularly suitable for power devices, RF equipment, and LED lighting applications. Additionally, the thermal stability of porcelain ceramic substrates allows them to maintain stable electrical performance even in extreme environments.
The manufacturing process of porcelain ceramic substrates involves steps such as material selection, shaping, drying, and sintering. By precisely controlling the sintering temperature and duration, the desired density and strength can be achieved. The surface of porcelain ceramic substrates can also be treated to enhance adhesion with other materials, accommodating various packaging requirements.
In the electronics industry, porcelain ceramic substrates serve as a high-performance substrate material widely used in mobile communication, automotive electronics, and medical devices, contributing to the development of highly reliable electronic components. With advancements in technology, the application prospects of porcelain ceramic substrates will become even broader.
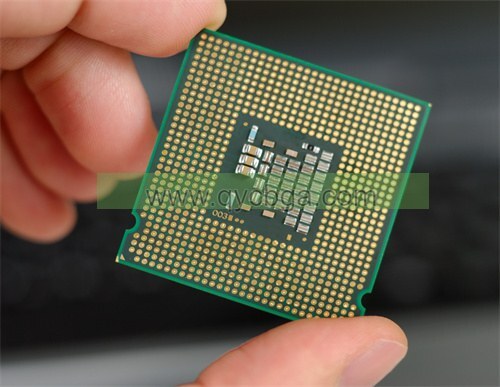
Porcelain Ceramic Substrate Manufacturer
What are the Porcelain Ceramic Substrate Design Guidelines?
Design guidelines for porcelain ceramic substrates focus on optimizing performance, reliability, and manufacturability. Here are some key considerations:
- Material Selection: Choose high-purity ceramic materials, such as alumina or aluminum nitride, based on thermal, electrical, and mechanical properties required for the application.
- Thickness: Determine appropriate substrate thickness to balance mechanical strength and thermal conductivity. Thicker substrates can provide better thermal management but may add weight.
- Layout Design: Ensure that traces and pads are designed with adequate spacing to prevent short circuits and ensure reliable electrical connections. Use standard trace widths to maintain consistent impedance.
- Via and Hole Design: Design vias and holes for mounting components carefully to ensure they meet thermal and electrical requirements. Use staggered vias to improve thermal conductivity.
- Thermal Management:Incorporate thermal vias and heat sinks in the design to enhance heat dissipation. Ensure that the layout facilitates optimal thermal flow.
- Surface Treatment: Consider surface treatments for improved adhesion to components and other substrates. Options include metallization for solderability or surface coatings for enhanced electrical performance.
- Fabrication Tolerances: Define tolerances for dimensions, flatness, and surface finish to ensure compatibility with assembly processes and component fit.
- Testing and Reliability: Plan for testing methods, such as thermal cycling and mechanical stress tests, to validate the reliability of the substrate in operational conditions.
- Manufacturing Considerations: Collaborate with manufacturers early in the design process to align on capabilities, limitations, and cost-effective fabrication techniques.
By following these guidelines, designers can create effective and reliable porcelain ceramic substrates for various high-performance applications.
What is the Porcelain Ceramic Substrate Fabrication Process?
The fabrication process of porcelain ceramic substrates involves several key steps, each critical to achieving the desired material properties and performance. Here’s an overview of the typical process:
- Material Preparation: High-purity ceramic powders (such as alumina or aluminum nitride) are sourced and prepared. These powders are often mixed with additives to enhance properties like sinterability and strength.
- Shaping: The ceramic powder mixture is shaped into the desired form using methods such as pressing (dry or isostatic) or tape casting. Pressing involves compacting the powder into molds, while tape casting involves creating thin ceramic sheets.
- Drying: The shaped green body is dried to remove excess moisture, ensuring it is sufficiently solid for the next processing steps. This step is crucial to prevent cracking during firing.
- Sintering: The dried ceramic body is heated in a furnace at high temperatures (typically 1200°C to 1700°C) to induce sintering. During this process, particles bond together, resulting in increased density and strength. The exact temperature and time depend on the specific ceramic material used.
