What is Rigid-Flex Package Substrate?
ผู้ผลิตพื้นผิวแพ็คเกจ Rigid-Flex,Rigid-flex package substrate combines the benefits of rigid and flexible circuit boards to create a versatile and reliable solution for complex electronic assemblies. It consists of multiple layers of rigid and flexible substrates laminated together, allowing for three-dimensional configurations and dynamic bending. This hybrid design offers excellent mechanical stability, reduced interconnects, and enhanced signal integrity. Rigid-flex substrates are ideal for applications requiring high reliability and compact form factors, such as aerospace, อุปกรณ์ทางการแพทย์, และอุปกรณ์อิเล็กทรอนิกส์สําหรับผู้บริโภค. Their ability to withstand harsh environments and repeated flexing makes them suitable for advanced, high-density electronic packaging where space and performance are critical.
In traditional PCB manufacturing, the substrate is rigid, meaning it cannot bend or flex easily. อย่างไรก็ตาม, in certain applications where space is limited or where flexibility is required, such as in wearable devices or foldable electronics, rigid-flex package substrates are used.
A rigid-flex package substrate combines both rigid and flexible components into a single substrate. This allows the PCB to bend and flex without compromising its structural integrity or functionality. Rigid-flex substrates typically consist of alternating layers of rigid and flexible materials, such as FR-4 (a type of fiberglass-reinforced epoxy laminate) for the rigid sections and polyimide or polyester for the flexible sections.
The use of rigid-flex package substrates enables designers to create more compact and lightweight electronic devices with complex geometries, while also improving reliability by reducing the need for connectors and solder joints that can be points of failure in traditional rigid PCB assemblies.
Rigid-Flex Package Substrate design Reference Guide.
“Rigid-Flex Package Substrate Design Reference Guide” is a handbook that provides detailed guidance and reference materials on how to design and utilize rigid-flex package substrates. This guide may include the following:
- Overview of Rigid-Flex Package Substrates: Introduction to the basic concepts, structure, and application scope of rigid-flex package substrates.
- Design Principles and Best Practices: Provide principles, best practices, and considerations to follow when designing rigid-flex package substrates. This may include layout and routing recommendations, interconnection methods, fold region design, etc.
- Material Selection and Performance Requirements: Introduction to the types of materials used in rigid-flex package substrates, their performance characteristics, and how to select suitable materials to meet the requirements of specific applications.
- Manufacturing Processes and Techniques: Explanation of the manufacturing processes, techniques, and methods involved in producing rigid-flex package substrates, including lamination, hole plating, metallization, folding, การทดสอบ, etc.
- Design Cases and Case Studies: Provide practical design cases and case studies of rigid-flex package substrates to help readers better understand the design process and application practices.
- 6. Reference Materials and Resource Links: Provide relevant literature, standards, specifications, as well as links to suppliers and manufacturers to further understand the design and application of rigid-flex package substrates.
This guide aims to provide comprehensive reference materials for engineers, designers, and manufacturers to follow best practices in designing and manufacturing rigid-flex package substrates, ensuring the performance, ความน่าเชื่อถือ, and quality of products.
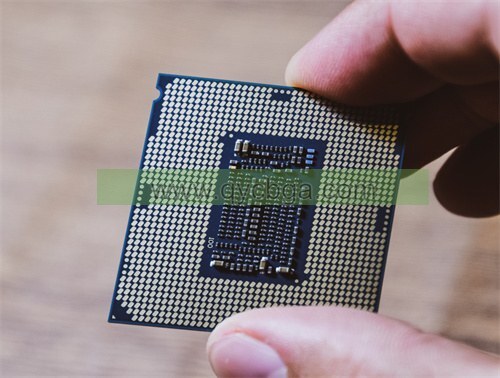
ผู้ผลิตพื้นผิวแพ็คเกจ Rigid-Flex
What are the materials used in Rigid-Flex Package Substrate?
Rigid-flex package substrates incorporate a combination of materials to achieve the desired properties of rigidity and flexibility. The materials commonly used in rigid-flex substrates include:
- Rigid Materials:
– FR-4: This is a widely used material for rigid portions of the substrate. FR-4 is a type of fiberglass-reinforced epoxy laminate known for its durability, เสถียรภาพทางความร้อน, and electrical insulation properties.
– Rigid polyimide (PI): Polyimide films are also used for rigid sections. They offer excellent thermal stability, chemical resistance, และความเสถียรของมิติ.
– Rigid polyester (PET): Polyester films can be used in rigid sections, offering good mechanical properties and chemical resistance.