- Machining: After sintering, the substrate may be machined to achieve precise dimensions and surface finishes. Techniques such as diamond grinding or laser cutting may be used to create features like vias and pads.
- Surface Treatment:Optional surface treatments can be applied to enhance properties such as adhesion for soldering or electrical performance. This may include metallization or protective coatings.
- Inspection and Testing:The final substrates undergo rigorous inspection and testing to ensure they meet specifications for dimensions, surface quality, and performance characteristics. This may include mechanical testing, thermal analysis, and electrical testing.
- Packaging and Delivery: Once approved, the substrates are packaged appropriately for delivery to customers, ensuring they remain protected during transportation.
By carefully controlling each step of the fabrication process, manufacturers can produce high-quality porcelain ceramic substrates suitable for demanding applications in electronics, automotive, and other fields.
How do you manufacture a Porcelain Ceramic Substrate?
Manufacturing a porcelain ceramic substrate involves several key steps, ensuring optimal material properties and performance. Here’s an overview of the typical process:
- Material Selection:High-purity ceramic powders, such as alumina or aluminum nitride, are chosen based on required thermal, electrical, and mechanical properties.
- Powder Preparation:The ceramic powders are mixed with additives that enhance sinterability and improve the final product’s properties. This mixture is often blended thoroughly to ensure uniformity.
- Shaping:The ceramic powder mixture is formed into the desired shape using techniques like pressing (either dry or isostatic) or tape casting. Pressing involves compacting the powder in molds, while tape casting produces thin sheets.
- Drying:The shaped green body is dried to remove moisture, which is crucial to avoid cracking during the subsequent firing stage. Controlled drying conditions are used to achieve uniform moisture removal.
- Sintering:The dried ceramic body is subjected to high-temperature firing (typically between 1200°C and 1700°C) in a furnace. This process allows particles to bond and densify, resulting in improved mechanical strength and thermal stability.
- 6. Machining:After sintering, the substrate may be machined to achieve precise dimensions and surface finishes. Techniques such as diamond grinding or laser cutting are commonly used to create specific features like vias and pads.
- Surface Treatment:Optional surface treatments may be applied to enhance properties like adhesion for soldering or electrical performance. This can include metallization or protective coatings.
- Quality Control:The finished substrates undergo thorough inspection and testing to ensure they meet specifications for dimensions, surface quality, and performance. This may involve mechanical testing, thermal analysis, and electrical performance evaluations.
- Packaging and Delivery:Once quality checks are complete, the substrates are packaged carefully to protect them during transportation and are delivered to customers.
By meticulously managing each step of the manufacturing process, high-quality porcelain ceramic substrates can be produced for use in advanced electronic applications, ensuring reliability and performance.
How much should a Porcelain Ceramic Substrate cost?
The cost of a porcelain ceramic substrate can vary significantly based on several factors, including:
- Material Quality: Higher purity and specialized materials may cost more.
- Size and Thickness: Larger or thicker substrates typically increase the cost.
- Manufacturing Process: The complexity of the fabrication process and the required precision can affect pricing.
- Quantity: Bulk orders often reduce the per-unit cost.
- Customization: Custom features or specifications may add to the price.
Generally, prices can range from a few dollars to several hundred dollars per substrate. For precise pricing, it’s best to consult manufacturers or suppliers, as they can provide quotes based on specific requirements and order quantities.
What is Porcelain Ceramic Substrate base material?
The base material for porcelain ceramic substrates typically consists of high-purity ceramic compounds. Common materials include:
- Alumina (Al2O3): Known for its excellent electrical insulation, thermal conductivity, and mechanical strength, alumina is one of the most widely used materials for ceramic substrates.
- Aluminum Nitride (AlN): This material offers superior thermal conductivity and is often used in high-power applications, particularly where efficient heat dissipation is crucial.
- Silicon Nitride (Si3N4): Known for its high strength and thermal shock resistance, silicon nitride is another option used in specialized applications.
- Other Oxides: Various other ceramic oxides may be used depending on specific application requirements, such as zirconia or titania.
These materials are chosen for their electrical, thermal, and mechanical properties, making them suitable for high-performance applications in electronics, automotive, and other industries.
Which company makes Porcelain Ceramic Substrates?
Many companies manufacture porcelain ceramic substrates, primarily focused on electronic components, automotive electronics, and high-power applications. Some well-known companies include:
- Murata Manufacturing Co., Ltd.: As a leading global manufacturer of electronic components, Murata has extensive experience in ceramic substrates, offering various types used in mobile communications, computers, and consumer electronics.
- Kyocera Corporation: Kyocera is renowned for its research and manufacturing of ceramic materials, especially in high-temperature and high-frequency applications.
- NGK Insulators, Ltd.: This company specializes in high-performance ceramic materials and provides various ceramic substrates suitable for different industrial applications.
- Yageo Corporation: Yageo also holds a position in the passive components and ceramic substrates market, offering a range of ceramic substrate solutions to meet diverse market needs.
In addition to these companies, many smaller manufacturers focused on ceramic substrate technology are driving innovation and development in this field.
Our company also manufactures porcelain ceramic substrates, equipped with advanced manufacturing technologies and facilities to provide high-quality, high-performance products. Our manufacturing process encompasses selecting high-purity ceramic materials, precise shaping, sintering, and subsequent processing, ensuring that each substrate meets strict customer requirements.
We emphasize controlling every aspect of the production process to guarantee high quality and stability. We offer customization services, allowing us to adjust substrate dimensions, thickness, and surface treatments according to specific customer needs to fit various applications.
Moreover, our porcelain ceramic substrates exhibit excellent thermal conductivity, electrical insulation, and mechanical strength, making them widely used in high-tech fields such as LED lighting, power devices, and RF equipment. Our products undergo rigorous quality testing to ensure reliability and durability under various operating conditions.
Overall, our company possesses rich experience and technical expertise in producing porcelain ceramic substrates, enabling us to provide high-quality products and excellent service, helping customers gain a competitive edge in the market. Please feel free to contact us for more information!
What are the 7 qualities of good customer service?
Good customer service is characterized by several key qualities that enhance customer satisfaction and loyalty. Here are seven important qualities:
- Responsiveness: Timely responses to customer inquiries and issues show that you value their time and concerns.
- Empathy: Understanding and addressing the customer’s feelings and perspectives helps build a strong connection and trust.
- Knowledge: Staff should be well-informed about products and services, enabling them to provide accurate and helpful information to customers.
- Politeness: Courteous and respectful communication creates a positive experience and reflects well on the company.
- Problem-Solving Skills: The ability to effectively address and resolve issues demonstrates commitment to customer satisfaction and can turn negative experiences into positive ones.
- Consistency: Providing reliable service consistently ensures that customers know what to expect, fostering trust and loyalty.
- Follow-Up: Checking in with customers after their issue is resolved shows that you care about their experience and are committed to continuous improvement.
These qualities, when practiced consistently, can lead to higher customer satisfaction and long-term loyalty.
FAQs
What is a porcelain ceramic substrate?
A porcelain ceramic substrate is a high-purity ceramic material used in electronic applications, known for its excellent electrical insulation, thermal conductivity, and mechanical strength.
What are the common applications for porcelain ceramic substrates?
They are widely used in LED lighting, power devices, RF components, automotive electronics, and other high-performance electronic applications.
What materials are used to make porcelain ceramic substrates?
Common materials include alumina (Al2O3), aluminum nitride (AlN), and other ceramic oxides, depending on the required properties for specific applications.
What are the benefits of using porcelain ceramic substrates?
Benefits include high thermal conductivity, excellent electrical insulation, chemical resistance, and high mechanical strength, making them suitable for demanding environments.
How are porcelain ceramic substrates manufactured?
The manufacturing process involves steps such as powder preparation, shaping, drying, sintering, machining, and optional surface treatments.
Can porcelain ceramic substrates be customized?
Yes, they can be customized in terms of dimensions, thickness, surface treatments, and specific features to meet unique application requirements.
What is the typical cost of porcelain ceramic substrates?
Prices can vary based on factors such as material quality, size, thickness, and manufacturing complexity. It’s best to consult manufacturers for specific pricing.