- Flexible Materials:
– โพลีอิไมด์ (PI): Polyimide films, such as Kapton, are commonly used for flexible portions of the substrate due to their flexibility, high-temperature resistance, and excellent electrical insulation properties.
– Polyester (PET): Flexible polyester films are also used for their flexibility and mechanical strength. They are often used as an alternative to polyimide in less demanding applications.
– พอลิเมอร์คริสตัลเหลว (แอลซีพี): LCP films are becoming increasingly popular for flexible substrates due to their exceptional electrical properties, low moisture absorption, and high-temperature resistance.
- Adhesive Materials:
– Adhesive films: Various adhesive films are used to bond the rigid and flexible layers together. These adhesives should have good adhesion to both rigid and flexible materials and provide mechanical stability while allowing for flexibility.
- Conductive Materials:
– Copper foil: Copper foil is used for conductive traces on both rigid and flexible sections of the substrate. Copper is preferred for its excellent electrical conductivity and compatibility with standard PCB manufacturing processes.
– Conductive adhesives: In some cases, conductive adhesives are used to bond components to the substrate or to create conductive pathways between layers.
These materials are carefully selected and engineered to meet the specific requirements of the application, such as mechanical flexibility, เสถียรภาพทางความร้อน, ประสิทธิภาพทางไฟฟ้า, และความน่าเชื่อถือ. The combination of rigid and flexible materials in a single substrate allows for the creation of complex and compact electronic designs with improved durability and performance.
How is Rigid-Flex Package Substrate manufactured?
The manufacturing process for rigid-flex package substrates involves several steps to create a single substrate that combines both rigid and flexible sections. นี่คือภาพรวมทั่วไปของกระบวนการผลิต:
- Design and Layout: The first step is to design the layout of the rigid-flex substrate according to the requirements of the electronic device. This includes determining the placement of components, traces, and vias on both the rigid and flexible sections.
- การเลือกวัสดุ: Select appropriate materials for the rigid and flexible portions of the substrate, as well as the adhesive materials used to bond them together. วัสดุทั่วไป ได้แก่ FR-4, โพลีอิไมด์, polyester, copper foil, and adhesive films.
- Preparation of Rigid Materials:
– For rigid sections, FR-4 or other rigid substrates are prepared by cutting them to the required size and shape.
– Copper foil is typically laminated onto the rigid substrate to create conductive traces.
- Preparation of Flexible Materials:
– Flexible polyimide or polyester films are prepared by cutting them to size and shape.
– Copper foil may also be laminated onto the flexible films to create conductive traces.
- Layer Alignment and Bonding:
– The rigid and flexible layers are aligned and bonded together using adhesive films. This is typically done using heat and pressure to ensure a strong bond between the layers.
– The adhesive films are carefully selected to provide both mechanical stability and flexibility.
- Drilling and Plating:
– Through-holes (จุดร่วม) are drilled through the entire substrate to allow for electrical connections between different layers.
– The vias are then plated with copper to create conductive pathways between the layers.
- รูปแบบวงจร:
– Conductive traces are patterned on both the rigid and flexible sections using processes such as photolithography and etching.
– This involves applying a resist material, exposing it to UV light through a mask to define the circuit pattern, and then etching away the unwanted copper.
- Component Assembly:
– Electronic components are assembled onto the substrate using surface mount technology (SMT) or other appropriate assembly methods.
– Conductive adhesives or solder paste may be used to attach components to the substrate.
- การทดสอบและการตรวจสอบ:
– The assembled substrate undergoes testing and inspection to ensure that it meets the required specifications and quality standards.
– ซึ่งอาจรวมถึงการทดสอบทางไฟฟ้า, visual inspection, and dimensional measurements.
- การตกแต่งขั้นสุดท้าย:
– The substrate may undergo additional processes such as coating or surface finishing to protect the circuitry and enhance its performance or appearance.
The specific details of the manufacturing process may vary depending on factors such as the complexity of the design, the materials used, and the requirements of the application. ทั้งหมด, the manufacturing of rigid-flex package substrates requires careful attention to detail and precision to create reliable and high-performance electronic assemblies.
The Application area of Rigid-Flex Package Substrate
Rigid-flex package substrates find applications in various industries where there’s a need for electronic devices that require both rigidity and flexibility. พื้นที่การใช้งานทั่วไปบางส่วน ได้แก่:
- เครื่องใช้ไฟฟ้า:
– Smartphones: Rigid-flex substrates are used in the construction of flexible displays, allowing for foldable or curved screen designs.
– Wearable Devices: Flexible substrates enable the creation of comfortable and wearable electronics, such as fitness trackers and smartwatches.
– Portable Devices: Rigid-flex substrates are used in devices like tablets and e-readers, where space and weight savings are crucial.
- Medical Devices:
– Implantable Devices: Rigid-flex substrates are used in medical implants and monitoring devices, where flexibility is required to conform to the body’s contours.
– Wearable Health Monitors: Flexible substrates enable the development of wearable health monitoring devices that can track vital signs and provide real-time feedback.
- อิเล็กทรอนิกส์ยานยนต์:
– In-Vehicle Displays: Rigid-flex substrates are used in automotive displays and infotainment systems, where they can conform to the shape of the dashboard or other interior surfaces.
– Sensors and Control Systems: Flexible substrates are used in sensors and control systems throughout vehicles, where they can withstand vibrations and temperature variations.
- Aerospace and Defense:
– Avionics: Rigid-flex substrates are used in aircraft instrumentation, ระบบเรดาร์, and communication equipment, where they can withstand harsh environmental conditions.
– Military Electronics: Flexible substrates are used in military applications such as unmanned aerial vehicles (UAVs), wearable electronics for soldiers, and ruggedized communication devices.
- Industrial Automation:
– Control Systems: Rigid-flex substrates are used in industrial automation equipment, วิทยาการหุ่นยนต์, and manufacturing machinery, where they can provide reliable electrical connections in tight spaces.
– Sensing and Monitoring: Flexible substrates enable the integration of sensors and monitoring devices into industrial equipment for condition monitoring and predictive maintenance.
- IoT (Internet of Things):
– Connected Devices: Rigid-flex substrates are used in IoT devices such as smart sensors, environmental monitors, and connected appliances, where they can provide flexibility for diverse form factors and deployment scenarios.
– Smart Infrastructure: Flexible substrates enable the integration of sensors and communication modules into infrastructure components such as buildings, bridges, and roadways for smart city applications.
ทั้งหมด, rigid-flex package substrates play a crucial role in enabling the development of innovative electronic devices across a wide range of industries, where their unique combination of rigidity and flexibility meets the demands of modern technology requirements.
What are the advantages of Rigid-Flex Package Substrate?
Rigid-flex package substrates offer several advantages over traditional rigid PCBs or flexible circuits. ข้อได้เปรียบที่สําคัญบางประการ ได้แก่:
- Space Savings: Rigid-flex substrates allow for the integration of multiple rigid and flexible sections into a single substrate, reducing the need for connectors, cables, and additional PCBs. This can result in significant space savings, particularly in compact electronic devices where space is at a premium.
- Improved Reliability: By eliminating connectors and solder joints, rigid-flex substrates reduce the potential points of failure in electronic assemblies. This can improve the overall reliability and durability of the device, particularly in applications where the device may be subjected to mechanical stress or vibration.
- Enhanced Design Flexibility: Rigid-flex substrates offer greater design flexibility compared to traditional rigid PCBs. Designers can create complex geometries and incorporate bends, folds, and curves into the substrate, allowing for more innovative and ergonomic designs.
- Weight Reduction: Rigid-flex substrates are typically lighter than traditional rigid PCB assemblies, thanks to their reduced need for additional connectors and cables. This can be advantageous in applications where weight savings are critical, such as portable devices or aerospace applications.
- Improved Signal Integrity: Rigid-flex substrates can help mitigate signal integrity issues by reducing signal losses and electromagnetic interference (อีเอ็มไอ). The shorter signal paths and reduced impedance variations provided by rigid-flex substrates can lead to better signal quality and overall performance.
- Cost Savings: While the initial manufacturing cost of rigid-flex substrates may be higher compared to traditional rigid PCBs, they can result in cost savings over the product lifecycle. The reduction in assembly time, lower component count, and improved reliability can lead to lower maintenance and replacement costs over time.
- Environmental Resistance: Rigid-flex substrates can withstand a wide range of environmental conditions, including temperature extremes, moisture, and mechanical stress. This makes them well-suited for use in harsh environments such as automotive, อวกาศ, and industrial applications.
- Streamlined Assembly Process: Rigid-flex substrates simplify the assembly process by reducing the number of interconnects and solder joints required. This can lead to faster and more efficient assembly, resulting in shorter time to market for electronic products.
ทั้งหมด, the advantages of rigid-flex package substrates make them a preferred choice for a wide range of applications where space savings, ความน่าเชื่อถือ, and design flexibility are critical requirements.
How Much Does Rigid-Flex Package Substrate Cost?
The cost of rigid-flex package substrates can vary widely depending on several factors, including:
- ความซับซ้อนของการออกแบบ: The complexity of the rigid-flex substrate design, รวมถึงจํานวนชั้น, the size and shape of the substrate, and the complexity of the circuitry, can significantly impact the cost. More complex designs typically require more materials and manufacturing steps, leading to higher costs.
- Materials Used: The cost of materials, including rigid and flexible substrates, copper foil, adhesive materials, and surface finishes, can vary based on their quality, availability, and specifications. Higher-quality materials may be more expensive but can offer better performance and reliability.
- กระบวนการผลิต: The manufacturing process used to produce rigid-flex substrates can affect the overall cost. Some processes may be more labor-intensive or require specialized equipment, leading to higher production costs.
- ปริมาณการผลิต: The volume of rigid-flex substrates produced can impact the unit cost. ปริมาณที่สูงขึ้นมักนําไปสู่การประหยัดจากขนาด, ส่งผลให้ต้นทุนต่อหน่วยลดลง. Conversely, low-volume production runs may incur higher setup and tooling costs, driving up the overall cost per unit.
- ซัพพลายเออร์และที่ตั้ง: The choice of supplier and their location can also influence the cost of rigid-flex substrates. Suppliers in regions with lower labor and overhead costs may offer more competitive pricing.
- บริการเพิ่มเติม: บริการเพิ่มเติม เช่น การสนับสนุนการออกแบบ, prototyping, การทดสอบ, and assembly can add to the overall cost of rigid-flex substrates. These services may be necessary depending on the specific requirements of the project.
Due to the many variables involved, it’s challenging to provide a specific cost for rigid-flex package substrates without detailed information about the design, materials, กระบวนการผลิต, and volume of production. อย่างเป็นแบบฉบับ, companies interested in obtaining rigid-flex substrates would need to request quotes from manufacturers based on their specific requirements and project specifications.
คําถามที่พบบ่อย
What is a rigid-flex package substrate?
A rigid-flex package substrate is a type of substrate used in electronics packaging that combines rigid and flexible sections into a single integrated structure. It allows for compact, reliable, and flexible electronic assemblies.
What are the advantages of using rigid-flex package substrates?
Rigid-flex package substrates offer advantages such as space savings, improved reliability, enhanced design flexibility, streamlined assembly processes, reduced weight, improved signal integrity, and environmental resistance.
What industries commonly use rigid-flex package substrates?
Rigid-flex package substrates are used in a wide range of industries, including consumer electronics, อุปกรณ์ทางการแพทย์, อุปกรณ์อิเล็กทรอนิกส์ยานยนต์, aerospace and defense, telecommunications, industrial and manufacturing, energy, and renewable resources.
How are rigid-flex package substrates manufactured?
The manufacturing process for rigid-flex package substrates involves steps such as design preparation, material preparation, layer alignment and bonding, drilling and copper plating, circuit patterning, coverlay application, component assembly, การทดสอบและการตรวจสอบ, and final processing.
What materials are used in rigid-flex package substrates?
Rigid-flex package substrates use materials such as FR-4, โพลีอิไมด์, polyester, liquid crystal polymer (แอลซีพี), adhesive films, copper foils, coverlay films, and surface finishes like electroless nickel immersion gold (เอนิก).
What factors influence the cost of rigid-flex package substrates?
The cost of rigid-flex package substrates is influenced by factors such as design complexity, วัสดุที่ใช้, กระบวนการผลิต, quantities ordered, supplier/vendor pricing, and additional services required.
What considerations should be taken into account when designing with rigid-flex package substrates?
Designers should consider factors such as mechanical constraints, การจัดการความร้อน, signal integrity, ความน่าเชื่อถือ, manufacturability, and environmental requirements when designing with rigid-flex package substrates.
Are there any standards or guidelines for designing rigid-flex package substrates?
Yes, there are industry standards and guidelines, such as IPC-2223 for flex PCB design and IPC-2221 for rigid PCB design, that provide recommendations and best practices for designing rigid-flex package substrates.
What are common challenges associated with rigid-flex package substrate design and manufacturing?
Common challenges include ensuring proper bend radius and flex region design, managing thermal issues, maintaining signal integrity, minimizing manufacturing defects, and ensuring compatibility with assembly processes.
Where can I find suppliers or manufacturers of rigid-flex package substrates?
Suppliers and manufacturers of rigid-flex package substrates can be found through online directories, industry trade shows, referrals, and direct inquiries to companies specializing in PCB fabrication and assembly.